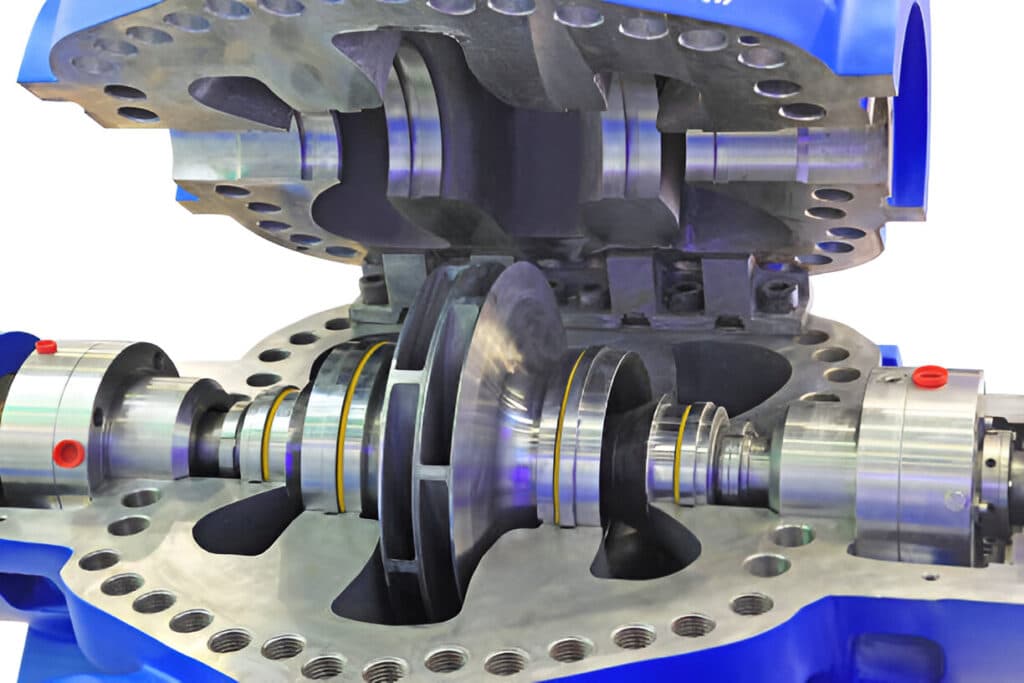
What is Tandem Seal
A tandem seal is a type of double mechanical seal arrangement used in various industrial applications to provide enhanced sealing performance and safety. This configuration consists of two sets of seal rings arranged in series along the shaft, with the inboard seal (primary seal) facing the process fluid and the outboard seal (secondary seal) facing the atmosphere.
Tandem seals are designed to offer a higher level of safety and reliability compared to single seals, especially when handling dangerous or flammable liquids. The space between the two seals is typically filled with a clean buffer fluid, which serves multiple purposes:
- It lubricates and cools the seal faces
- It provides a barrier between the process fluid and the atmosphere
- It allows for monitoring of the primary seal’s performance
How Tandem Seals Work
The inboard seal, located closest to the process fluid, acts as the primary sealing mechanism. It prevents the process fluid from escaping into the buffer fluid chamber. The outboard seal, positioned on the atmosphere side, contains the buffer fluid and acts as a backup in case of inboard seal failure. This dual seal design creates an effective safety barrier between the process fluid and the environment.
In a tandem seal configuration, the buffer fluid is typically unpressurized or maintained at a slightly lower pressure than the seal chamber pressure. This arrangement allows for seal reliability monitoring through pressure alarms and fluid level indicators. If the inboard seal fails, the pressure in the buffer fluid chamber will increase, triggering an alarm and alerting operators to take appropriate action.
Components of a Tandem Seal
Inboard (Primary) Seal
The inboard seal, also known as the primary seal, is the first line of defense against fluid leakage. It is located closest to the process fluid and bears the brunt of the seal chamber pressure. This seal is typically designed to handle the full pressure and temperature of the sealed fluid. The inboard seal consists of a set of seal rings, with one rotating and one stationary, creating a dynamic seal interface that prevents product leakage.
Outboard (Secondary) Seal
The outboard seal, or secondary seal, is positioned on the atmosphere side of the tandem configuration. It acts as a backup to the inboard seal, providing an additional layer of protection against leakage. In normal operation, the outboard seal faces less severe conditions than the inboard seal. However, it is designed to take over sealing responsibilities in case of inboard seal failure, ensuring continued operation and safety.
