A pusher mechanical seal is a specialized sealing device designed to prevent fluid leakage in rotating equipment, such as pumps and compressors. This type of seal utilizes a spring-loaded mechanism to maintain constant contact between the sealing faces, ensuring optimal performance and reliability in demanding industrial applications.
This blog post will delve into the intricacies of pusher mechanical seals, exploring their components, functioning principles, and key advantages.
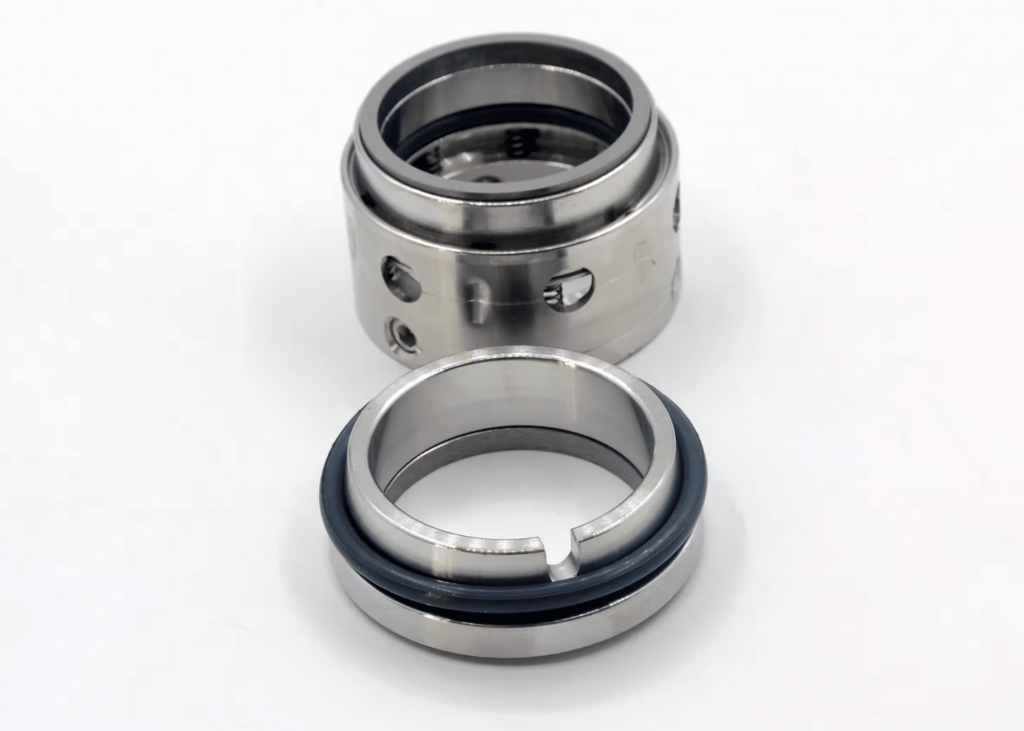
What is a Pusher Mechanical Seal
A pusher mechanical seal is a type of mechanical seal designed to prevent leakage of fluids or gases between a rotating shaft and a stationary housing. It consists of a rotating seal face, usually made of a hard material such as silicon carbide or tungsten carbide, and a stationary seal face, typically made of a softer material like carbon or ceramic.
The rotating seal face is mounted on the shaft, while the stationary seal face is fixed to the housing. A spring mechanism applies pressure to the seal faces, pushing them together to create a tight seal. This spring force ensures that the seal faces maintain contact even under varying pressure and temperature conditions.
Pusher mechanical seals are named for the way the spring mechanism “pushes” the seal faces together. The spring is located behind the stationary seal face, and it compensates for any wear or misalignment that may occur during operation. As the seal faces wear down, the spring continues to push them together, maintaining a consistent seal.
How Pusher Mechanical Seals Work
The working principle of a pusher mechanical seal relies on the precise interaction between its components. The stator is typically mounted in the seal housing, while the rotor is attached to the rotating shaft. The seal faces are held in close contact by a combination of hydraulic pressure and spring force.
As the shaft rotates, the rotor face moves with it, maintaining a thin fluid film between the seal faces. This fluid film, often just a few microns thick, prevents direct contact between the faces and minimizes wear. The sealing pressure is maintained by the spring force pushing the rotor face against the stator face, as well as the hydraulic pressure acting on the backside of the rotor.
To accommodate shaft axial movement and misalignment, pusher mechanical seals incorporate secondary sealing elements, such as O-rings or V-rings. These elements are located between the rotor and the sleeve, allowing for some degree of movement while maintaining the seal’s integrity.
Advantages of Pusher Mechanical Seals
Compact and Cost-Effective
One major benefit is their simple, compact design compared to other mechanical seal types. The basic components of a pusher seal – a seal ring, mating ring, and secondary seals – make for a space-efficient assembly that is easy to retrofit into many types of rotating equipment without major modifications.
This simple, compact design also makes pusher seals very cost-effective. They are economical to manufacture and are often the least expensive type of mechanical seal.
Versatile and Reliable
Pusher mechanical seals are also highly versatile and reliable across a wide range of common applications. While not suited for extreme pressures, they provide dependable sealing performance and long service life in most services up to about 200 psi. The dynamic O-rings accommodate shaft movement and maintain sealing contact for reliable functionality.
Disadvantages of Pusher Mechanical Seals
Limited Pressure Capability
One disadvantage of pusher mechanical seals is their limited ability to handle high pressures compared to other types of seals like bellows and diaphragm seals. The dynamic O-ring that provides axial loading in a pusher seal tends to extrude and fail under very high pressures, typically above 200 psi. This pressure limitation makes pusher seals unsuitable for some demanding high-pressure applications.
Vulnerable to Dry Running
Pusher mechanical seals are also more vulnerable to damage from dry running than non-pusher designs. If the seal faces run dry without proper lubrication from the sealed fluid, the high friction and heat can quickly destroy the carbon and ceramic seal faces. The dynamic secondary seals are also prone to burning up during dry running conditions.
Higher Leakage Rates
Another potential drawback of pusher mechanical seals is that they tend to have slightly higher leakage rates than non-pusher seals, especially as they wear over time. The axial loading mechanism of a pusher seal maintains less precise face contact than spring or bellows loading.
Applications of Pusher Mechanical Seals
Petrochemical Processing
Pusher mechanical seals are widely used in petrochemical processing equipment like pumps, mixers and compressors. They are well-suited for sealing organic chemicals, hydrocarbons, and other fluids common in refineries and chemical plants.
Pulp and Paper
The pulp and paper industry also makes extensive use of pusher mechanical seals. They are found in pulp digesters, paper machine rolls, agitators, fan pumps and more. Pusher seals made with appropriate elastomers reliably handle the challenging fluid compatibility requirements of paper industry chemicals and process fluids.
Water and Wastewater
Pusher seals are a common choice for water and wastewater treatment equipment as well. The moderate pressures and benign fluid properties in most water applications are well-suited for pusher seals. Their compact, economical design makes them a practical choice for the many pumps, mixers and other rotating equipment used in the treatment of municipal and industrial water and wastewater.