Cryogenic seals are specialized sealing solutions designed to operate in extremely low-temperature environments. These seals play a vital role in maintaining the integrity and performance of machinery and systems operating under cryogenic conditions.
This blog post will delve into the world of cryogenic seals, exploring their unique characteristics, design considerations, advantages, and applications. We will also discuss the challenges associated with cryogenic sealing and the strategies employed to overcome them.
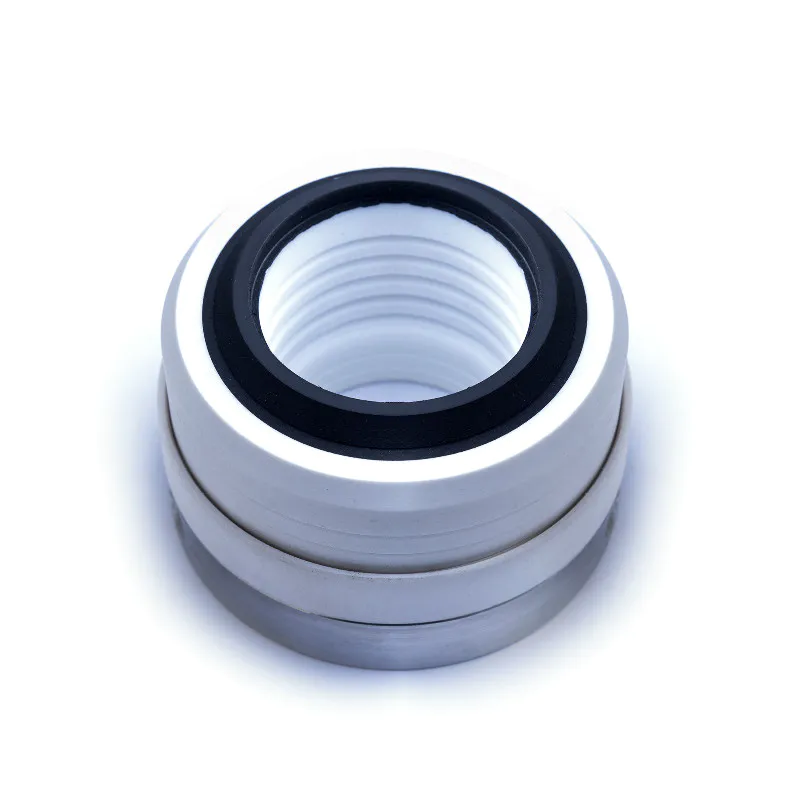
Cryogenic Conditions
Cryogenic conditions refer to extremely low temperature environments, typically below -150°C (-238°F). At these temperatures, materials exhibit unique properties and behaviors that differ significantly from their characteristics at room temperature.
In cryogenic systems, common fluids include liquefied gases such as liquid nitrogen (LN2), liquid helium (LHe), and liquid hydrogen (LH2). These liquids have boiling points of -196°C (-320.8°F), -269°C (-452.2°F), and -253°C (-423.4°F), respectively, at atmospheric pressure.
The extreme cold in cryogenic environments presents several challenges for materials and components. Thermal contraction, embrittlement, and changes in mechanical properties can lead to seal failure, leakage, and system malfunctions if not properly addressed.
What Is Cryogenic Seal
A cryogenic seal is a specialized sealing solution designed to maintain a leak-tight barrier in extremely low-temperature applications. These seals prevent the escape of cryogenic fluids, maintain vacuum insulation, and protect sensitive components from the adverse effects of cold temperatures.
The primary function of a cryogenic seal is to maintain a leak-tight seal between mating surfaces, preventing the ingress of external contaminants and the egress of cryogenic fluids. These seals must withstand the challenges associated with cryogenic temperatures, such as thermal contraction, material embrittlement, and extreme temperature gradients.
To ensure reliable performance, cryogenic seals are manufactured from special materials that retain their flexibility, strength, and sealing properties at low temperatures. Common materials include PTFE (polytetrafluoroethylene), PCTFE (polychlorotrifluoroethylene), and special metal alloys like stainless steel, aluminum, and Inconel.
Types of Cryogenic Seals
Static Seals
Static seals are used in cryogenic applications where there is no relative motion between the sealing surfaces. These seals are typically made from materials such as PTFE, PCTFE, or other low-temperature compatible elastomers. Static seals are designed to maintain a tight seal under the extreme cold and pressure conditions found in cryogenic systems.
Dynamic Seals
Dynamic seals are used in cryogenic applications where there is relative motion between the sealing surfaces, such as in rotating or reciprocating equipment. These seals must be able to withstand the challenges of cryogenic temperatures while also accommodating the movement of the components. Dynamic seals for cryogenic applications often incorporate specialized designs, such as bellows or spring-energized seals, to maintain sealing effectiveness under these demanding conditions.
Gaskets
Gaskets are another type of seal commonly used in cryogenic systems. These flat seals are placed between two stationary surfaces, such as flanges, to prevent leakage. Gaskets for cryogenic applications are typically made from materials that remain flexible and maintain their sealing properties at extremely low temperatures, such as PTFE, graphite, or certain metals like copper or stainless steel.
