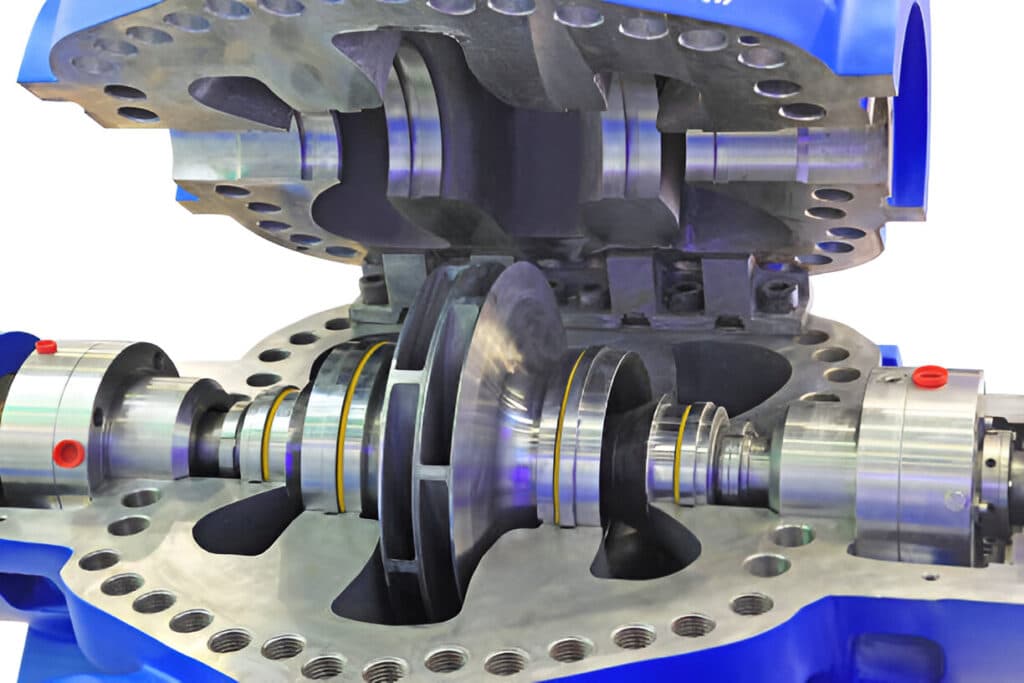
What Is Magnetic Drive Pump
A magnetic drive pump is a type of seal-less pump that utilizes permanent magnets to create a direct connection between the motor shaft and the pump shaft. This innovative design eliminates the need for mechanical seals, making mag-drive pumps ideal for handling hazardous, corrosive, or ultra-pure liquids.
The pump consists of an outer drive magnet assembly connected to the electric motor and an inner driven magnet assembly attached to the impeller. The magnetic connection allows for the transfer of torque without direct contact between the motor and pump, providing a hermetic seal and preventing fluid leakage.
Advantages of Magnetic Drive Pump
- Leak-proof design: The seal-less nature of magnetic drive pumps eliminates the risk of leakage, making them suitable for handling hazardous, toxic, or expensive fluids.
- Improved safety: By eliminating mechanical seals, mag-drive pumps minimize the potential for seal failures and the associated safety hazards.
- Reduced maintenance: The absence of mechanical seals and seal-related components reduces maintenance requirements and costs.
- Enhanced reliability: Magnetic drive pumps offer increased reliability due to their simple design and the elimination of seal-related failures.
- Wide range of applications: These pumps can handle a variety of liquids, including corrosive, abrasive, and ultra-pure fluids, making them suitable for diverse industrial applications.
Disadvantages of Magnetic Drive Pump
- Limited operating conditions: Magnetic drive pumps may have limitations in terms of temperature, pressure, and flow rate compared to mechanical seal pumps.
- Higher initial cost: The advanced technology and materials used in mag-drive pumps often result in a higher initial investment compared to traditional pumps.
- Reduced efficiency: The presence of the magnetic coupling can lead to slightly lower efficiency due to the additional energy required to overcome the magnetic forces.
- Limited torque capacity: Magnetic drive pumps have a maximum torque limit, which can restrict their use in high-pressure or high-viscosity applications.
