Selecting the right materials for mechanical seals can be a daunting task. With so many options available and critical factors to consider, making the wrong choice can lead to premature seal failure, costly downtime, and safety hazards.
In this blog post, we’ll demystify the process of choosing the best materials for your mechanical seals. We’ll cover the commonly used face and secondary seal materials, and discuss the key factors to evaluate, including fluid compatibility, temperature and pressure ratings, mechanical properties, and more.
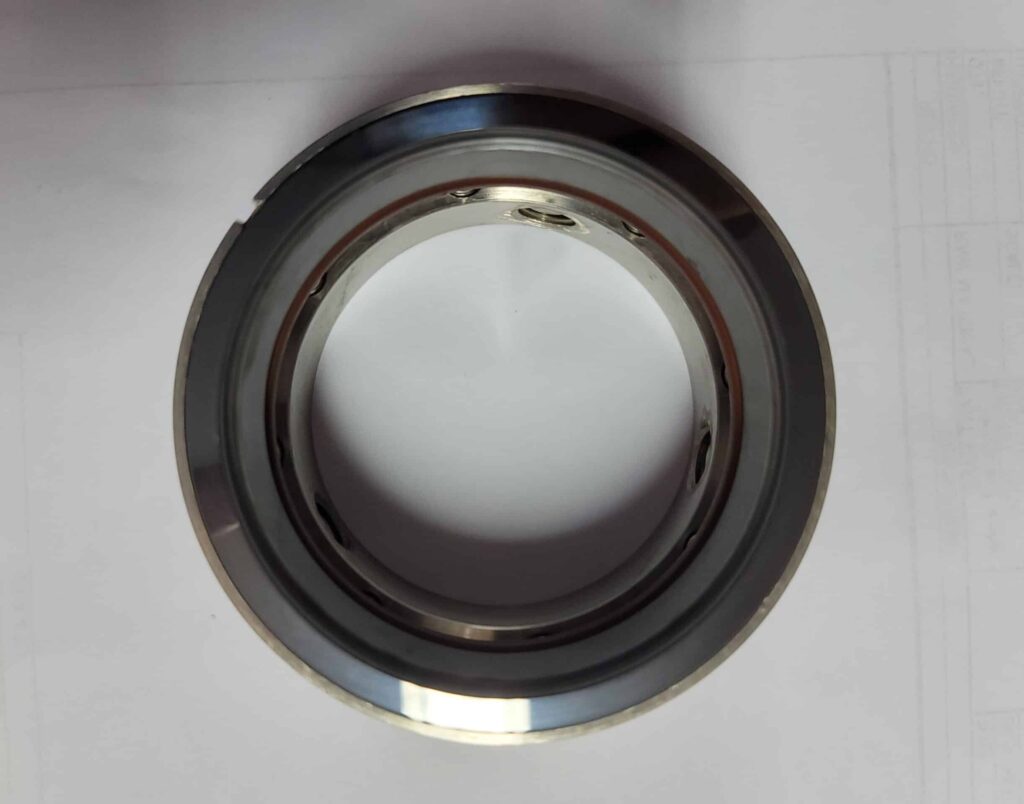
Commonly Used Materials for Mechanical Seals
Seal Face Materials
The seal faces are the heart of a mechanical seal, responsible for maintaining a tight sealing interface despite challenging operating conditions. The following materials are frequently used for seal faces due to their unique properties:
- Carbon: Carbon-graphite is a popular choice for seal faces because of its self-lubricating properties, excellent thermal conductivity, and ability to conform to minor imperfections in the mating face. It is commonly used in water and low-pressure applications but may oxidize at high temperatures or in highly oxidizing environments.
- Silicon Carbide: Silicon carbide is an extremely hard, wear-resistant ceramic material that offers excellent chemical resistance and dimensional stability. It is often used in demanding applications involving high temperatures, pressures, and aggressive media. Silicon carbide can be sintered or reaction-bonded, with the latter offering improved thermal shock resistance.
- Tungsten Carbide: Tungsten carbide is a dense, wear-resistant material with high thermal conductivity. It is frequently used in high-pressure, high-temperature applications and can withstand abrasive media. However, tungsten carbide may be prone to thermal cracking under rapid temperature changes.
- Ceramic: Advanced ceramics, such as alumina and zirconia, offer excellent wear resistance, chemical inertness, and high-temperature stability. They are increasingly used in severe service conditions, such as high-pressure pumps and compressors handling aggressive fluids. However, ceramics can be brittle and susceptible to thermal shock.
- Glass-Filled PTFE: Glass-filled PTFE (polytetrafluoroethylene) is a composite material that combines the low friction and chemical resistance of PTFE with the improved wear resistance and dimensional stability provided by the glass fibers. It is commonly used in low-pressure, chemically aggressive environments where low friction is essential.