Buffer Fluid Reservoir and Circulation System
A critical component of tandem seals is the buffer fluid system. This system consists of a reservoir containing a clean, neutral fluid and a circulation mechanism. The buffer fluid, which is typically unpressurized, fills the space between the inboard and outboard seals.
Condition Monitoring Equipment
To ensure reliable operation and early detection of potential issues, tandem seals are equipped with various condition monitoring devices:
- Pressure Sensors: These monitor the pressure in the buffer fluid chamber, alerting operators to any deviations that might indicate seal wear or failure.
- Level Indicators: Used to monitor the buffer fluid level, providing insight into inboard seal performance an
Advantages of Tandem Seals
- Enhanced Safety: Tandem seals provide an effective safety barrier against dangerous fluids. The outboard seal acts as a backup, preventing leakage to the atmosphere if the inboard seal fails.
- Improved Reliability: The tandem configuration offers superior seal reliability compared to single seals. With two sets of seal rings working in series, the likelihood of complete seal failure is greatly reduced. If the primary seal experiences issues, the secondary seal can continue to function, allowing for continued operation until maintenance can be performed.
- Lower Operating Costs: Unlike pressurized dual seals, tandem seals utilize an unpressurized buffer fluid. This arrangement eliminates the need for complex pressurization systems, reducing both initial investment and ongoing maintenance costs. The simpler design of tandem seals also contributes to lower overall operating expenses.
- Easier Monitoring: Tandem seals facilitate straightforward condition monitoring. Pressure sensors and alarms can be installed to detect changes in the buffer fluid chamber, providing early warning of inboard seal wear or failure.
- Improved Heat Management: The buffer fluid in tandem seals helps dissipate heat generated by the seal faces, particularly in the inboard seal. This thermal management capability contributes to extended seal life and improved overall performance, especially in high-temperature applications.
Applications of Tandem Seals
- Pumps and Compressors: Tandem seals are widely used in centrifugal and reciprocating pumps as well as compressors. These seals effectively manage high-pressure differentials, ensuring minimal fluid leakage and optimal performance.
- Aerospace Industry: The aerospace sector employs tandem seals in various systems, including hydraulic actuators and fuel pumps. These seals provide redundancy and added reliability, crucial for maintaining the integrity of aerospace components under extreme conditions.
- Chemical Processing: Tandem seals are essential in chemical processing facilities where they handle aggressive and hazardous chemicals. By providing an additional barrier, tandem seals protect against leaks that could cause contamination or pose safety risks. They are particularly useful in applications involving volatile organic compounds (VOCs).
- Power Generation: In power plants, tandem seals are used in turbine and generator systems. They help manage the high pressures and temperatures associated with these applications, ensuring efficient operation and reducing downtime due to maintenance.
- Pharmaceutical Manufacturing: In pharmaceutical production, tandem seals are employed in mixers and reactors to maintain sterile environments. The dual-seal configuration ensures that no contaminants enter the process, preserving the purity and quality of pharmaceutical products.
- Water Treatment Plants: Tandem seals are used in pumps and mixers within water treatment facilities to handle various fluids under different pressure conditions. They ensure reliable operation and prevent leakage of potentially harmful substances into the environment.
- Oil and Gas Exploration: In offshore and onshore drilling operations, tandem seals are crucial for maintaining well integrity. They prevent leaks of hydrocarbons and other drilling fluids, thereby protecting the environment and enhancing operational safety.
- Food and Beverage Industry: Tandem seals are utilized in food processing equipment to prevent contamination and ensure hygienic conditions. The seals provide a dual barrier to protect against the ingress of contaminants and the egress of process fluids.
Conclusion
Tandem seals represent a crucial advancement in mechanical seal technology, offering a robust solution for challenging sealing applications. By combining an inboard and outboard seal with a buffer fluid system and condition monitoring equipment, tandem seals provide superior leak prevention and equipment protection. Their unique arrangement offers significant advantages over other double seal configurations, making them ideal for a wide range of applications in industries where reliability and safety are paramount.
Ready to enhance your equipment’s performance with top-quality tandem seals? Look no further than COWSEAL, your trusted mechanical seal manufacturer. Our expert team is prepared to guide you through selecting the perfect tandem seal solution for your specific needs.