In the machinery industry, selecting the appropriate sealing solution is paramount for optimizing equipment performance and longevity. Two primary categories of seals employed in various applications are contact seals and non-contact seals, each with distinct characteristics and advantages.
This blog post will delve into the fundamental differences between contact and non-contact seals, examining factors such as friction, sealing mechanisms, wear and tear, speed capability, sealing efficiency, and typical applications. By understanding these key distinctions, industry professionals can make informed decisions when choosing seals for their specific machinery requirements.
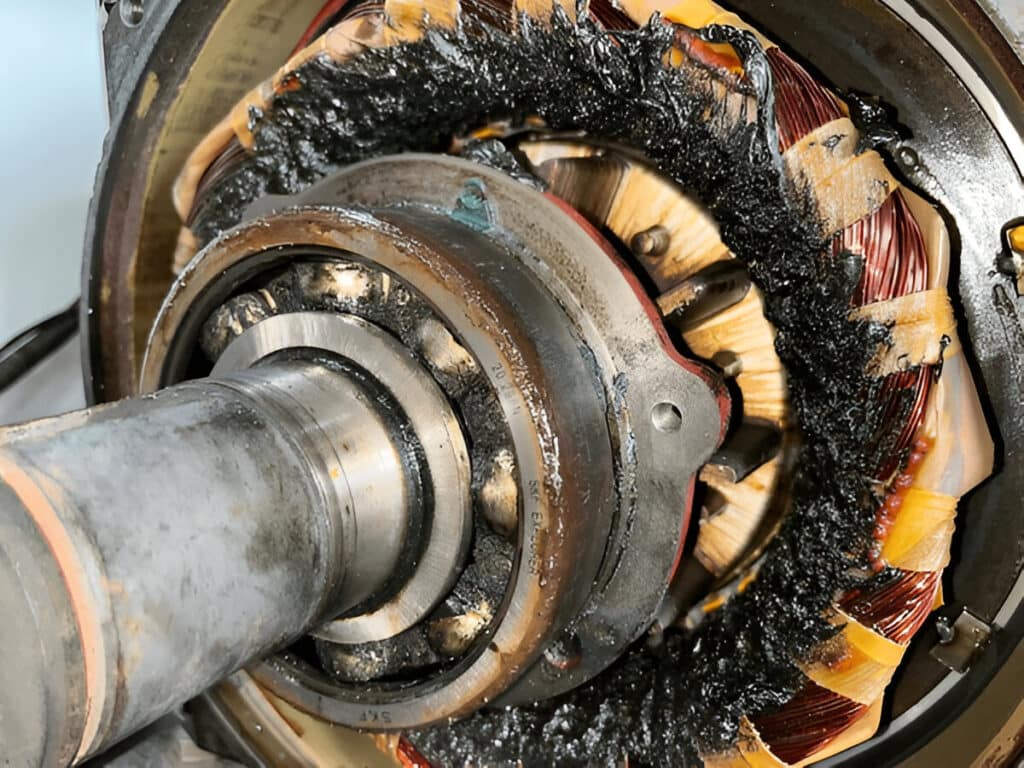
What Is Contact Seal
A contact seal is a type of seal that operates by maintaining direct physical contact between the sealing surfaces to prevent leakage. The sealing surfaces are typically made of materials such as elastomers, polymers, or soft metals that deform under pressure to create a tight seal.
The most common examples of contact seals include:
- O-rings: Circular cross-section elastomeric seals that sit in grooves and compress between two surfaces.
- Lip seals: Seals with a flexible lip that presses against a shaft or housing to prevent leakage.
- Gaskets: Flat seals made of materials like rubber, cork, or paper that compress between two stationary surfaces.
What Is Non Contact Seal
Non contact seals, also known as clearance seals or gap seals, operate without direct physical contact between the sealing surfaces. Instead, they rely on a small gap or clearance between the rotating and stationary components to minimize leakage.
Some common types of non contact seals include:
- Labyrinth seals: A series of alternating grooves and teeth that create a tortuous path for the fluid, reducing leakage through a pressure drop.
- Floating ring seals: A type of mechanical seal that uses a floating ring between the rotating and stationary components to create a dynamic seal.
- Brush seals: Consists of densely packed bristles that form a seal against a rotating shaft, allowing for some leakage while minimizing friction.
Non contact seals are designed to operate with a controlled leakage rate, which is often acceptable in applications where a small amount of leakage is tolerable. They offer advantages such as reduced friction, longer seal life, and the ability to handle higher speeds and temperatures compared to contact seals.
Key Differences Between Contact and Non Contact Seals
Friction
One of the primary differences between contact and non contact seals lies in the amount of friction generated during operation. Contact seals, such as mechanical seals and lip seals, rely on direct physical contact between the seal faces to prevent leakage. This contact inevitably creates friction, which can lead to heat generation and increased power consumption.
In contrast, non contact seals, like labyrinth seals and floating ring seals, maintain a small gap between the sealing surfaces, resulting in minimal friction and reduced heat generation.
Sealing Mechanism
Contact seals achieve sealing through direct physical contact between the sealing surfaces, often utilizing a combination of materials with different hardness levels to ensure a tight seal. The sealing effectiveness depends on factors such as surface finish, contact pressure, and the materials used.
Non contact seals, on the other hand, rely on a different sealing mechanism. They create a tortuous path for the fluid, using a series of cavities, grooves, or chambers to reduce leakage. The sealing efficiency of non contact seals is influenced by the design of the sealing geometry and the operating conditions.
Wear & Tear
The presence of friction in contact seals leads to increased wear and tear on the sealing surfaces over time. As the sealing faces rub against each other, they gradually wear down, reducing the sealing effectiveness and potentially leading to failure.
Non contact seals experience significantly less wear and tear due to the absence of direct contact between the sealing surfaces. This results in longer seal life and reduced maintenance requirements compared to contact seals.
Speed Capability
The speed capability of contact seals is generally limited by the amount of friction and heat generated at high rotational speeds. Excessive heat can cause thermal distortion, material degradation, and premature failure of the sealing components. As a result, contact seals are typically used in applications with moderate speed requirements.
Non contact seals, with their low friction characteristics, are well-suited for high-speed applications. The absence of direct contact allows them to operate at higher rotational speeds without generating excessive heat or experiencing significant wear.
Sealing Efficiency
Contact seals, when properly designed and maintained, can provide excellent sealing efficiency. The direct contact between the sealing surfaces creates a tight barrier against fluid leakage, making them suitable for applications that require high levels of sealing performance. However, the sealing efficiency of contact seals can deteriorate over time due to wear and damage to the sealing faces.
Non contact seals, while not providing the same level of sealing efficiency as contact seals, can still offer adequate sealing performance for many applications.
Applications
The choice between contact and non contact seals depends on the specific requirements of the application. Contact seals are commonly used in applications that demand high sealing efficiency, such as in pumps, compressors, and mixers. They are also suitable for low to moderate speed applications and environments with relatively clean fluids.
Non contact seals find widespread use in high-speed applications, such as in turbines, expanders, and centrifugal compressors. They are also preferred in applications involving abrasive or dirty fluids, as the absence of direct contact minimizes the risk of seal damage due to contaminants.