Bellows, an essential component in various industrial applications, come in a wide array of types and designs. Each type exhibits unique characteristics that make it suitable for specific tasks, from providing flexible connections in vacuum environments to protecting critical components from debris.
In this blog post, we will explore the different types categorized by their construction methods and shapes, and the applications they are best suited for.
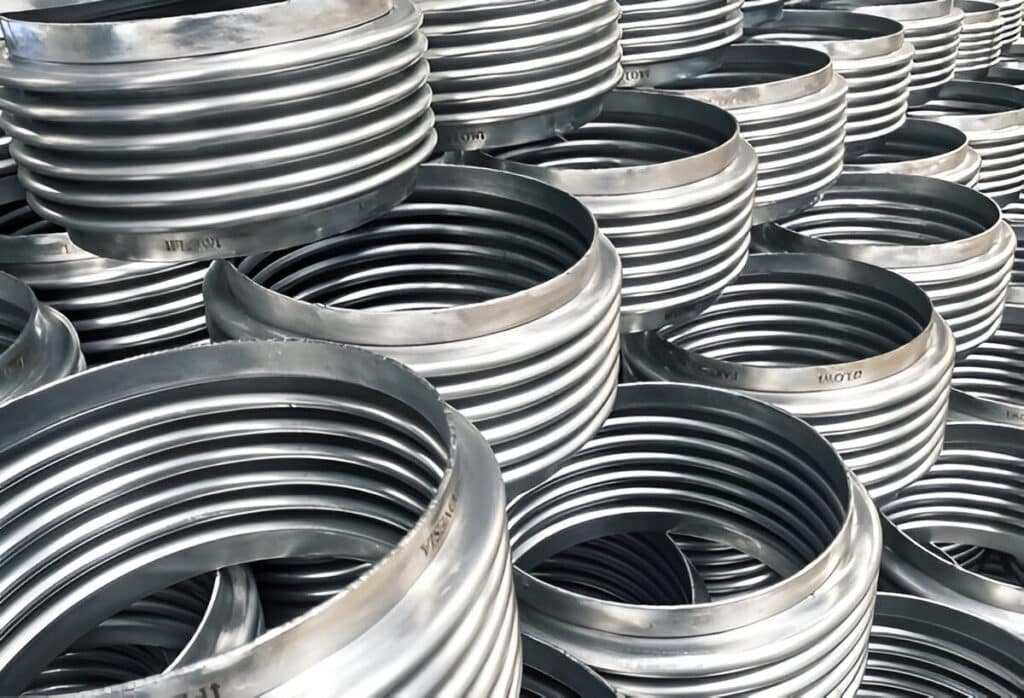
Types of Bellows by Construction Method
Formed Bellows
Also referred to as convoluted bellows, formed bellows are manufactured by reshaping a tube through processes such as hydroforming, cold forming, or rolling. The tube material is plastically deformed into the desired bellows shape, creating a series of convolutions. This construction method results in bellows with excellent pressure stability and load-bearing capabilities, making them a preferred choice for applications in petrochemical refineries, boiler plants, and thermal plants, where high-pressure environments are common.
Welded Bellows
Welded bellows are constructed by joining individually shaped diaphragms, usually made from thin metal sheets, through welding. Each diaphragm is precision-formed to the required shape and then welded at the inner and outer diameter to create the bellows convolutions. Compared to formed bellows, welded bellows provide several advantages, including greater flexibility, a wider range of motion, and more precise control over the spring rate.
Machined Bellows
In contrast to formed and welded bellows, machined bellows are created by machining a solid piece of material, typically forged rings or bar stock, to form the convolutions. This construction method produces bellows with exceptional strength and durability, capable of withstanding high spring rates and pressure thrusts. Machined bellows find applications in demanding environments, such as aerospace and high-pressure industrial systems.
Electroformed Bellows
The electroforming process deposits metal, usually nickel, uniformly onto a precision mandrel that is later chemically dissolved to leave behind an extremely thin-walled bellows with highly repeatable geometry. By producing wall thicknesses as low as a few micrometers, electroformed bellows have very low spring rates and high sensitivity.
Sewn Bellows
For the largest and most rigid bellows designs, sewn bellows offer performance properties unattainable with other construction methods. These are formed by stitching together flat sheets of coated fabric, such as neoprene or Kevlar-reinforced material, to form the flexible convolutions.
