In the realm of sealing technologies, brush seals and labyrinth seals are two distinct solutions employed to control fluid leakage and maintain pressure differences in rotating machinery. While both serve the purpose of sealing, their designs, materials, and performance characteristics differ significantly.
This article will delve into the intricacies of brush seals and labyrinth seals, comparing their structures, applications, and effectiveness in various industrial settings.
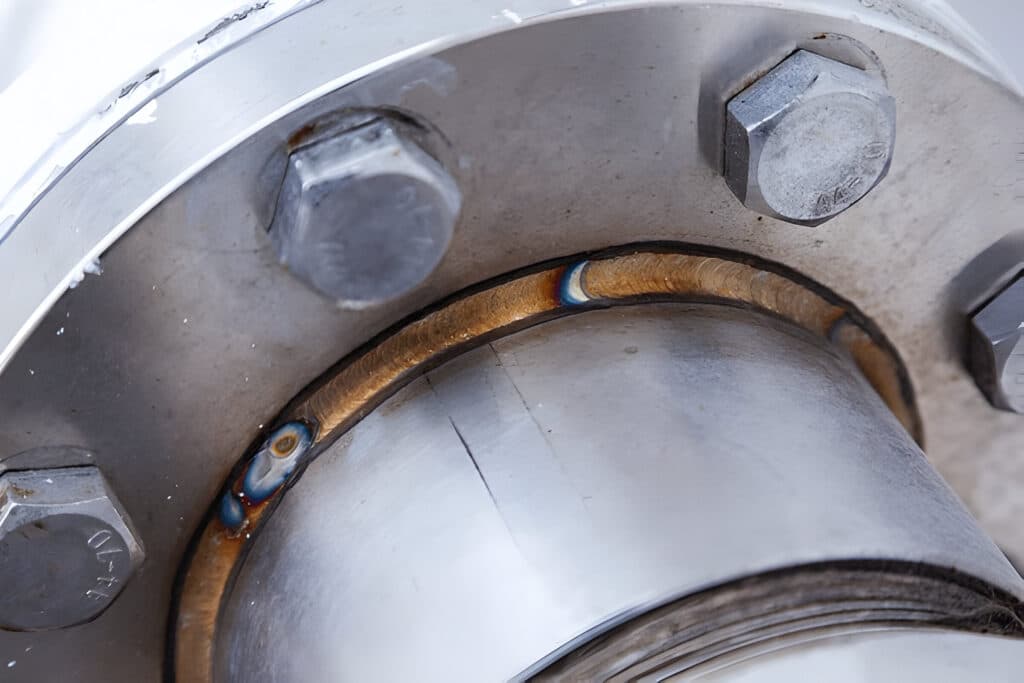
What Is Brush Seal
A brush seal is a type of mechanical seal that utilizes a dense pack of bristles, typically made from stainless steel, to create a flexible sealing mechanism between stationary and rotating components in turbomachinery. The bristles are angled in the direction of rotation, allowing for a compliant sealing interface that can accommodate radial movement and shaft excursions while maintaining minimal clearance. This unique design enables brush seals to provide effective sealing even under high pressure differentials and rotational speeds.
Brush seals offer several advantages over traditional labyrinth seals. The bristle pack conforms to the rotor surface, minimizing leakage gaps and reducing leakage flow. The compliance of the bristles allows for better accommodation of rotor dynamics, thermal growth, and other operational factors. Additionally, brush seals can be used in combination with labyrinth seals or other seal technologies to further enhance sealing performance.
The application of brush seals has expanded across various industries, including steam turbines, gas turbines, and aerospace engines. In steam turbine applications, brush seals can significantly reduce steam leakage, improving overall machine efficiency and reducing costly steam losses. Brush seals are also used in industrial gas turbines and jet engines to minimize leakage air flow, resulting in improved operational efficiencies.
What Is Labyrinth Seal
A labyrinth seal is a type of non-contacting seal that utilizes a series of intricate, maze-like passages to create a torturous path for fluid flow. The seal consists of a series of labyrinth teeth or fins arranged in a specific pattern, with each tooth creating a small pressure drop. As the fluid navigates through the labyrinth, it experiences a series of expansions and contractions, resulting in a significant pressure reduction across the seal.
Labyrinth seals rely on the principle of creating multiple pressure drops to minimize leakage flow. The effectiveness of a labyrinth seal depends on factors such as the number of labyrinth teeth, their geometry, and the clearance between the rotating and stationary components. The clearance is designed to be as small as possible while still allowing for safe operation and accommodating factors such as thermal expansion and rotor dynamics.
One of the main advantages of labyrinth seals is their non-contacting nature, which minimizes wear on the rotor surface and extends seal life. Labyrinth seals are also relatively simple in design and can be easily manufactured and maintained. However, they are sensitive to changes in clearance and can experience increased leakage if the clearance becomes too large due to wear or operational conditions.
