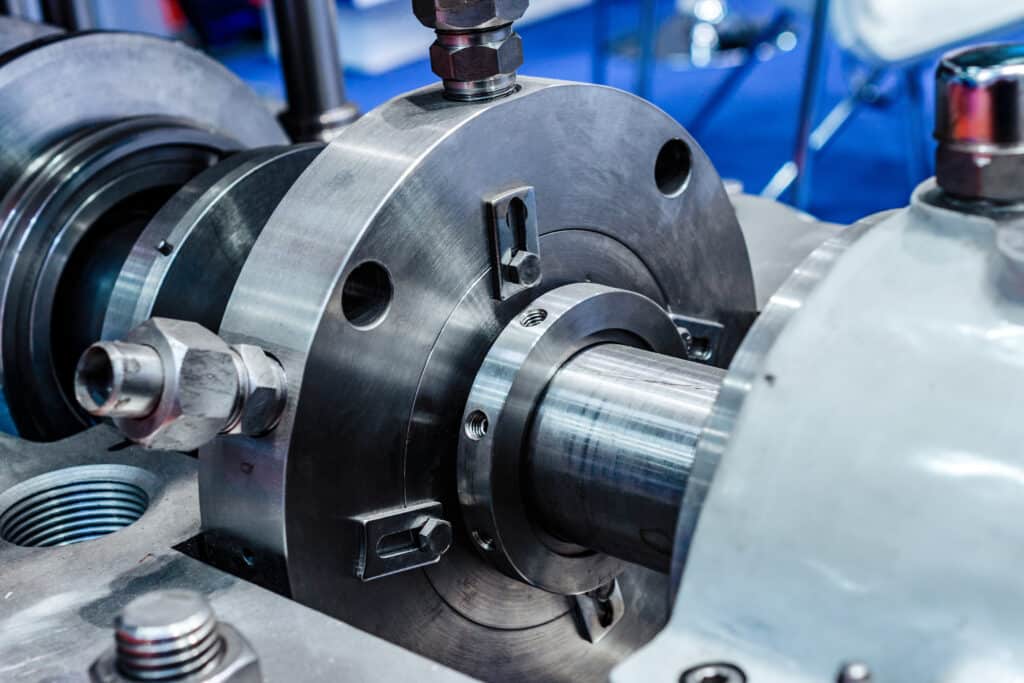
What Is a Mechanical Seal Flushing Plan
A mechanical seal flushing plan is a system designed to introduce a clean, compatible liquid into the seal chamber of a mechanical seal. The purpose of this system is to ensure optimal seal performance and longevity by maintaining a clean and stable environment within the seal chamber.
Mechanical seal flushing plans are commonly used in pumping applications where the process fluid is not suitable for direct contact with the seal faces due to factors such as abrasive particles, high temperatures, or incompatibility with seal materials.
How Does Mechanical Seal Flushing Plan Work
In a typical mechanical seal flushing plan, a clean flush fluid is introduced into the seal chamber through a series of pipes, valves, and fittings. The flush fluid is typically supplied from an external source, such as a clean liquid reservoir or a plant water supply. The flush fluid enters the seal chamber through a flush inlet port and exits through a flush outlet port, creating a continuous flow of clean fluid across the seal faces.
The flow rate and pressure of the flush fluid are carefully regulated to maintain optimal conditions within the seal chamber. A flow control orifice or throttle valve is often used to adjust the flow rate, while a pressure control valve maintains the desired pressure within the seal chamber. In some cases, a heat exchanger may be incorporated into the flushing system to regulate the temperature of the flush fluid.
What Is the Purpose of a Mechanical Seal
The primary purpose of a flush plan is to control the environment around the seals by regulating factors such as temperature, pressure, and contaminants.