Design Considerations for Cryogenic Seals
Material
The selection of appropriate materials is critical for the successful performance of cryogenic seals. The materials must be able to withstand the extremely low temperatures without becoming brittle, losing flexibility, or experiencing significant dimensional changes. Some common materials used in cryogenic seals include:
- PTFE (Polytetrafluoroethylene)
- PCTFE (Polychlorotrifluoroethylene)
- FKM (Fluoroelastomer)
- FFKM (Perfluoroelastomer)
- Graphite
- Stainless steel
- Copper
Design to Accommodate Thermal Expansion and Contraction
Cryogenic seals must be designed to accommodate the significant thermal expansion and contraction that occurs when components are exposed to extremely low temperatures. As materials cool down, they tend to shrink, which can lead to changes in the sealing interface and potentially compromise the seal’s effectiveness.
To mitigate this issue, cryogenic seals often incorporate flexible elements, such as bellows or spring-energized components, that can maintain contact between the sealing surfaces despite dimensional changes. Additionally, designers may specify materials with similar coefficients of thermal expansion for mating components to minimize the relative movement between them.
Mechanical Stress Management
Cryogenic seals are subjected to significant mechanical stresses due to the extreme temperature gradients and pressure differentials found in cryogenic systems. These stresses can lead to seal failure if not properly managed.
Designers must carefully consider the seal geometry, material properties, and installation methods to ensure that the seal can withstand the imposed stresses. This may involve using materials with high strength and low thermal conductivity, incorporating stress-relieving features into the seal design, or specifying appropriate torque values for seal installation to prevent over-compression or damage.
Advantages of Cryogenic Seals
Excellent Sealing Performance
One of the key advantages of cryogenic seals is their superior sealing performance in extreme low-temperature environments. Cryogenic seals are specifically designed to maintain a tight, leak-free seal even when exposed to cryogenic fluids and gases.
Enhanced Safety
Cryogenic seals play a vital role in enhancing safety in cryogenic systems. By preventing leaks and maintaining the integrity of the sealed components, cryogenic seals help minimize the risk of hazardous situations arising from the escape of cryogenic fluids or gases.
Increased System Reliability
The use of cryogenic seals significantly improves the reliability of cryogenic systems. These seals are designed to withstand the extreme thermal stresses and mechanical loads encountered in cryogenic environments. By providing a reliable sealing solution, cryogenic seals help prevent system failures, downtime, and costly repairs.
Disadvantages of Cryogenic Seals
Limited Temperature Range
One of the main disadvantages of cryogenic seals is their limited temperature range. While cryogenic seals excel in extremely low-temperature environments, they may not be suitable for applications that involve a wide range of temperatures. The materials and design of cryogenic seals are optimized for cryogenic conditions, which can limit their effectiveness and durability in higher temperature ranges.
Higher Cost
Cryogenic seals often come with a higher cost compared to standard sealing solutions. The specialized materials, such as polymers and metals, used in the manufacturing of cryogenic seals contribute to their increased cost. Additionally, the precision engineering and rigorous testing required to ensure the reliability and performance of cryogenic seals further add to their overall expense.
Complexity in Installation and Maintenance
The installation and maintenance of cryogenic seals can be more complex compared to standard seals. The unique design features and tight tolerances of cryogenic seals require careful handling and precise installation procedures to ensure proper sealing performance. Maintenance activities, such as seal replacement or repair, may also be more intricate and time-consuming due to the specialized nature of cryogenic seals.
Applications of Cryogenic Seals
Liquefied Natural Gas (LNG) Systems
Cryogenic seals find extensive application in liquefied natural gas (LNG) systems. LNG is stored and transported at extremely low temperatures, typically around -162°C (-260°F). Cryogenic seals are utilized in various components of LNG systems, such as storage tanks, pipelines, and transfer lines, to prevent leakage and ensure the safe containment of the cryogenic liquid.
Cryogenic Fluid Transfer and Storage
Cryogenic seals are widely used in the transfer and storage of cryogenic fluids, such as liquid nitrogen, liquid oxygen, and liquid helium. These fluids are utilized in various industries, including healthcare, aerospace, and scientific research. Cryogenic seals are employed in the valves, couplings, and connections of cryogenic fluid transfer lines and storage vessels. They ensure leak-free operation and maintain the purity and integrity of the cryogenic fluids during transfer and storage processes.
Aerospace and Space Applications
Cryogenic seals play a crucial role in aerospace and space applications. In rocket engines, cryogenic propellants such as liquid hydrogen and liquid oxygen are used to generate thrust. Cryogenic seals are employed in the fuel and oxidizer lines, as well as in the engine components, to prevent leakage and ensure the efficient and safe operation of the propulsion system. Additionally, cryogenic seals are used in satellite systems and space vehicles to maintain the integrity of cryogenic cooling systems and instrumentation.