The fabric construction gives sewn bellows a very large stroke capability along with extremely high extendibility and compressibility. They can retract compactly into a short stack but extend as much as 10 to 20 times their retracted length, making them well-suited for applications like long-reach protective covers for machine slideways and articulating joints.
Folded Bellows
Folded bellows are manufactured by folding multiple layers of thermoplastic or elastomer materials together to create the convolutions. This construction method results in bellows that can withstand high-speed and high-cycle operations, making them suitable for dynamic applications. Folded bellows offer excellent flexibility and can be designed to accommodate specific motion requirements, such as linear, angular, or rotational movement.
Types of Bellows by Shape
Round Bellows
Round bellows are the most prevalent type, featuring a circular cross-section. This shape provides a high degree of flexibility and uniform stress distribution, making round bellows suitable for a broad range of applications. They are commonly used as seals to prevent leakage, as actuators to convert pressure into linear or rotary motion, and as expansion joints to absorb thermal expansion and contraction in piping systems.
Rectangular Bellows
Rectangular bellows feature a rectangular cross-section. They are commonly employed as protective covers for linear guides and machine tools, shielding critical components from debris, dust, and other contaminants. The flat surfaces of rectangular bellows allow for easy attachment and integration with adjacent equipment. Additionally, their shape enables them to accommodate linear motion while maintaining a compact profile.
Polygonal Bellows
Polygonal bellows are characterized by their multi-sided cross-section, which can take on various shapes such as square, hexagonal, or octagonal. This unique geometry makes them well-suited for applications that require specific spatial constraints or customized fit. Camera bellows and laser beam guide bellows are prime examples where polygonal bellows excel.
Elevating Platform Bellows
Elevating platform bellows are specifically engineered to protect the spindles and critical components in elevating platforms from environmental hazards. These bellows form a protective barrier, preventing dust, water, and debris from entering and damaging the delicate spindle mechanism.
Solar Energy Bellows
Similar to elevating platform bellows, solar energy bellows are designed to shield spindles in solar panels from environmental factors such as dust, water, and wind-borne particles.
U-Shaped Bellows
U-shaped bellows have a distinctive cross-section resembling the letter “U”. This shape provides excellent flexibility and allows for significant lateral movement, making U-shaped bellows ideal for use as way covers on machine tools and other industrial equipment.
Rolling Lobe Bellows
Rolling lobe bellows are distinguished by their unique rolling lobe design, which allows for significant extension and compression while minimizing stress on the bellows material. This characteristic makes them particularly well-suited for applications involving large displacements or high-frequency cycling. Rolling lobe bellows are frequently found in vehicle suspensions, particularly in heavy-duty trucks and buses.
Diaphragm Bellows
Diaphragm bellows share many similarities with welded bellows in terms of their construction, consisting of thin, flexible metal diaphragms welded together to form a series of convolutions. However, diaphragm bellows are typically smaller in size and designed for more delicate applications, such as pressure gauges, sensors, and vacuum interrupters.
KF Bellows
KF bellows, also known as Klein Flange bellows, are specifically designed for use in vacuum systems. They provide a flexible and reliable connection between components while maintaining a high vacuum seal. KF bellows are commonly used in scientific research, semiconductor manufacturing, and other applications.
Vacuum Bellows
Vacuum bellows are another specialized type designed for use in vacuum environments. Unlike KF bellows, which are primarily used for connecting components, vacuum bellows are used to provide motion or flexibility within a vacuum system. These bellows are manufactured from high-quality materials with low outgassing properties to minimize contamination of the vacuum.
Crimped Convoluted Bellows
Crimped convoluted bellows are characterized by their attachment method to a bead plate using a permanent crimp. This construction provides a secure and stable connection, allowing the bellows to maintain its position and shape even under high stress or vibration. The convoluted design of these bellows enables them to provide effective vibration isolation and accommodate linear or angular motion.
Sleeve Bellows
Sleeve bellows, also known as air springs or air bellows, consist of a cylindrical rubber sleeve that expands and compresses in response to air pressure changes. These bellows are commonly used in commercial vehicles and industrial applications to provide a smooth, comfortable ride and support heavy loads.