A well-designed seal flushing plan helps to:
- Remove heat generated by friction between the seal faces
- Lubricate the seal faces and minimize wear
- Prevent the accumulation of solids or precipitates in the seal chamber
- Maintain a stable fluid environment for the seal materials
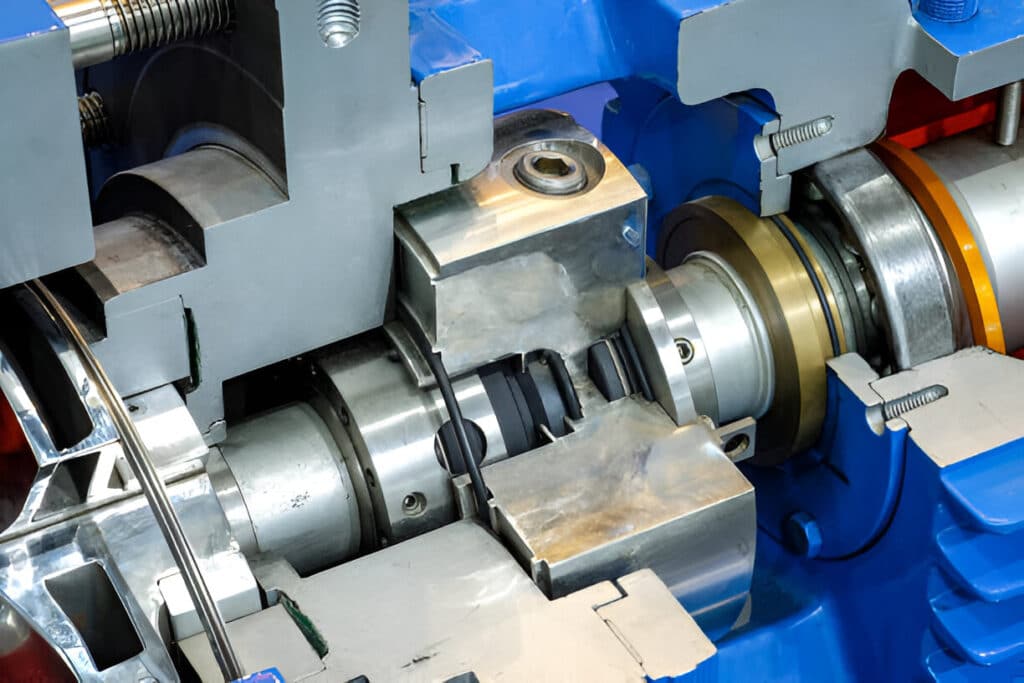
Factors Leading to Frequent Seal Flushing
High Concentration of Particulates or Abrasive Materials
One of the primary factors that can lead to frequent seal flushing is the presence of a high concentration of particulates or abrasive materials in the process fluid. These contaminants can enter the seal chamber and cause rapid wear of the seal faces, leading to increased leakage and premature seal failure.
Common sources of particulates and abrasive materials include:
- Suspended solids in the process fluid
- Corrosion products from piping and equipment
- Crystallization of dissolved solids due to changes in temperature or pressure
- Cavitation-induced erosion of pump components
Incorrect Flush Fluid Pressure, Flow Rate, Or Temperature
Insufficient flush fluid pressure can allow process fluid to enter the seal chamber, leading to contamination and damage to the seal faces. On the other hand, excessive flush fluid pressure can cause excessive leakage or even damage to the seal components. The ideal flush fluid pressure should be maintained at a level slightly higher than the seal chamber pressure to prevent process fluid ingress while minimizing flush fluid consumption.
Inadequate flush fluid flow rate can result in poor heat dissipation and an accumulation of contaminants within the seal chamber. This can lead to increased wear of the seal faces and premature failure. Conversely, excessive flush fluid flow rates can cause turbulence and erosion of the seal components.
Improper flush fluid temperature can also have a detrimental effect on seal performance. If the flush fluid temperature is too low, it may cause condensation of process vapors within the seal chamber, leading to contamination and corrosion. If the flush fluid temperature is too high, it may cause thermal distortion of the seal components or accelerated degradation of the seal materials. The ideal flush fluid temperature should be maintained within the acceptable range specified by the seal manufacturer, typically between 50-150°F (10-65°C).
Shaft Misalignment or Excessive Vibration
Shaft misalignment and excessive vibration are mechanical issues that can cause frequent seal flushing by inducing stress and wear on the seal components. When the rotating equipment is not properly aligned or balanced, it can create uneven loading and contact between the seal faces, leading to accelerated wear and leakage.
Faqs
What Is the Difference Between Mechanical Seal Quench and Flush
A mechanical seal quench and a mechanical seal flush are both methods of introducing a clean fluid into the seal chamber, but they serve different purposes and have distinct configurations.
Mechanical seal quench is designed to create a vapor barrier between the atmosphere and the process fluid. In a quench system, a clean fluid (typically a gas such as nitrogen or steam) is introduced into the seal chamber on the atmospheric side of the seal faces. This creates a positive pressure within the seal chamber, preventing the ingress of atmospheric contaminants and minimizing the escape of process fluid vapors.
Mechanical seal flush is designed to provide a continuous flow of clean, compatible liquid across the seal faces. The flush fluid is introduced into the seal chamber on the process side of the seal faces and exits on the atmospheric side, creating a constant purge of the seal chamber. The primary purpose of a flush system is to maintain a clean and stable environment within the seal chamber, preventing the accumulation of contaminants and heat that can lead to seal failure.
What Is the Pressure for Mechanical Seal Flushing
In general, the flush pressure should be maintained at a level slightly higher than the seal chamber pressure. A typical flush pressure is 10-15 psi (0.7-1.0 bar) above the seal chamber pressure.
How Much Water Is Required for a Mechanical Seal Flush
A typical range for mechanical seal flush flow rates is 0.5-2.0 gpm (1.9-7.6 lpm) per inch of seal shaft diameter. For example, a 2-inch (50 mm) shaft diameter seal would require a flush flow rate of 1-4 gpm (3.8-15.1 lpm).