Bushing seals are critical components in various machinery applications, providing effective sealing solutions between moving parts. These seals are designed to prevent leakage, minimize friction, and protect against contaminants, ensuring optimal performance and longevity of the equipment.
By selecting the appropriate bushing seal material and design, engineers can address specific operational requirements such as temperature range, pressure, speed, and chemical compatibility. In this blog post, we will dive into the world of bushing seals, exploring their types, advantages and disadvantages.
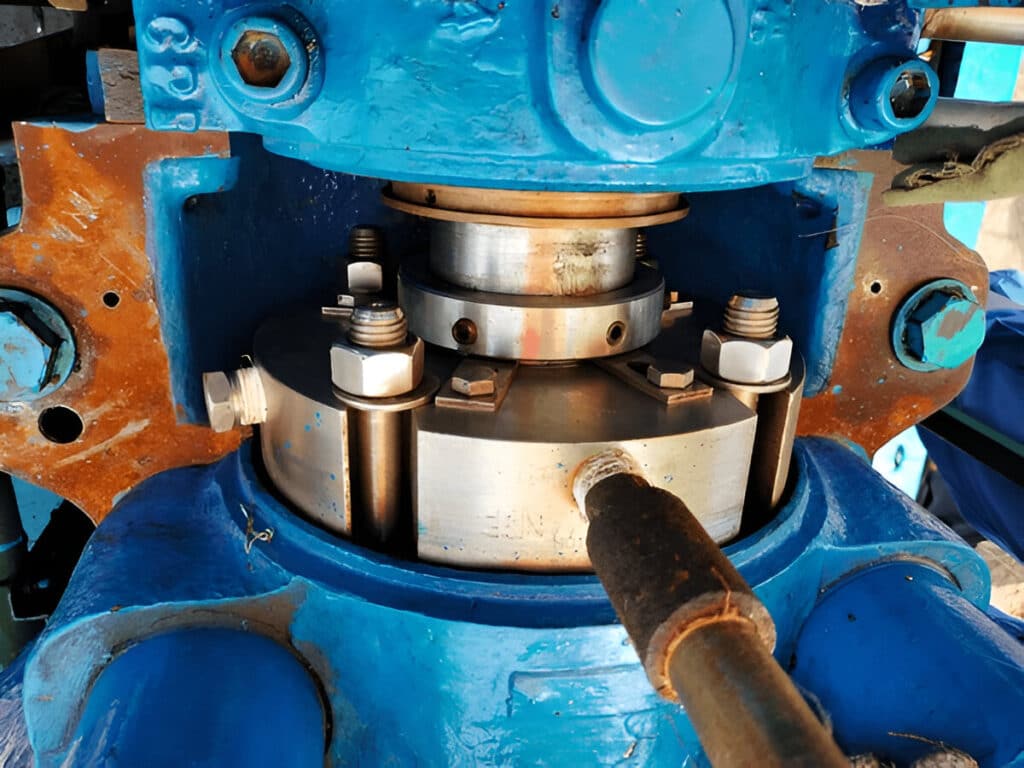
What Are Bushing Seals
Bushing seals are mechanical components designed to prevent leakage and control fluid flow in rotary applications. These seals are typically installed between a stationary component, such as a housing, and a rotating shaft or rod. The primary function of bushing seals is to maintain a tight seal around the shaft while accommodating its rotational movement.
The sealing action of bushing seals is achieved through a combination of factors. First, the seal material is selected to provide a tight fit around the shaft, minimizing clearance and reducing leakage paths. Second, the seal geometry is designed to promote effective sealing, often incorporating features such as lips, grooves, or multi-piece constructions.
In addition to preventing leakage, bushing seals also help to protect the internal components of machinery from contamination by external debris, dust, or moisture. By maintaining a clean and controlled environment within the equipment, bushing seals contribute to improved system reliability and extended component life.
Types Of Bushing Seals
Bushing seals come in various types, each designed to suit specific applications and operating conditions. The main types of bushing seals include fixed bushing seals, floating bushing seals, floating ring bushing seals, balanced bushing seals, and segment bushing seals.
Fixed bushing seals
Fixed bushing seals are rigidly mounted to the housing and remain stationary during operation. They feature a precise clearance between the shaft and the bushing, which allows for proper lubrication and minimizes leakage. Fixed bushing seals are suitable for applications with low to moderate speeds and pressures, such as in gearboxes and pumps.
