Mechanical seal face flatness is a critical parameter that directly impacts the performance and reliability of sealing systems in rotating equipment. Maintaining proper flatness ensures optimal contact between the seal faces, minimizing leakage and extending seal life.
This article explores the concept of seal face flatness, its significance in mechanical seals, and the factors that influence it. We will discuss how flatness is measured and the consequences of poor flatness, providing insights to help optimize seal performance in various industrial applications.
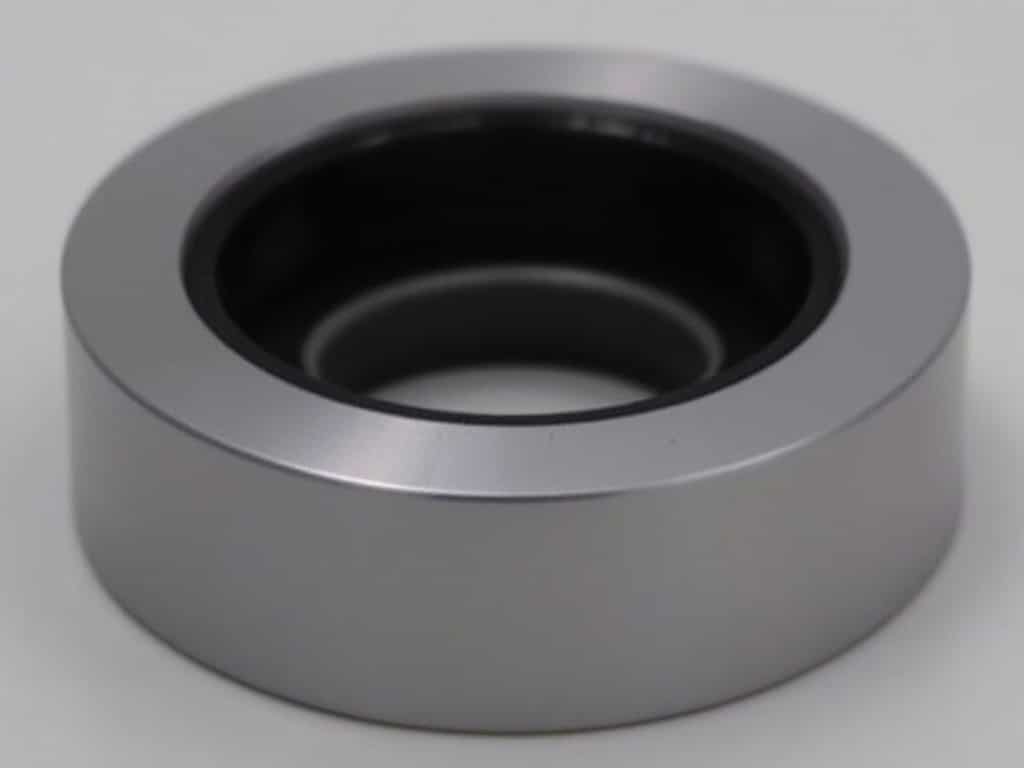
What Is Seal Face Flatness
Seal face flatness refers to the degree of evenness and smoothness of the surface of a mechanical seal face. A perfectly flat seal face would have no irregularities or deviations from a completely level plane. However, in reality, all seal faces have some degree of deviation from perfect flatness due to manufacturing limitations and material properties.
Flatness is typically measured in units of length, such as micrometers (μm) or helium light bands (HLB). The flatness value represents the maximum deviation of the seal face from a perfectly flat reference plane. For example, a seal face with a flatness of 2 μm means that the highest point on the surface is 2 μm above the lowest point.
Why Is Flatness Important in Mechanical Seals
Flatness is a critical factor in the performance and longevity of mechanical seals for several reasons:
- Leakage prevention: Flat seal faces form a better seal against each other, reducing the risk of fluid leakage. Irregularities on the seal face can create gaps or channels that allow fluid to escape.
- Heat dissipation: Flat seal faces have more surface area in contact with each other, allowing for better heat transfer and dissipation. This helps to prevent overheating and premature wear of the seal faces.