Labyrinth seals find applications in various rotating machinery, such as steam turbines, gas turbines, and compressors. They are often used in combination with other seal technologies, such as brush seals or abradable seals, to provide a comprehensive sealing solution.
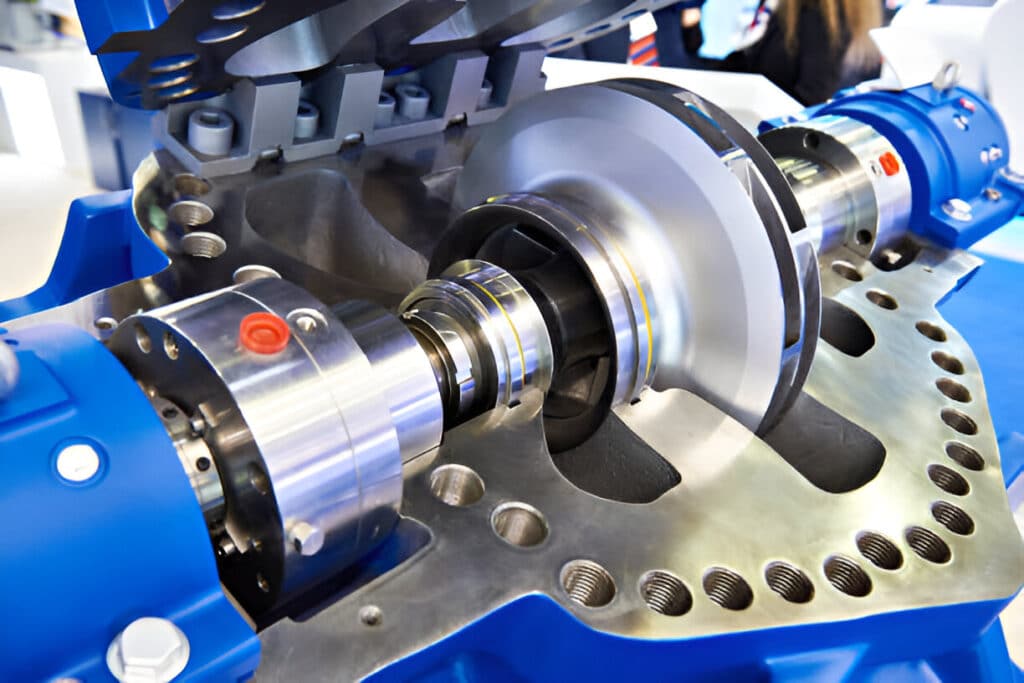
Key Differences Between Brush Seal and Labyrinth Seal
Sealing Mechanism
Brush seals consist of densely packed bristles, typically made of stainless steel, that form a compliant sealing interface. The bristles flex and adapt to rotor movements, maintaining a close clearance.
In contrast, labyrinth seals rely on a series of rigid teeth or knife edges that create a tortuous path for fluid flow. Labyrinth seals do not have a compliant sealing element like brush seals.
Contact
Brush seals are a contact-type seal, meaning the bristles make light contact with the rotor surface. This contact allows brush seals to accommodate rotor excursions and vibrations while maintaining effective sealing.
Labyrinth seals, on the other hand, are non-contact seals. They maintain a small clearance between the seal teeth and rotor, relying on the pressure drop across the labyrinth path to reduce leakage.
Leakage Reduction
Brush seals provide superior leakage reduction compared to labyrinth seals. The compliant bristle pack conforms to the rotor, minimizing leakage gaps. A single brush seal can reduce leakage by up to 90% compared to conventional labyrinth seals.
Labyrinth seals, while effective, have inherent leakage due to the clearance between the seal teeth and rotor. Leakage in labyrinth seals increases over time as the clearances increase due to wear and thermal growth.
Durability
Labyrinth seals generally have higher durability compared to brush seals. The rigid geometry of labyrinth seals makes them resistant to wear and deterioration.
Brush seals, due to their contacting nature, experience wear over time as the bristles rub against the rotor surface.
Temperature Range
Both brush seals and labyrinth seals can operate in a wide temperature range. However, brush seals have a slight advantage in high-temperature applications. Brush seal bristles, typically made of cobalt or nickel-based superalloys, can withstand temperatures up to 800°C (1,472°F). Labyrinth seals, depending on the material used, can operate at temperatures up to around 650°C (1,200°F). The compliant nature of brush seals allows them to accommodate thermal growth more effectively than rigid labyrinth seals.
Applications
Brush seals and labyrinth seals find applications in various turbomachinery, including steam turbines, gas turbines, compressors, and pumps. Brush seals are particularly effective in applications with high pressure differentials, such as steam turbine gland sealing and gas turbine bearing sump sealing. They are also used in combination with labyrinth seals to enhance overall sealing performance.
Labyrinth seals are widely used in applications with lower pressure differentials and where non-contact sealing is preferred. They are commonly found in turbocharger sealing, compressor eye sealing, and as inter-stage seals in turbines and compressors.