Floating bushing seals
Floating bushing seals are designed to move radially with the shaft, accommodating misalignment and thermal expansion. They consist of a bushing with a larger clearance than fixed bushing seals, allowing for greater tolerance to shaft movement. Floating bushing seals are commonly used in applications with moderate speeds and pressures, such as in compressors and turbines.
Floating ring bushing seals
Floating ring bushing seals feature a rotating ring that floats between the stationary bushing and the shaft. The ring is typically made of a soft material, such as bronze or carbon, which conforms to the shaft surface and provides a tight seal. Floating ring bushing seals are effective in high-speed applications and can handle moderate to high pressures, making them suitable for use in steam turbines and gas compressors.
Balanced bushing seals
Balanced bushing seals are designed to equalize the pressure on both sides of the seal, reducing the net axial force acting on the bushing. This is achieved by incorporating balance holes or grooves in the bushing, which allow the pressure to equalize across the seal faces. Balanced bushing seals are ideal for high-pressure applications, such as in centrifugal compressors and pumps, where unbalanced seals may cause excessive wear and leakage.
Segment bushing seals
Segment bushing seals consist of multiple segments or pads arranged around the shaft, creating a seal between the stationary and rotating components. The segments are typically made of a wear-resistant material, such as carbon or tungsten carbide, and are held in place by a garter spring or other retaining mechanism. Segment bushing seals offer excellent sealing performance and can handle high speeds and pressures, making them suitable for demanding applications, such as in gas turbines and high-pressure pumps.
Advantages of Bushing Seals
Low Friction and Wear
Bushing seals offer low friction and wear characteristics due to their design and materials. The smooth surface of the bushing seal minimizes friction between the shaft and the seal, reducing heat generation and wear. This low-friction operation improves the efficiency and longevity of the sealing system.
Compact Design
Bushing seals feature a compact design that allows for easy integration into various machinery and equipment. Their small size and simple construction enable installation in tight spaces without compromising sealing performance. This compact design also contributes to reduced weight and space requirements.
Cost-Effective Solution
Compared to other sealing options, bushing seals provide a cost-effective solution for many applications. The simplicity of their design and the use of standard materials make them an economical choice for sealing rotating shafts. Bushing seals offer reliable performance at a lower cost than more complex sealing systems.
Versatile Application
Bushing seals are versatile and can be used in a wide range of industries and applications. They are suitable for sealing lubricants, oils, and other fluids in various machinery, including pumps, gearboxes, and hydraulic systems. The adaptability of bushing seals allows for their use in diverse operating conditions and environments.
Disadvantages of Bushing Seals
Limited Pressure Capability
Bushing seals have limitations in terms of pressure capability compared to other sealing options. They are typically designed for low to moderate pressure applications and may not provide adequate sealing performance in high-pressure systems.
Sensitivity to Misalignment
Misalignment can lead to increased friction, wear, and leakage. Bushing seals are more sensitive to misalignment compared to other sealing types, requiring precise installation and maintenance to ensure proper functioning.
Limited Speed Range
Bushing seals are most effective in applications with low to moderate shaft speeds. High-speed operations can generate excessive heat and wear, compromising the sealing performance of bushing seals.
Applications of Bushing Seals
Pumps and Compressors
Bushing seals are commonly used in pumps and compressors to seal the rotating shafts and prevent fluid leakage. They provide reliable sealing performance in low to moderate pressure applications, ensuring the efficient operation of pumps and compressors in various industries, including water treatment, oil and gas, and chemical processing.
Gearboxes and Transmissions
Bushing seals find application in gearboxes and transmissions to seal the rotating shafts and prevent lubricant leakage. They help maintain the integrity of the lubrication system, reducing contamination and ensuring smooth operation. Bushing seals are suitable for low to moderate speed gearboxes and transmissions in automotive, industrial, and agricultural machinery.
Hydraulic and Pneumatic Systems
Bushing seals are employed in hydraulic and pneumatic systems to seal the rotating components and prevent fluid leakage. They provide reliable sealing performance in low to moderate pressure applications, maintaining the efficiency and functionality of hydraulic and pneumatic systems in various industries, including construction, manufacturing, and aerospace.