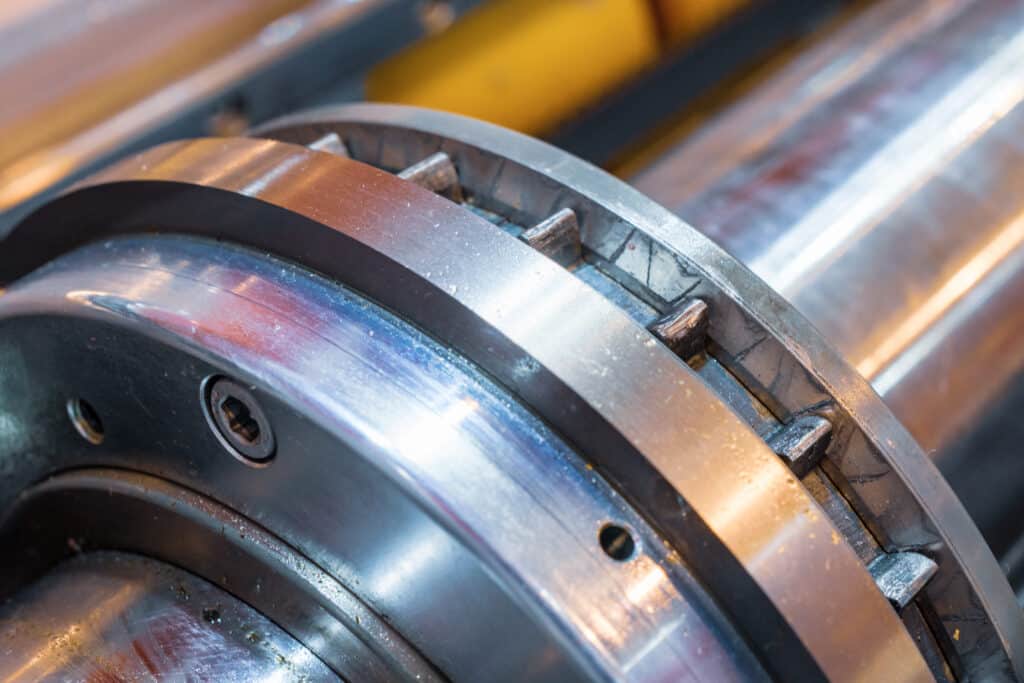
Typical Acceptable Leakage Rates
In most industrial applications, a properly functioning mechanical seal will have a leakage rate of 10 drops per hour or less per seal. This small amount of leakage is considered normal and necessary for proper seal lubrication and cooling. Excessive leakage beyond this rate can indicate issues with the seal design, installation, or operating conditions.
Seal leakage is measured by collecting and quantifying the fluid that leaks past the seal faces over a given period. The generally accepted method is to measure drops per minute and convert to an hourly rate. One drop per minute equates to approximately 2.5 to 3 ml per hour.
Allowable Leakage of API 682
The American Petroleum Institute (API) Standard 682 provides guidelines for acceptable seal leakage in the oil and gas industry. API 682 defines three seal leakage classes:
- Category I Seals: Leakage rate less than 500 ml per day (20.8 ml/hr)
- Category II Seals: Leakage rate less than 1,000 ml per day (41.7 ml/hr)
- Category III Seals: Leakage rate less than 2,000 ml per day (83.3 ml/hr)
These allowable leakage rates are higher than the typical 10 drops per hour benchmark due to the demanding operating conditions and critical nature of oil and gas applications.
Factors Affecting Seal Leakage Rate
Seal Design Factors
- Face Materials: The tribological properties and compatibility of the primary and mating ring face materials affect leakage. Hard face pairings like silicon carbide vs. silicon carbide tend to run with tighter clearances and less leakage.
- Balance Ratio: Seals with high balance ratios (i.e., more closing force) tend to have lower leakage rates. However, this must be balanced against heat generation and wear.
- Face Treatments: Surface treatments like laser surface texturing (LST) or microwave resurfacing can be used to optimize the topography of the seal faces for improved lubrication and leakage control.
- Spring Loading: The spring force holding the faces together affects the face loading and leakage rate. Stronger springs reduce leakage but increase wear and heat generation.
Equipment Factors
- Shaft Speed: Higher shaft speeds tend to increase seal leakage due to greater centrifugal forces and turbulence.
- Misalignment: Excessive shaft misalignment or deflection can cause uneven loading and increased leakage at the seal faces.
- Vibration: Vibration can cause the seal faces to chatter or open momentarily, leading to higher leakage rates.
Operating Conditions
- Pressure: Higher sealed pressures tend to increase leakage rate all else being equal. Doubled pressure will approximately double the leakage rate.
- Temperature: Increased temperatures reduce viscosity which can lead to higher leakage rates. High temperatures can also damage elastomers and cause face distortion.
Fluid Properties
- Viscosity: Lower viscosity fluids are more prone to leakage as they flow more easily through the thin film between the faces.
- Lubricity: Fluids with poor lubricating properties can cause increased friction and wear at the seal faces, leading to higher leakage.
- Abrasiveness: Abrasive fluids accelerate wear of the seal faces, causing faces to open up and increasing leakage over time.
- Volatility: Highly volatile or gaseous fluids are more difficult to seal and are prone to greater leakage, especially if operating near the fluid’s vapor pressure.