Seal chambers and stuffing boxes are two essential components in rotating equipment that serve to prevent fluid leakage and protect the shaft and bearings. While both are designed to control leakage around a shaft, they differ in their design, sealing method, functionality, maintenance requirements, cost, and optimal applications.
In this article, we will dive deep into the key differences between seal chambers and stuffing boxes, exploring their unique characteristics, advantages, and limitations across various dimensions. By the end, you’ll have a thorough understanding of when and why to use each type of shaft sealing solution in different machinery contexts.
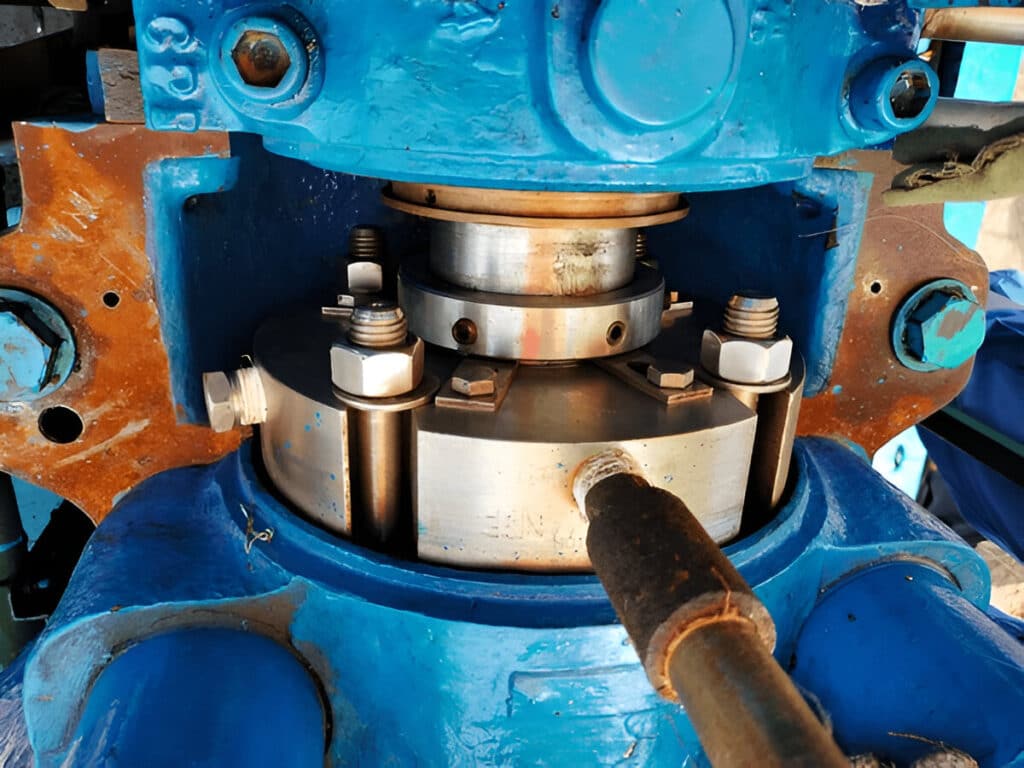
What Is Seal Chamber
A seal chamber is a cavity or space that surrounds the shaft of a pump or other rotating equipment where it passes through the casing or housing. The primary purpose of a seal chamber is to contain the shaft sealing system, which is responsible for preventing fluid leakage along the rotating shaft.
The seal chamber provides a controlled environment for the shaft seal to operate in. It is typically designed with features such as:
- A recessed area or “gland” to hold the sealing elements in place against the shaft
- Ports or connections for circulating a sealing fluid or barrier fluid to cool and lubricate the seal faces
- A drain port at the bottom to allow any accumulated leakage to be safely drained away
- A vent at the top to prevent air or gas from being trapped in the chamber
In general, the seal chamber must be large enough to accommodate the sealing elements and allow for proper circulation of sealing fluids, but not so large as to create excessive dead space where solids could settle out or corrosive fluids could stagnate. The internal shape should promote smooth, turbulence-free flow to avoid seal issues.
