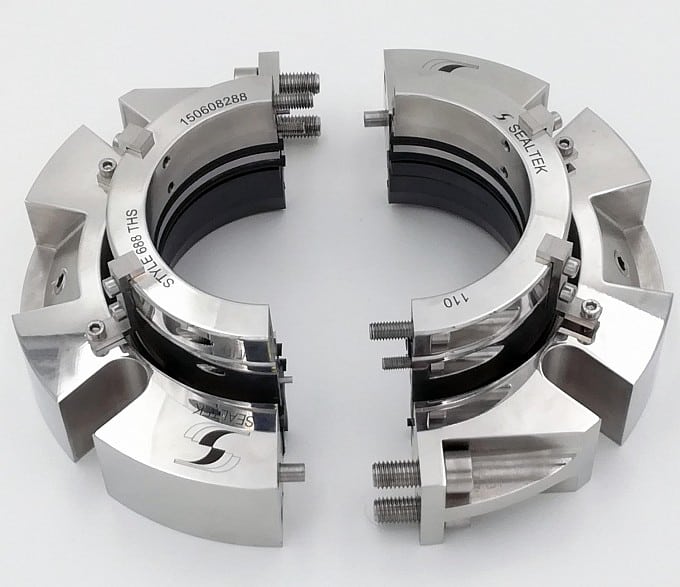
What Are Split Mechanical Seals
Split mechanical seals, also known as split seals, are a type of mechanical seal that consists of two halves which can be installed around a shaft without the need for complete disassembly of the equipment. This unique design allows for easier installation, maintenance, and repair compared to traditional one-piece mechanical seals.
Split mechanical seals are commonly used in pumps, mixers, agitators, and other rotating equipment where shaft sealing is critical to prevent leakage and maintain efficiency. These seals are particularly useful in applications where frequent seal replacement is necessary, or where the equipment is difficult to disassemble due to its size or location.
How Split Mechanical Seals Work
A split mechanical seal operates on the same principles as a standard mechanical seal, with the primary difference being its split design. The seal consists of two main components: a stationary part (the seal ring) and a rotating part (the mating ring). The seal ring is typically mounted on the stationary housing, while the mating ring is attached to the rotating shaft.
The two halves of the split seal are carefully machined to ensure a precise fit when assembled around the shaft. A secondary sealing element, such as an O-ring or gasket, is used to seal the two halves together and prevent leakage between them.
When the equipment is in operation, the rotating mating ring and stationary seal ring create a tight seal that prevents fluid from escaping the system. The seal faces are usually made from hard, wear-resistant materials such as silicon carbide, tungsten carbide, or ceramic. These materials are lapped to a very fine finish to ensure optimal sealing performance and minimal leakage.
Split mechanical seals often incorporate additional features such as springs, bellows, or hydraulic balancing devices to maintain the proper sealing pressure between the seal faces. These components help to compensate for any shaft misalignment, thermal expansion, or pressure fluctuations that may occur during operation.
Advantages of Split Mechanical Seals
- Ease of installation: Split seals can be installed without completely disassembling the equipment, saving time and reducing downtime during seal replacement.
- Reduced maintenance costs: The ability to replace split seals without extensive disassembly can significantly reduce maintenance costs, especially in large or complex equipment.
- Improved safety: Split seals minimize the need for workers to enter confined spaces or work in hazardous environments during seal replacement, enhancing overall safety.
- Versatility: Split mechanical seals can be used in a wide range of applications and can be customized to suit specific operating conditions, such as high temperatures, pressures, or corrosive environments.
- Increased reliability: The precise manufacturing and assembly of split seals ensure optimal sealing performance, reducing the risk of leakage and improving overall system reliability.
Disadvantages of Split Mechanical Seals
- Higher initial cost: Split seals are typically more expensive than traditional one-piece seals due to their complex design and precise manufacturing requirements.
- Potential for misalignment: If not installed correctly, the two halves of a split seal may not align properly, leading to increased leakage or premature wear.
- Limited pressure and speed capabilities: Split seals may not be suitable for extremely high-pressure or high-speed applications, as the split design can limit their performance under these conditions.
- Increased complexity: The additional components and precise fitting required for split seals can make them more complex than one-piece seals, requiring specialized knowledge for installation and maintenance.
What Are Split Mechanical Seals Used for
- Pumps: Split seals are frequently used in centrifugal pumps, positive displacement pumps, and submersible pumps to prevent leakage of the pumped fluid.
- Mixers and agitators: In mixing and agitation equipment, split seals help to maintain the integrity of the process fluid and prevent contamination.
- Refineries and petrochemical plants: Split seals are used in various rotating equipment in refineries and petrochemical facilities to handle hazardous or corrosive fluids.
- Power generation: In power plants, split seals are used in pumps, turbines, and other rotating equipment to ensure reliable operation and minimize downtime.
- Food and pharmaceutical processing: Split seals are used in equipment handling food or pharmaceutical products to maintain strict hygiene standards and prevent contamination.
- Marine and offshore: In marine and offshore applications, split seals are used in propulsion systems, thrusters, and other rotating equipment exposed to seawater.
- Paper and pulp industry: Split seals are used in pumps and other equipment handling abrasive slurries and corrosive chemicals in the paper and pulp manufacturing process.
In conclusion
Split mechanical seals are a valuable sealing solution for various industrial applications, offering enhanced ease of installation, reduced maintenance costs, and improved reliability compared to traditional one-piece seals.
By understanding their working principles, advantages, and disadvantages, engineers and maintenance professionals can make informed decisions when selecting and implementing split seals in their equipment.