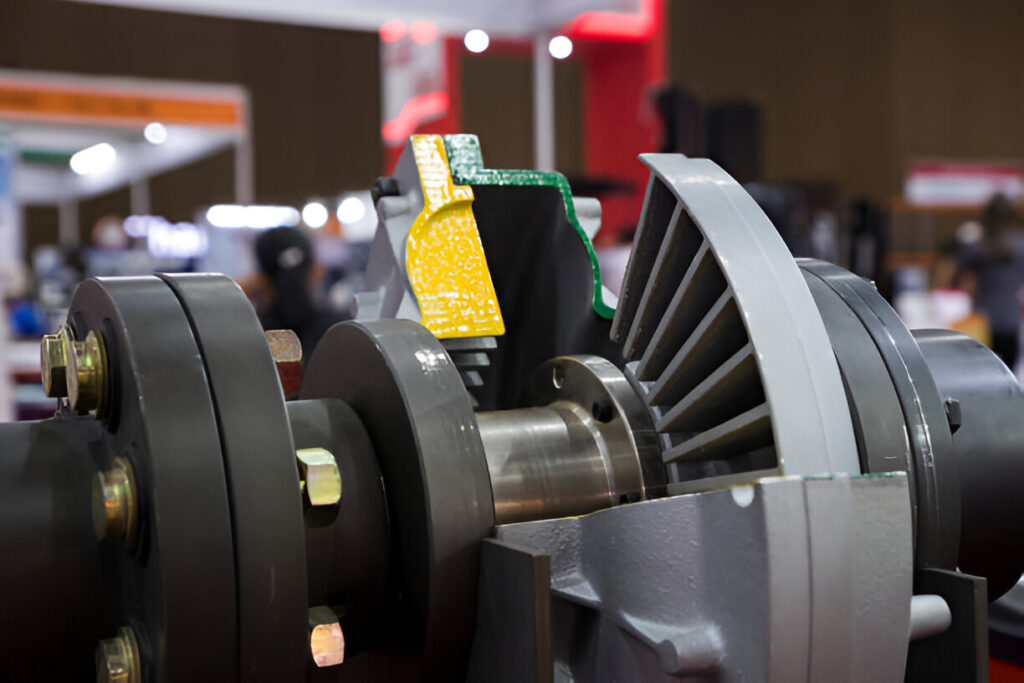
What Is Plan 53a
Plan 53a is a type of mechanical seal support system that provides a pressurized barrier fluid to the seal cavity. This barrier fluid maintains a higher pressure than the process fluid, preventing process fluid from entering the seal cavity and causing damage to the seal faces. The barrier fluid is typically a clean, compatible liquid that is maintained at a pressure of 15-30 psi above the seal chamber pressure.
In a Plan 53a system, the barrier fluid is supplied from a reservoir that is pressurized by an external source, such as a nitrogen bottle or a plant instrument air supply. The pressurized reservoir is connected to the seal cavity through a series of valves and piping, allowing the barrier fluid to flow into the seal cavity and maintain the desired pressure differential.
Advantages of 53a
- Lower operating costs: Due to the use of a bladder accumulator as the barrier fluid reservoir, eliminating the need for a separate pressure source and reducing energy consumption.
- Simpler design: With fewer components, leading to easier maintenance and lower likelihood of failure compared to the more complex setups of 53b and 53c.
- Versatile pressure range: Suitable for a wide range of pressure ranges, making it a versatile option for various applications.
- Space-efficient: Requires less space for installation due to its compact design, making it ideal for facilities with limited room for seal support systems.
- Adequate cooling: Provides adequate cooling for most applications without the need for additional cooling systems, which are often required in 53b and 53c setups.
- Effective contamination protection: Offers effective protection against particulates, ensuring reliable operation and extended seal life in environments with moderate contamination levels.
- Single seal system: Supports a single seal system, making it a cost-effective choice for applications that do not require multiple seals or redundancy.
Disadvantages of 53a
- Limited pressure range: Plan 53a is designed for lower-pressure applications, typically up to 300 psig. This makes it less suitable for high-pressure environments where Plan 53b or 53c would be more appropriate.
- No gas absorption: Unlike Plan 53b, which includes a bladder accumulator to absorb gases that may permeate through the seal faces, Plan 53a does not have this feature. This can lead to gas buildup in the barrier fluid, potentially affecting seal performance and reliability.
- No cooling system: Plan 53a does not incorporate a cooling system for the barrier fluid, which can be problematic in high-temperature applications. In contrast, Plan 53c includes a heat exchanger to maintain optimal barrier fluid temperature, making it more suitable for demanding thermal conditions.
