In the machinery industry, keeping contaminants out of critical components is vital for optimal performance and longevity. Traditional sealing methods often fall short, leading to reduced efficiency and costly downtime.
Labyrinth air purge seals provide a robust solution to this pervasive problem. By creating an intricate maze-like path, these advanced seals effectively prevent the ingress of dirt, dust, and other harmful particles.
In this comprehensive guide, we’ll dive deep into the world of labyrinth air purge seals, exploring their components, types, and working principles.
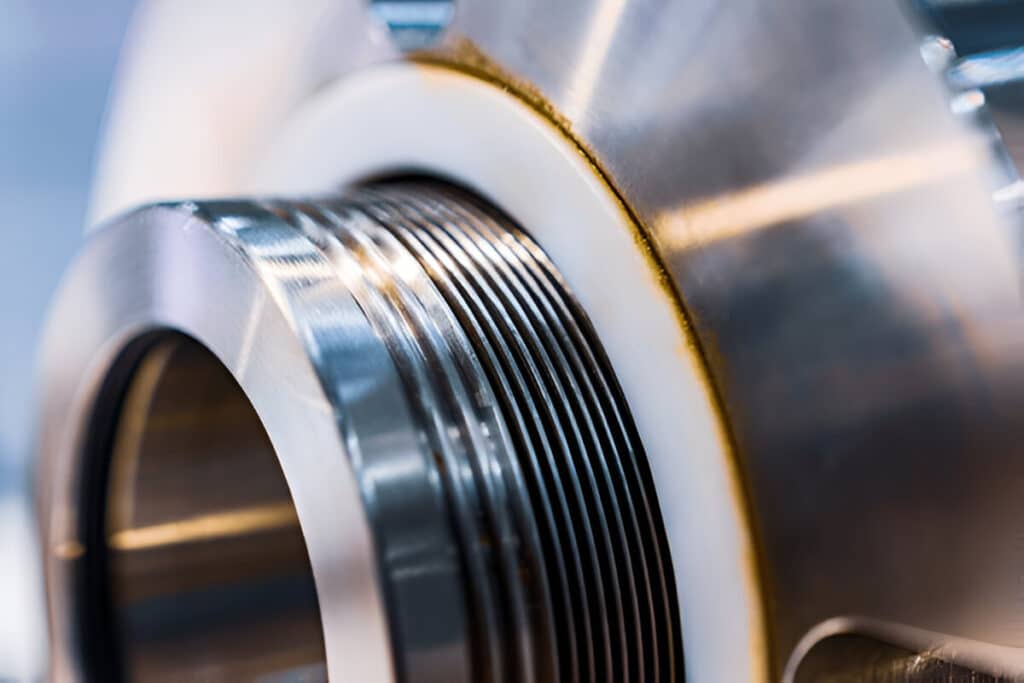
What is a Labyrinth Air Purge Seal
A labyrinth air purge seal is a specialized type of non-contacting mechanical seal designed to prevent the leakage of gases or fluids along a rotating shaft. It utilizes a complex maze-like pathway, known as a labyrinth, between the rotating and stationary components to create a highly effective sealing system.
At its core, a labyrinth seal consists of a series of grooves or teeth machined into the rotor and stator components. These grooves are arranged in a precise, alternating pattern that creates a tortuous path for the fluid or gas to navigate. As the medium attempts to pass through the seal, it encounters resistance due to the lengthy, convoluted route it must follow.
Components of Labyrinth Air Purge Seals
The primary components of a labyrinth air purge seal include:
- Rotor: The rotating part of the seal, typically attached to the shaft of the equipment. It features a series of teeth or knives that create the labyrinth path.
- Stator: The stationary part of the seal, usually mounted on the housing or casing of the equipment. It has corresponding grooves or chambers that match the rotor’s teeth.
- Labyrinth Path: The intricate maze-like path created by the interlocking teeth and grooves of the rotor and stator. This path is designed to create a tortuous flow path for the fluid, causing pressure drops and reducing leakage.
How Labyrinth Air Purge Seals Work
Labyrinth air purge seals provide an effective sealing solution through a complex maze-like path between the rotor and stator components. This labyrinth path is designed to create a series of pressure drops that gradually decrease the pressure of the fluid or gas as it attempts to pass through the seal.
The sealing action occurs as the high-pressure fluid enters the first chamber of the labyrinth. As it passes through the narrow clearances and sharp turns of the labyrinth, the fluid expands and its pressure decreases. This process repeats as the fluid navigates each subsequent chamber, with its pressure dropping further at each stage.
