In industrial machinery, seals are critical components that prevent leakage and contamination of fluids or gases. Two common types of seals used in various applications are mechanical seals and dynamic seals, each with distinct characteristics and advantages.
This article will delve into the key differences between mechanical and dynamic seals, focusing on their design complexity, supported motion types, typical applications, durability, and cost factors. By understanding these distinctions, engineers and maintenance professionals can make informed decisions when selecting the most suitable seal for their specific machinery requirements.
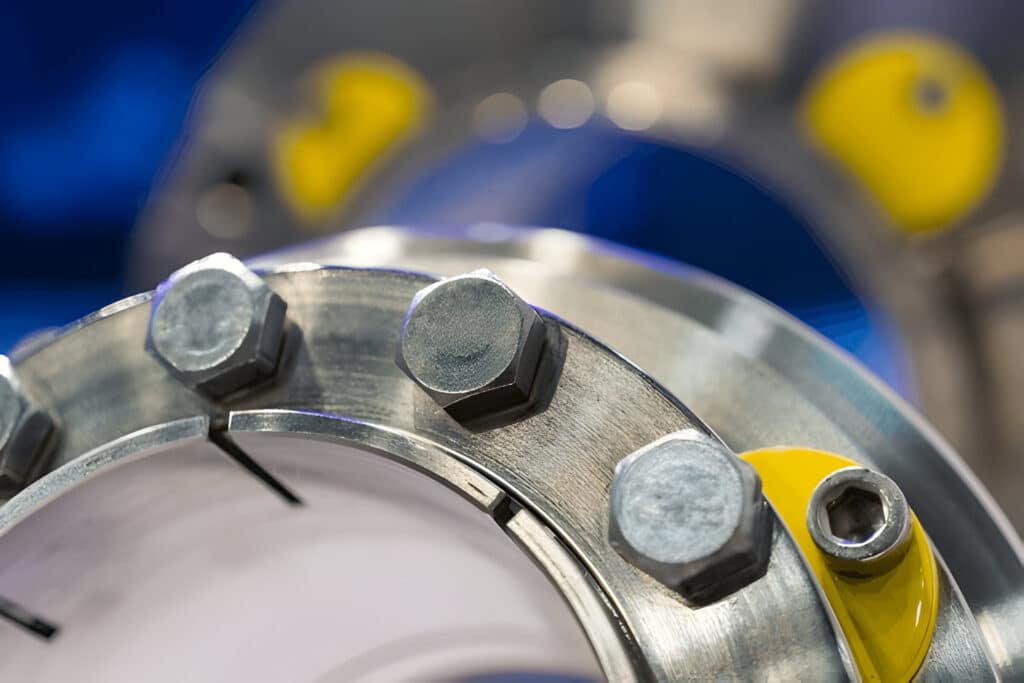
What Is Mechanical Seal
A mechanical seal is a device used to prevent leakage of fluids between two surfaces that are in relative motion. It consists of two main components: a stationary part called the stator and a rotating part called the rotor. The stator is typically mounted on the housing, while the rotor is attached to the shaft.
The sealing action is achieved by maintaining a small gap between the stator and rotor faces, which are highly polished and lapped to create an extremely flat surface. This gap is filled with a thin film of fluid, often from the process being sealed. The fluid film helps lubricate the faces and prevents direct contact between them, minimizing wear.
Mechanical seals are widely used in pumps, mixers, compressors, and other rotary equipment to contain process fluids and prevent environmental contamination. They offer reliable sealing performance and can handle a wide range of pressures, temperatures, and fluid types.
What Is Dynamic Seal
Dynamic seals, also known as rotary seals or shaft seals, are designed to prevent leakage between a stationary housing and a rotating shaft. Unlike mechanical seals, which rely on flat sealing faces, dynamic seals employ a flexible sealing element that maintains contact with the shaft surface.
The most common types of dynamic seals include:
- Lip seals: These consist of a flexible elastomeric lip that presses against the shaft surface. The lip is often spring-loaded to maintain contact pressure and compensate for wear. Lip seals are simple, compact, and cost-effective, making them suitable for a wide range of applications.
- Packed glands: Packed glands use a compressed packing material, such as braided fibers or graphite rings, to create a seal around the shaft. The packing is held in place by a gland follower and compressed by adjusting the gland bolts. Packed glands are versatile and can handle high temperatures and pressures.
- Labyrinth seals: Labyrinth seals create a tortuous path for the fluid using a series of closely spaced rings or grooves. While they do not provide a complete seal, they significantly reduce leakage by creating a pressure drop across the seal. Labyrinth seals are non-contacting and suitable for high-speed applications.
Dynamic seals are used in various machinery, including gearboxes, turbines, and bearing housings. They are generally less complex and more cost-effective than mechanical seals but may have limitations in terms of pressure, speed, and fluid compatibility.
Key Differences Between Mechanical Seal and Dynamic Seal
Design Complexity
Mechanical seals have a more complex design compared to dynamic seals. They consist of multiple components, including primary and secondary sealing faces, springs, and other parts that must be precisely engineered and manufactured.
In contrast, dynamic seals, such as O-rings and lip seals, have a simpler construction, often made from a single piece of elastomeric material.
Motion Type Supported
Mechanical seals are designed to handle rotary motion, making them suitable for equipment with rotating shafts, such as pumps, mixers, and agitators. They can effectively seal against leaks while accommodating the continuous rotation of the shaft.
On the other hand, dynamic seals are versatile and can handle various types of motion, including rotary, reciprocating, and oscillating movements. This versatility makes them applicable in a wide range of machinery, such as hydraulic and pneumatic cylinders, valves, and actuators.
Applications
Due to their ability to handle high pressures, temperatures, and speeds, mechanical seals are commonly used in demanding industrial applications. They are prevalent in the oil and gas, chemical processing, pharmaceutical, and power generation industries, where reliable sealing is critical for process integrity and safety.
Dynamic seals find applications in a broader range of industries, including automotive, aerospace, manufacturing, and hydraulic systems. They are suitable for sealing fluids and gases in various operating conditions, making them a popular choice for many general-purpose sealing applications.
Durability
The durability of mechanical seals depends on factors such as proper installation, maintenance, and operating conditions. When installed and maintained correctly, mechanical seals can provide long-lasting sealing performance. However, they are more susceptible to wear and damage if not operated within their designed parameters or if exposed to abrasive or corrosive media.
Dynamic seals, especially those made from high-quality elastomers, offer excellent durability and resilience. They can withstand a wide range of operating conditions and provide reliable sealing over an extended period. The simplicity of their design also contributes to their durability, as there are fewer components that can fail or wear out.
Cost
Mechanical seals are generally more expensive than dynamic seals due to their complex design and precision manufacturing requirements. The cost of mechanical seals includes not only the seal itself but also the installation and maintenance expenses associated with ensuring proper functionality.
Dynamic seals, on the other hand, are more cost-effective. Their simple design and wide availability make them an economical choice for many sealing applications. The lower cost of dynamic seals makes them attractive for use in high-volume production and applications where frequent seal replacement is necessary.