Mechanical seals are critical components in industrial machinery, but improper maintenance can lead to premature failure and costly downtime.
Neglecting proper mechanical seal maintenance can result in leaks, contamination, overheating, excessive wear, and catastrophic failure. This not only disrupts production but can create safety hazards and require expensive repairs or replacements.
Fortunately, by following some key tips, you can significantly extend the life of your mechanical seals and keep your equipment running at peak performance. This guide will walk you through 14 critical aspects of mechanical seal maintenance, from lubrication and cleaning to monitoring and handling.
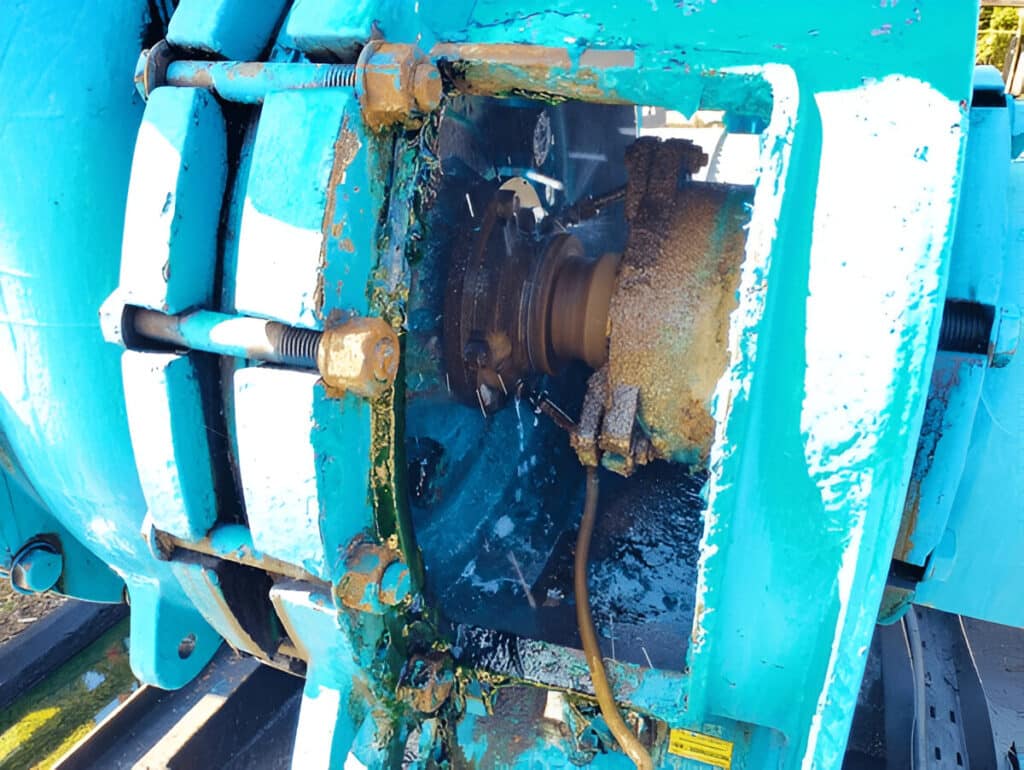
Lubrication
The lubricant fills the microscopic imperfections on the seal faces, providing a hydrodynamic film that separates the faces and reduces friction, heat generation, and wear. Use the correct type and amount of lubricant as specified by the seal manufacturer.
Regularly check the lubricant level and condition. Top off or replace the lubricant as needed to maintain the proper level. Contaminated, degraded, or incorrect lubricant can lead to premature seal failure.
Prevent Dry Running
Dry running occurs when a mechanical seal operates without adequate lubrication between the seal faces. This can happen during startup, shutdown, or upset conditions. Dry running leads to rapid overheating and damage to the seal faces, often resulting in seal failure.
To prevent dry running, ensure a stable supply of the sealed fluid to the seal faces. Use seal flush systems, barrier fluids, or quench fluids as appropriate. Monitor process parameters and interlock the seal with the pump to avoid running the seal dry.
Clean Seal Faces
Keep the seal faces clean and free from contaminants. Debris, solidified product, or reaction deposits on the seal faces can cause abrasion, increased leakage, and seal damage. Establish regular cleaning intervals based on the process fluid and operating conditions.
Use appropriate cleaning methods and solvents compatible with the seal materials. Avoid using abrasive tools or harsh chemicals that can scratch or degrade the seal faces. Inspect the seal faces after cleaning to ensure they are free of deposits and damage.