By the time the fluid reaches the last chamber, its pressure has decreased to near atmospheric conditions, effectively preventing leakage. The labyrinth design does not require any contact between the rotor and stator, minimizing friction and wear.
In air purge labyrinth seals, an additional sealing effect is achieved by introducing a purge gas, typically air, into the center of the labyrinth. This purge air is supplied at a pressure slightly higher than the process fluid, creating an outward flow that opposes the inward leakage of the process fluid.
As the purge air travels outward through the labyrinth, it mixes with and dilutes any process fluid that has leaked into the labyrinth. This mixture is then safely vented to the atmosphere, preventing contamination of the process fluid and enhancing the overall sealing efficiency.
Types of Labyrinth Seals
Standard Labyrinth Seals
Standard labyrinth seals are the most basic and widely used type. They consist of a series of alternating grooves and teeth machined into the rotor and stator components. As the fluid enters the labyrinth path, it encounters resistance from the frequent direction and velocity changes. This causes a pressure drop across each tooth, reducing leakage.
Standard labyrinth seals are typically made from metal alloys like stainless steel or brass. They offer good durability and can handle moderate temperatures and pressures.
Thermoplastic Labyrinth Seals
Thermoplastic labyrinth seals use high-performance plastics such as PTFE, PEEK, or nylon in place of traditional metal components. The flexible nature of these materials allows for tighter clearances between the rotor and stator without risk of contact or damage. Tighter clearances mean improved sealing efficiency. Thermoplastic seals also have a lower coefficient of friction, reducing heat generation and wear.
They excel in applications with thermal cycling or exposure to corrosive media. However, they have lower maximum temperature limits compared to metal seals.
Air Purge Labyrinth Seals
Air purge labyrinth seals introduce an additional sealing mechanism beyond the basic labyrinth path geometry. They inject a pressurized air or inert gas barrier into the center of the labyrinth. This purge flow opposes any process fluid trying to escape, providing a highly effective seal even with larger clearances. The purge gas also prevents contamination by creating a clean environment around the seal.
Air purge designs are ideal for high-speed equipment or applications with abrasive particles that could damage seal faces. The trade-off is increased complexity and the need for an external purge system.
Difference between Labyrinth Seals
Seal Type | Materials | Clearances | Sealing Mechanism | Temperature Range | Purge Required |
---|---|---|---|---|---|
Standard Labyrinth | Metal alloys | Moderate | Labyrinth path | -100°C to 500°C | No |
Thermoplastic Labyrinth | PTFE, PEEK, nylon | Tight | Labyrinth path | -100°C to 250°C | No |
Air Purge Labyrinth | Metal or thermoplastic | Larger | Labyrinth path + purge barrier | -100°C to 500°C | Yes |
Advantages of Labyrinth Air Purge Seals
Non-Contact Operation
Labyrinth air purge seals operate without any physical contact between the rotor and stator. This non-contact operation minimizes wear and tear, extending the seal’s lifespan and reducing maintenance requirements.
Low Friction and Heat Generation
Due to the absence of contact between the sealing surfaces, labyrinth air purge seals generate minimal friction and heat. This leads to improved energy efficiency and reduced thermal stress on the equipment.
High-Pressure Capability
The combination of the labyrinth path and the purge gas enables labyrinth air purge seals to handle high-pressure differentials effectively. They can maintain a reliable seal even under demanding process conditions.
Contamination Prevention
The positive pressure created by the purge gas prevents the ingress of contaminants into the sealed area.
Applications of Labyrinth Air Purge Seals
Aerospace Industry
In the aerospace industry, labyrinth air purge seals are used in aircraft engines, turbines, and other rotating equipment. They help prevent leakage of lubricants, coolants, and other fluids while operating at high speeds and temperatures.
Automotive Industry
Labyrinth air purge seals find application in automotive turbochargers, pumps, and compressors. They ensure reliable sealing and prevent oil or coolant leakage, even under the harsh operating conditions of automotive systems.
Oil and Gas Sector
The oil and gas industry relies on labyrinth air purge seals in various rotating equipment, such as pumps, compressors, and turbines. These seals help maintain process integrity, prevent fluid contamination, and minimize emissions in both upstream and downstream operations.
Industrial Equipment
Labyrinth air purge seals are widely used in industrial equipment, including gearboxes, blowers, and mixers. They provide effective sealing solutions for a range of industrial processes, ensuring equipment reliability and process efficiency.