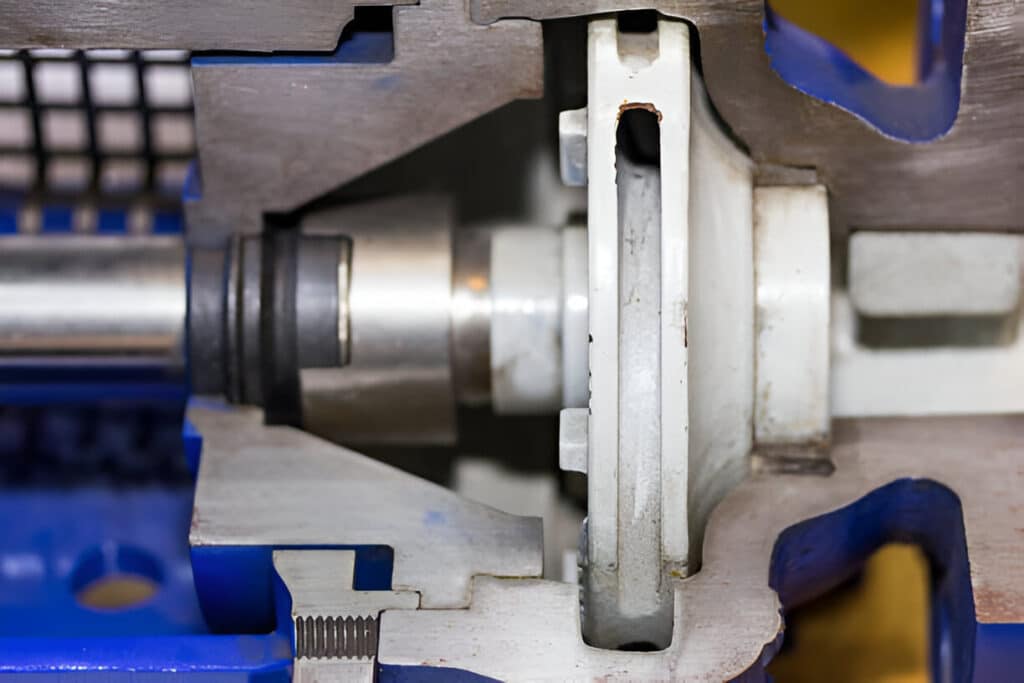
What Is Mechanical Seal Pump
A mechanical seal pump, also known as a centrifugal pump with mechanical seals, is a type of pump that uses mechanical seals to prevent fluid leakage along the pump shaft. The mechanical seal consists of two flat surfaces – a stationary component and a rotating component – that are pressed together by spring pressure and fluid pressure, creating a seal between the pump casing and the atmosphere.
Mechanical seals are designed to withstand the pressure, temperature, and chemical properties of the pumped fluid, making them suitable for a wide range of industrial applications.
Advantages of Mechanical Seal Pump
- Versatility: Mechanical seal pumps can handle a wide range of liquids, temperatures, and pressures, making them suitable for diverse applications.
- High efficiency: These pumps generally offer higher efficiency compared to magnetic drive pumps due to the direct connection between the motor shaft and pump impeller.
- Lower initial cost: Mechanical seal pumps typically have a lower upfront cost compared to magnetic drive pumps.
- Easier maintenance: Mechanical seals can be replaced without disassembling the entire pump, making maintenance less time-consuming and costly.
Disadvantages of Mechanical Seal Pump
- Potential for leakage: Mechanical seals can wear out over time, leading to fluid leakage and the need for periodic seal replacement.
- Higher maintenance costs: The presence of mechanical seals and the need for regular seal replacements can result in higher long-term maintenance costs compared to seal-less pumps.
- Safety concerns: The potential for seal failures and leakage can pose safety risks when handling hazardous or toxic fluids.
- Sensitivity to operating conditions: Mechanical seals are sensitive to changes in temperature, pressure, and fluid composition, which can impact their performance and lifespan.
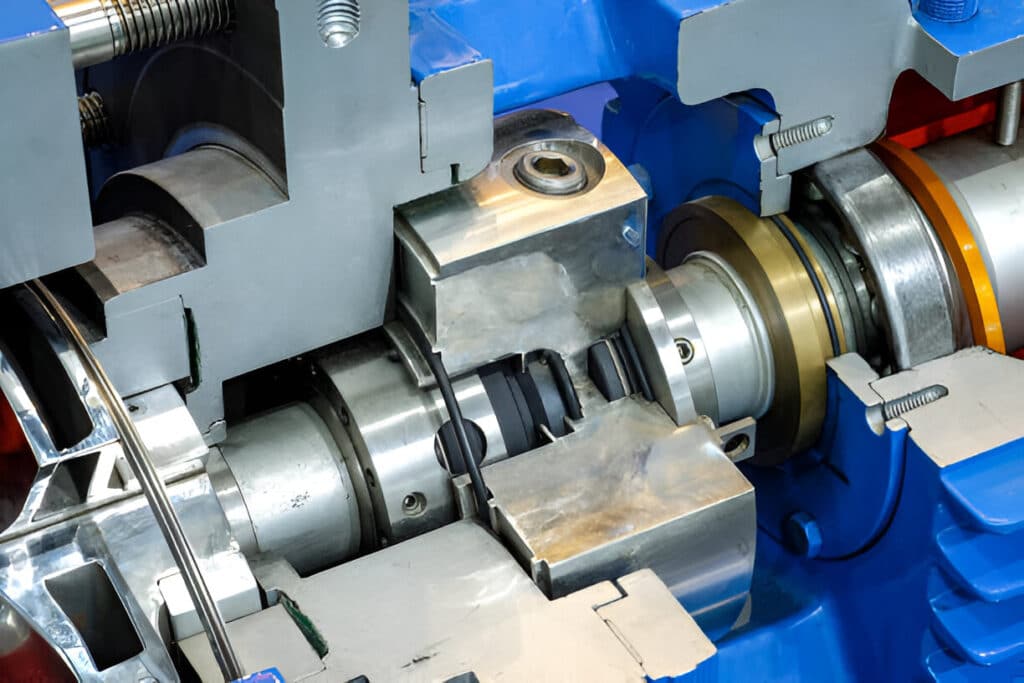
Difference Between Mechanical Seal and Magnetic Drive Pump
Leakage to the Atmosphere
Mechanical seal pumps: Mechanical seals, while designed to prevent fluid leakage, can wear out over time and allow small amounts of fluid to escape.