- Particulate sensitivity: The absence of a filtration system in Plan 53a makes it more susceptible to particulate contamination compared to Plan 53b and 53c, which include particle filters. This can lead to increased wear on seal faces and reduced seal life in environments with high particulate levels.
- Single seal support: Plan 53a is designed to support a single mechanical seal, whereas Plan 53b and 53c can accommodate multiple seals in series. This limitation may restrict the use of Plan 53a in applications requiring redundant sealing arrangements for enhanced safety and reliability.
- Higher maintenance requirements: The simpler design of Plan 53a may result in more frequent maintenance intervals compared to Plan 53b and 53c, which offer additional features to maintain barrier fluid quality and extend seal life.
When to Use 53a
Plan 53a is best suited for single seal applications with clean, non-condensing process fluids at moderate temperatures and pressures. It is a cost-effective solution for many general-purpose sealing applications where the process conditions do not require advanced features like cooling or gas absorption.
What Is Plan 53b
API Plan 53b is a seal plan designed for dual unpressurized seals with a barrier fluid reservoir providing buffer fluid for the outer seal. This plan utilizes an external reservoir to supply barrier fluid to the outer seal, which serves as a buffer between the process fluid and the atmosphere. The reservoir is maintained at a pressure lower than the process pressure, allowing the barrier fluid to act as a lubricant and coolant for the seal faces.
In Plan 53b, the barrier fluid is typically a clean, compatible liquid that is immiscible with the process fluid. The reservoir is sized to accommodate thermal expansion and provide an adequate fluid volume for the seal’s operation. A level transmitter monitors the barrier fluid level in the reservoir, ensuring that it remains within the acceptable range.
Advantages of 53b
- Wider pressure range: Plan 53b can handle a broader range of pressures compared to 53a and 53c, making it more versatile for various applications. This flexibility allows Plan 53b to be used in a greater number of industrial settings.
- Enhanced gas absorption: The barrier fluid in Plan 53b is designed to absorb gases more effectively than the fluids used in 53a and 53c. This improved gas absorption capability helps maintain the integrity of the seal and prevents the accumulation of harmful gases in the system.
- Superior cooling properties: Plan 53b incorporates a more efficient cooling system compared to 53a and 53c. The enhanced cooling capabilities help maintain optimal operating temperatures, extending the life of the seal and reducing the risk of failure due to excessive heat.
- Effective particulate handling: The barrier fluid in Plan 53b is better equipped to handle particulates compared to 53a and 53c. This advantage is particularly important in environments with high levels of dust, dirt, or other contaminants that can compromise seal performance.
- Support for multiple seal systems: Plan 53b is designed to support a greater number of seal systems compared to 53a and 53c. This feature makes Plan 53b a more cost-effective solution for facilities that require multiple seals, as it reduces the need for additional support systems.
Disadvantages of 53b
- Limited pressure range: Plan 53b seals have a narrower pressure range compared to 53a and 53c seals, which can limit their applicability in certain industrial settings. This means that 53b seals may not be suitable for processes that involve high or low-pressure extremes, requiring the use of alternative seal plans.
- Higher cost: The complexity of Plan 53b seals, which include a barrier fluid reservoir and pressure source, often results in a higher initial investment compared to the simpler 53a and 53c configurations. The additional components and maintenance requirements associated with 53b seals can also lead to increased long-term costs.
- Increased maintenance: Plan 53b seals require more frequent monitoring and maintenance due to the presence of the barrier fluid reservoir and pressure source. The barrier fluid needs to be regularly checked for contamination and replenished as necessary, while the pressure source must be inspected to ensure proper functioning. These additional maintenance tasks can be time-consuming and costly compared to the simpler 53a and 53c seal plans.
- Potential for barrier fluid contamination: The barrier fluid used in Plan 53b seals can become contaminated with process fluid, particularly if the primary seal fails. This contamination can lead to reduced seal performance and increased wear on the seal faces, resulting in more frequent seal replacements and associated downtime.
- Limited gas absorption and cooling capabilities: While Plan 53b seals provide some gas absorption and cooling benefits, they are not as effective as the dedicated features found in 53a and 53c seals. This can be a disadvantage in applications where significant gas entrainment or heat generation is present, as the 53b seal may not be able to adequately address these issues.
When to Use 53b
Plan 53b is recommended for applications where gas absorption into the barrier fluid is a concern, such as in hydrocarbon processing or other gas-handling systems. It is also suitable for dual seal arrangements and processes with moderate to high temperatures and pressures.
What Is Plan 53c
Plan 53c is a mechanical seal support system designed for use with dual unpressurized seals. This plan utilizes a barrier fluid circulated from an external reservoir at a pressure lower than the seal chamber pressure. The barrier fluid serves to lubricate and cool the seal faces while also preventing process fluid from entering the seal chamber.
