Mechanical seals are integral components in rotating equipment, preventing fluid leakage and maintaining system pressure. Seal chamber pressure, a critical factor influencing seal performance and lifespan, is determined by various design and operational parameters.
This article explores the concept of seal chamber pressure, examining the factors that influence it and the design features used to manage it effectively. We will also discuss the suitability of different mechanical seal types for various pressure conditions.
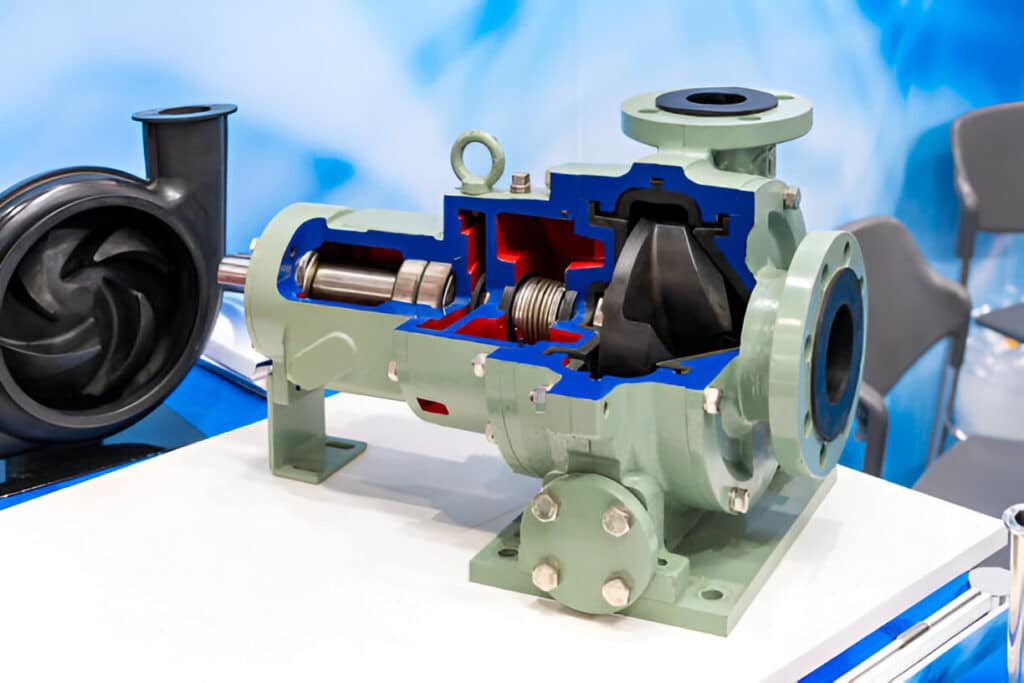
What Is Seal Chamber Pressure in Mechanical Seals
Seal chamber pressure refers to the fluid pressure within the cavity that houses the mechanical seal. This pressure plays a significant role in the performance and longevity of the seal, as it affects factors such as lubrication, cooling, and the prevention of contaminant ingress.
In a typical mechanical seal arrangement, the seal chamber is located between the pump casing and the atmosphere. The pressure within this chamber is determined by various factors, including the pump’s operating conditions, the seal design, and the fluid being pumped.
Maintaining the appropriate seal chamber pressure is critical for several reasons:
- Proper lubrication: Adequate pressure ensures that the seal faces are supplied with a thin film of fluid, reducing friction and wear.
- Cooling: The fluid in the seal chamber helps dissipate heat generated by the seal faces, preventing overheating and premature failure.
- Contaminant exclusion: Positive pressure within the seal chamber helps prevent external contaminants from entering and damaging the seal faces.
Factors Influencing Pressure Within the Seal Chamber
Pump Operating Conditions
The operating conditions of the pump have a direct impact on the seal chamber pressure. Factors such as the pump’s discharge pressure, suction pressure, and rotational speed influence the pressure within the seal cavity.
Higher discharge pressures generally result in increased seal chamber pressure, while lower suction pressures can lead to reduced pressure or even vacuum conditions within the chamber.
Seal Design and Arrangement
The design of the mechanical seal and its arrangement within the pump also affect the seal chamber pressure. Several design elements come into play:
- Balance ratio: The balance ratio determines the hydraulic loading on the seal faces. Seals with higher balance ratios tend to operate at lower pressures, while lower balance ratios result in higher pressures.
- Seal face geometry: The geometry of the seal faces, such as face width and surface finish, influences the pressure distribution within the seal chamber.
- Piping plan: The piping plan used in conjunction with the mechanical seal affects the pressure in the seal chamber. For example, a Plan 11 (recirculation from pump discharge to seal) increases pressure, while a Plan 13 (recirculation from seal chamber to suction) reduces pressure.
Fluid Properties
The properties of the fluid being pumped also influence the pressure within the seal chamber. Factors such as viscosity, specific gravity, and vapor pressure come into play.
Higher viscosity fluids may require increased seal chamber pressure to maintain adequate lubrication between the seal faces. Fluids with high vapor pressures can lead to cavitation and reduced pressure within the seal chamber.
Types of Mechanical Seals and Pressure Suitability
Seal Type | Pressure Range | Characteristics |
---|---|---|
Single Spring Pusher Seal | Low to moderate | Suitable for pressures up to 20 bar. Simple design, cost-effective, and reliable for general-purpose applications. |
Balanced Seal | Moderate to high | Designed for pressures between 20 to 70 bar. Utilizes balanced geometry to minimize the effect of pressure on seal faces, reducing wear and extending seal life. |
Double Seal | Low to high | Consists of two seals arranged in tandem, with a barrier fluid between them. Suitable for pressures up to 100 bar. Provides enhanced safety and reliability in demanding applications. |
Cartridge Seal | Low to high | Pre-assembled and pre-adjusted seal unit. Accommodates a wide pressure range depending on the specific design. Simplifies installation and maintenance. |
Gas Seal | Low to high | Specifically designed for sealing gases. Can handle pressures up to 200 bar. Utilizes non-contacting seal faces to minimize wear and friction. |
Design Features for Managing Pressure
To effectively manage pressure within the seal chamber, mechanical seals incorporate various design features. These features ensure optimal sealing performance and longevity across different pressure ranges.
Balanced Seal Faces
Balanced seal faces are designed to minimize the impact of pressure on the sealing surfaces. By reducing the effective sealing area exposed to the pressure, balanced seals maintain a consistent sealing force regardless of fluctuations in the seal chamber pressure. This design feature prolongs seal life and improves sealing efficiency in moderate to high-pressure applications.
Multiple Springs
Mechanical seals often employ multiple springs to provide uniform sealing force distribution. By using a series of smaller springs instead of a single large spring, the sealing force is evenly applied around the circumference of the seal faces. This multi-spring arrangement ensures consistent sealing performance and reduces the risk of pressure-induced deformation or leakage.
Pressure-Responsive Geometry
Some mechanical seals feature pressure-responsive geometry, which allows the seal faces to adapt to changes in the seal chamber pressure. As the pressure increases, the geometry of the seal faces automatically adjusts to maintain the optimal sealing gap. This self-adjusting mechanism helps prevent excessive wear and maintains sealing effectiveness across a wide pressure range.
Barrier Fluid Systems
Double seals and tandem seals incorporate barrier fluid systems to manage pressure and enhance sealing performance. The barrier fluid, typically a compatible liquid or gas, is maintained at a higher pressure than the process fluid. This pressure differential prevents the process fluid from entering the sealing interface and provides lubrication and cooling to the seal faces. Barrier fluid systems effectively isolate the mechanical seal from the potentially harmful effects of high-pressure process fluids.