Magnetic drive pumps: Magnetic drive pumps offer a hermetic seal between the pump casing and the atmosphere, virtually eliminating the risk of leakage.
Installation & Maintenance
Mechanical seal pumps: Mechanical seal pumps generally require more frequent maintenance due to the need to replace worn seals and monitor seal performance.
Magnetic drive pumps: Magnetic drive pumps have fewer moving parts and do not require seal maintenance, resulting in reduced maintenance requirements and associated costs.
Monitoring
Mechanical seal pumps: Monitoring the performance and condition of mechanical seals is crucial to prevent leakage and ensure reliable operation. This may involve regular visual inspections, monitoring of seal flush systems, and the use of leak detection devices.
Magnetic drive pumps: Magnetic drive pumps require less monitoring due to the absence of mechanical seals and the reduced risk of leakage.
Monitoring
Mechanical seal pumps: Monitoring the performance and condition of mechanical seals is crucial to prevent leakage and ensure reliable operation. This may involve regular visual inspections, monitoring of seal flush systems, and the use of leak detection devices.
Magnetic drive pumps: Magnetic drive pumps require less monitoring due to the absence of mechanical seals and the reduced risk of leakage.
Cost-Effectiveness
Mechanical seal pumps: Mechanical seal pumps typically have a lower upfront cost but may incur higher maintenance expenses over time.
Magnetic drive pumps: Magnetic drive pumps often have a higher initial cost but can provide long-term savings through reduced maintenance and improved reliability.
Bearing Load
Mechanical seal pumps: In mechanical seal pumps, the bearings are subjected to both radial and axial loads due to the direct connection between the motor shaft and pump impeller. This can lead to increased wear on the bearings and may require more frequent bearing replacements.
Magnetic drive pumps: Magnetic drive pumps experience lower bearing loads as the magnetic coupling absorbs some of the axial forces, potentially extending bearing life.
Resonance Frequency
Magnetic drive pumps: The presence of the magnetic coupling in magnetic drive pumps can introduce additional resonance frequencies that must be considered during pump design and operation. If the pump operating speed coincides with the resonance frequency of the magnetic coupling, it can lead to excessive vibration and potentially damage the pump.
Mechanical seal pumps: Mechanical seal pumps do not face this issue as they lack the magnetic coupling component.
Safety
Magnetic drive pumps: Magnetic drive pumps offer inherently safer operation due to their leak-proof design, minimizing the risk of fluid leakage and associated safety hazards.
Mechanical seal pumps: Mechanical seal pumps, while designed to prevent leakage, have a higher potential for seal failures and subsequent safety concerns.
FAQs
Do Mag Drive Pumps Have Mechanical Seals?
No, magnetic drive pumps do not have mechanical seals. The term “seal-less” refers to the absence of dynamic seals, such as mechanical seals, in the pump design. Instead, mag-drive pumps use a magnetic coupling to transmit torque from the motor to the impeller, creating a hermetic seal between the pump casing and the atmosphere.
How Does a Magnetic Drive Sealless Pump Compare with a Canned Pump?
Canned motor pumps and magnetic drive pumps are both types of seal-less pumps designed to eliminate leakage and improve safety.
Canned motor pumps: In canned motor pumps, the motor and pump are integrated into a single unit, with the motor windings and rotor sealed inside a pressure-proof motor casing. This design provides a compact and leak-proof solution but may have limitations in terms of motor cooling and power output.
Magnetic drive pumps: Magnetic drive pumps use a magnetic coupling to transmit torque between the motor and pump, allowing for a separate motor and pump assembly. This design offers greater flexibility in terms of motor selection and maintenance, as the motor is not an integral part of the pump.