In a Plan 53c system, the barrier fluid is typically a clean, compatible liquid that is immiscible with the process fluid. The reservoir is maintained at a lower pressure than the seal chamber, allowing the barrier fluid to flow into the seal and then back to the reservoir. This circulation helps to remove heat generated by the seal faces and keeps the seals running at optimal temperatures.
Advantages of 53c
- Enhanced Gas Absorption: Plan 53c incorporates a gas absorber in the seal system, effectively removing dissolved gases from the barrier fluid. This feature significantly reduces the risk of seal failure due to gas accumulation, ensuring more reliable operation compared to Plan 53a and 53b.
- Superior Cooling Capabilities: The Plan 53c seal system includes a dedicated heat exchanger, allowing for efficient cooling of the barrier fluid. This advanced cooling mechanism maintains optimal fluid temperature, extending seal life and minimizing the likelihood of thermal-related failures. In contrast, Plan 53a and 53b lack this integrated cooling feature, making them less suitable for high-temperature applications.
- Improved Particulate Handling: Plan 53c features a cyclone separator, which effectively removes particulates from the barrier fluid. This additional filtration step helps maintain fluid cleanliness, reducing wear on seal faces and prolonging seal life. Both Plan 53a and 53b do not incorporate this advanced particulate removal technique, leaving them more susceptible to contamination-related issues.
- Versatile Pressure Source Options: Unlike Plan 53a, which relies solely on a bladder accumulator, and Plan 53b, which uses a piston accumulator, Plan 53c offers flexibility in pressure source selection. It can accommodate both bladder and piston accumulators, allowing for customization based on specific application requirements and preferences.
- Multiple Seal System Support: Plan 53c is designed to support multiple seal systems, making it a cost-effective solution for applications requiring redundancy or multiple sealing points. This capability reduces the need for separate seal support systems, streamlining installation and maintenance. Plan 53a and 53b, on the other hand, are typically limited to supporting a single seal system.
Disadvantages of 53c
- Higher initial cost: Plan 53c seal systems typically have a higher upfront cost compared to 53a and 53b due to the additional components and complexity involved in their design. The pressure system, barrier fluid reservoir, and cooling system all contribute to the increased cost.
- Increased maintenance requirements: The complexity of 53c seal systems necessitates more frequent maintenance and monitoring to ensure optimal performance. This includes regular checks on the barrier fluid reservoir, pressure source, and cooling system, which can be time-consuming and costly.
- Potential for gas absorption: In some cases, the barrier fluid used in 53c seal systems may absorb process gases, leading to changes in fluid properties and reduced sealing effectiveness. This issue is less common in 53a and 53b systems, which rely on simpler sealing mechanisms.
- Limited compatibility with particulates: While 53c seal systems offer improved sealing performance in many applications, they may be less suitable for processes involving high levels of particulates or abrasive materials. The intricate sealing components can be more susceptible to damage and wear in these environments compared to the simpler designs of 53a and 53b.
- Increased space requirements: The additional components and subsystems present in 53c seal systems, such as the barrier fluid reservoir and cooling system, require more physical space for installation and operation. This can be a disadvantage in applications where space is limited or where compact sealing solutions are preferred.
- Higher energy consumption: The pressure system and cooling system in 53c seal systems consume more energy compared to the passive sealing mechanisms of 53a and 53b. This increased energy consumption can lead to higher operating costs over time, particularly in continuous or high-demand applications.
When to Use 53c
Plan 53c is the preferred choice for high-temperature applications or processes with significant heat generation at the seals. It is also recommended for critical services where maintaining optimal barrier fluid temperature is crucial for seal reliability and longevity.
Differences between Seal Plan 53a, 53b and 53c
Feature | Plan 53a | Plan 53b | Plan 53c |
---|---|---|---|
Pressure Range | Low to moderate | Moderate to high | High |
Barrier Fluid Reservoir | Shared reservoir | Dedicated reservoir per seal | Dedicated reservoir per seal |
Pressure Source | Pressurized nitrogen or air | Bladder accumulator | Piston accumulator |
Gas Absorption | Not typically used | Used to remove dissolved gases | Used to remove dissolved gases |
Cooling | Cooling coils or heat exchanger | Cooling coils or heat exchanger | Cooling coils or heat exchanger |
Particulates | Filters used to remove particulates | Filters used to remove particulates | Filters used to remove particulates |
Number of Seal Systems Supported | Multiple seals can share reservoir | Each seal has dedicated system | Each seal has dedicated system |
Cost | Lowest cost option | Moderate cost | Highest cost option |