Control Contamination
Contaminants can enter the seal chamber from external sources or be generated internally by the process. Solid particles, abrasive dust, corrosive chemicals, and incompatible fluids can deteriorate seal materials and damage seal faces.
Implement effective contamination control measures. Use filters, cyclones, or magnetic separators to remove solid contaminants from the sealed fluid. Maintain a clean operating environment and prevent ingress of external contaminants. Monitor fluid quality and replace degraded fluids promptly.
Temperature Control
Maintain the proper operating temperature range for the mechanical seals. Excessive heat buildup accelerates lubricant breakdown and seal face wear. Overheated seals may warp or crack.
Use adequate cooling methods, such as seal coolers, heat exchangers, or circulation systems, to remove excess heat. Monitor the seal chamber and lubricant temperatures to ensure they remain within acceptable limits.
Pressure Management
Operate mechanical seals within their rated pressure range. Excessive pressure can distort the seal faces, disrupt the lubricating film, and cause leaks or failures. Insufficient pressure may allow process fluid to enter the seal chamber.
Ensure the seal is rated for the maximum operating pressure of the system. Use pressure relief valves, accumulators, or pressure control systems to maintain a stable pressure profile. Avoid dead-heading the pump or closing valves abruptly, which can create pressure shocks.
Vibration and Alignment Control
Minimize vibration and maintain proper alignment of the shaft and seal. Excessive vibration or misalignment can cause uneven face loading, leading to accelerated wear, face distortion, or seal failure.
Ensure the seal is rated for the maximum operating pressure of the system. Use pressure relief valves, accumulators, or pressure control systems to maintain a stable pressure profile. Avoid dead-heading the pump or closing valves abruptly, which can create pressure shocks.
Flush Systems
Use proper flushing systems to cool, lubricate, and clean the seal faces. Flushing helps control seal chamber temperature, remove heat, and flush away contaminants. Configure flush systems according to seal manufacturer recommendations.
Regularly inspect flush system components, such as filters, valves, and piping, for proper operation and cleanliness. Ensure adequate flush flow rate, pressure, and temperature control. Use filtration to maintain high flush fluid cleanliness levels.
Monitor Seal Performance
Implement condition monitoring to track mechanical seal performance and detect issues early. Monitoring parameters such as temperature, pressure, vibration, and leakage provides valuable diagnostic information to guide maintenance.
Use appropriate instrumentation, such as thermocouples, pressure transducers, or flow meters, to collect seal performance data. Set alert and alarm thresholds to provide early warning of developing problems.
Replace Worn Components
Periodically inspect mechanical seals for signs of wear and damage. Replace worn seal faces, springs, elastomers, and other components before they fail. Do not allow seals to operate with severely degraded parts.
Follow seal manufacturer guidelines for wear limits and replacement intervals. Consider upgrading to more wear-resistant face materials, such as silicon carbide or diamond coatings, for extended service life in abrasive or demanding applications.
Proper Installation
Install mechanical seals using the proper techniques, tools, and procedures. Precision alignment, correct bolt torque, proper lubrication, and clean assembly are all essential for reliable seal performance.
Follow the seal manufacturer’s detailed installation instructions. Use qualified personnel with mechanical seal training and experience. Verify the installation meets all specifications before startup.
Shaft Movement
Accommodate normal shaft movement with proper seal design and installation. Shaft runout, end play, and thermal growth can all affect seal performance if not properly addressed. Excessive movement can cause face contact, accelerated wear, and leakage.
Select seal designs that can tolerate the expected range of shaft movement. Use balanced seals, bellows seals, or other designs that can adapt to shaft movement. Ensure adequate clearances during installation. Use shaft stabilizing features, such as shaft shoulders or bushings.
Seal Support Systems
Seal support systems provide additional features to enhance seal performance and reliability. These systems include barrier fluid systems, buffer fluid systems, and seal gas supply systems. They help isolate the seal from the process fluid, provide lubrication, and control the seal environment.
Select the appropriate seal support system based on the process requirements and seal type. Ensure a reliable supply of the support fluid or gas at the specified pressure and flow rate.
Storage and Handling
Use proper storage and handling practices to prevent seal damage prior to installation. Store seals in a clean, dry, temperature-controlled environment. Protect seals from dirt, moisture, chemicals, and physical damage.
Follow seal manufacturer instructions for storage orientation, support, and protection. Limit seal storage time to avoid deterioration of elastomers and lubricants. Handle seals carefully using clean gloves and appropriate tools to prevent damage.