What Is Stuffing Box
A stuffing box is a type of seal chamber that is commonly used with compression packing as the shaft sealing element. It gets its name from the fact that packing material, historically a soft, pliable material like rope or rags, would literally be “stuffed” into the space around the shaft to form a seal.
A stuffing box consists of an enlarged cylindrical space surrounding the shaft where it passes through the pump casing or machine housing. Key elements include:
- A cylindrical “bore” or inside diameter only slightly larger than the shaft, providing a close fit
- A means of compressing the packing material axially to expand it radially against the shaft, usually a flanged “gland follower” bolted to the stuffing box face
- Ports or fittings to allow adding packing, lubricating oil, or sealing fluid
- A drain connection to carry away leakage
The stuffing box provides an enclosure to contain the packing rings and allow them to be compressed to form a tight seal against the shaft. The depth and diameter of the stuffing box depend on the number of packing rings required, which is determined by the shaft size, operating pressure, and fluid properties.
As the packing is compressed and expands radially, it conforms to the shaft surface and forms a tight but flexible seal. A small amount of controlled leakage is generally required to lubricate and cool the packing, so stuffing boxes are not considered zero-leakage seals.
Differences Between Seal Chamber and Stuffing Box
Design
The design of seal chambers and stuffing boxes differs significantly. Seal chambers are typically larger and more complex, featuring a spacious housing that accommodates mechanical seals, bushings, and circulation systems. In contrast, stuffing boxes have a simpler, more compact design, consisting of a cylindrical housing that holds packing material and a gland follower.
Sealing Method
Seal chambers rely on mechanical seals to prevent fluid leakage. These seals are precision-engineered components that create a tight barrier between the rotating shaft and the stationary housing. Stuffing boxes, on the other hand, use packing material, such as braided fibers or graphite rings, which is compressed around the shaft to form a seal.
Functionality
The primary function of both seal chambers and stuffing boxes is to prevent fluid leakage from the pump or equipment. However, seal chambers offer superior sealing performance and are better suited for high-pressure, high-temperature, and corrosive applications. Stuffing boxes are more cost-effective and are commonly used in less demanding applications or older equipment.
Leakage Control
Seal chambers provide excellent leakage control, as mechanical seals maintain a tight, leak-free barrier between the process fluid and the environment. Properly installed and maintained mechanical seals can operate with virtually no visible leakage. Stuffing boxes, while effective at reducing leakage, typically allow a small amount of controlled leakage, which is necessary to lubricate and cool the packing material.
Maintenance
Maintaining seal chambers involves periodic inspection, cleaning, and replacement of mechanical seals and associated components. This process can be more complex and time-consuming compared to stuffing box maintenance. Stuffing boxes require regular adjustment of the gland follower to compress the packing material and control leakage. The packing material also needs to be replaced periodically as it wears out.
Cost
Seal chambers are generally more expensive than stuffing boxes due to their complex design, precision components, and advanced sealing technology. The initial cost of a seal chamber, including the mechanical seals, can be significantly higher than that of a stuffing box. However, the long-term cost savings from reduced leakage and improved reliability may justify the investment in a seal chamber for critical applications.
Cooling and Circulation
Seal chambers often incorporate cooling and circulation systems to manage heat generated by the mechanical seals and maintain optimal operating conditions. These systems can include cooling jackets, heat exchangers, and recirculation lines. Stuffing boxes typically rely on the controlled leakage of the process fluid to provide cooling and lubrication to the packing material.
Applications
Seal chambers are widely used in modern pumps, mixers, and other rotating equipment, particularly in industries such as oil and gas, chemicals, and pharmaceuticals. They are preferred for applications involving high pressures, high temperatures, corrosive fluids, or strict environmental regulations. Stuffing boxes are still common in older equipment, lower-pressure applications, and industries where the cost is a primary concern, such as water treatment and general manufacturing.