- Uniform pressure distribution: Flat seal faces ensure that the contact pressure between the faces is evenly distributed. Uneven pressure distribution can lead to localized wear and damage to the seal faces.
- Reduced friction: Smooth, flat seal faces minimize friction between the rotating and stationary components of the seal. Lower friction results in less heat generation and improved energy efficiency.
- Extended seal life: By promoting better sealing, heat dissipation, pressure distribution, and reduced friction, flat seal faces contribute to longer seal life and reduced maintenance requirements.
How Is Flatness Measured
Flatness of mechanical seal faces is typically measured using optical flatness measurement techniques. The most common methods include:
- Monochromatic light interferometry: This method uses a single wavelength of light (usually helium) to create an interference pattern on the seal face. The pattern reveals surface irregularities, allowing for the calculation of flatness.
- White light interferometry: Similar to monochromatic light interferometry, this technique uses a broader spectrum of light to create interference patterns. It is particularly useful for measuring surface roughness in addition to flatness.
- Optical profilometry: This method uses a laser or other light source to scan the seal face surface and create a 3D map of its topography. The data is then analyzed to determine flatness and other surface characteristics.
Factors Affecting Seal Face Flatness
Material
The material properties of the seal faces significantly influence their flatness. Different materials exhibit varying degrees of hardness, elasticity, and thermal expansion, which can affect the flatness of the sealing surfaces. For example, softer materials like carbon graphite are more prone to deformation under pressure, while harder materials like silicon carbide maintain their flatness better.
Manufacturing Processes
The manufacturing processes used to create the seal faces also play a significant role in determining their flatness. Lapping and polishing techniques are commonly employed to achieve the desired level of flatness. Inconsistencies or imperfections during these processes can result in variations in flatness across the sealing surface.
Thermal Expansion
Temperature changes can cause the seal face materials to expand or contract, leading to deviations from the original flatness. Different materials have different coefficients of thermal expansion, meaning they expand and contract at different rates when subjected to temperature variations. This can cause distortion of the sealing surfaces, especially if the mating faces are made of dissimilar materials.
Pressure Variations
Fluctuations in the pressure acting on the seal faces can also affect their flatness. High pressure can cause the faces to deform, while sudden pressure changes can lead to uneven loading and distortion.
Shaft Misalignment
Misalignment between the rotating and stationary components of a mechanical seal can result in uneven contact between the seal faces. This misalignment can be caused by factors such as improper installation, shaft runout, or bearing wear. When the faces are not perfectly aligned, it can lead to localized high spots and low spots on the sealing surface, compromising the overall flatness.
Consequences of Poor Flatness
Leakage
One of the primary consequences of poor seal face flatness is increased leakage. When the faces are not flat, gaps can form between them, allowing the sealed fluid to escape. Even small deviations in flatness can create leak paths, compromising the sealing efficiency and leading to product loss or contamination.
Accelerated Wear
Poor flatness can also accelerate the wear of the seal faces. When the faces are not perfectly flat, they experience uneven contact and loading. This can result in localized high-pressure zones, leading to increased friction and wear. Accelerated wear reduces the lifespan of the seals and necessitates more frequent replacements.
Heat Generation
Seal faces with poor flatness are more prone to generating excessive heat during operation. The uneven contact between the faces causes increased friction, which in turn generates heat. This heat buildup can lead to thermal distortion of the seal components, further exacerbating the flatness issues. Excessive heat can also degrade the sealing materials and reduce their effectiveness over time.
Vibration and Noise
Flatness deviations can contribute to increased vibration and noise in mechanical seals. When the faces are not flat, they may experience intermittent contact or chattering, resulting in vibrations that can propagate through the sealing system. These vibrations not only generate noise but can also cause premature failure of other components in the assembly.
Reduced Sealing Performance
Poor seal face flatness directly impacts the overall sealing performance. Flat faces are essential for maintaining a thin, uniform fluid film between the sealing surfaces. When the flatness is compromised, the fluid film becomes disrupted, leading to increased friction, wear, and leakage. This reduction in sealing performance can have detrimental effects on the efficiency and reliability of the entire system.