Secondary Seal Materials (Elastomers)
Secondary seals, typically O-rings or gaskets, are responsible for static sealing between the seal faces and the housing. They prevent leakage and maintain the integrity of the sealing system. Common elastomeric materials used for secondary seals include:
- Buna (Nitrile): Buna, or nitrile rubber, is a general-purpose elastomer with good resistance to oils, fuels, and hydraulic fluids. It offers a wide operating temperature range and excellent abrasion resistance. However, it is not recommended for use with polar solvents, ketones, or aromatic hydrocarbons.
- EPDM: Ethylene propylene diene monomer (EPDM) is a versatile, cost-effective elastomer with excellent resistance to heat, ozone, and weathering. It is frequently used in applications involving water, steam, and mild chemicals. However, EPDM is not compatible with oils and petroleum-based fluids.
- Viton: Viton, or fluoroelastomer, is a high-performance synthetic rubber with exceptional chemical resistance and high-temperature stability. It is commonly used in aggressive chemical environments and can withstand temperatures up to 200°C (400°F). However, Viton is relatively expensive and may not be suitable for dynamic applications with high friction.
Properties of Different Materials Used for Mechanical Seals
Material | Chemical Resistance | Wear Resistance | Temperature Range (°F) | Thermal Conductivity | Mechanical Strength | Abrasion Resistance | Suitable Applications |
---|---|---|---|---|---|---|---|
Ceramic (Al2O3) | Excellent | Excellent | Up to 1,800 | High | Brittle, susceptible to thermal shock | Excellent | Clean applications, high temperatures |
Carbon | Good resistance to hydrocarbons, solvents, and acids | Moderate | Varies by grade | Moderate | Limited, improved with resin impregnation | Limited | Wide range of process fluids, avoid abrasive fluids or extreme pressure |
Silicon Carbide (SiC) | Exceptional | Excellent | Up to 1,000 | Excellent | High | Excellent | Harsh environments, high-temperature applications |
Tungsten Carbide | Excellent | Excellent | Up to 1,400 | Moderate | High | Excellent | Abrasive and high-pressure applications |
Ni-Resist | Excellent corrosion resistance, moderate wear resistance | Moderate | Up to 1,000 | Good | Moderate | Good | Aggressive chemicals, viscous fluids, low-pressure applications |
GFPTFE | Excellent resistance to acids, alkalis, and solvents | Good | Up to 500 | Low | Limited | Good | Low-pressure applications, clean fluids |
Factors to Consider When Selecting Materials for Mechanical Seals
Fluid Compatibility
The chemical composition, pH level, and potential contaminants in the fluid can have a significant impact on the durability and functionality of the seal materials. For example, a seal material that performs well with water may rapidly degrade when exposed to a hydrocarbon-based fluid. Therefore, it is essential to select materials that can withstand the specific chemical properties of the fluid without experiencing excessive corrosion, swelling, or deterioration.
Temperature Range
Different materials have varying temperature tolerances, and choosing materials that can maintain their properties and performance across the expected temperature spectrum is critical. For high-temperature applications, materials such as tungsten carbide, silicon carbide, and certain engineered ceramics are often preferred due to their excellent heat resistance and thermal stability. Conversely, in low-temperature environments, materials like carbon and certain elastomers may be more suitable.
Pressure Conditions
High-pressure environments require materials with superior mechanical strength and dimensional stability to withstand the increased forces acting on the seal faces. In these cases, harder, more resilient materials like silicon carbide, tungsten carbide, or ceramics are often selected for their ability to maintain a stable, wear-resistant sealing interface under demanding pressure conditions.
Mechanical Strength
The mechanical strength of the seal materials is a key consideration, particularly in applications involving high rotational speeds, frequent start-stop cycles, or exposure to vibrations and shocks. Materials with high hardness, fracture toughness, and flexural strength are better equipped to handle these mechanical stresses without cracking, chipping, or suffering premature wear. The seal faces, in particular, must possess sufficient mechanical strength to maintain a stable, precise sealing interface throughout the seal’s operational life.
Abrasion Resistance
In applications involving abrasive particles or contaminants in the fluid, the abrasion resistance of the seal materials is of utmost importance. Abrasive wear can quickly erode the seal faces, leading to increased leakage and reduced seal life. Materials with high hardness and wear resistance, such as tungsten carbide, silicon carbide, and certain ceramics, are preferred for their ability to withstand the scraping action of abrasive particles. The use of hard face materials in combination with softer, more resilient secondary seals can help to minimize the impact of abrasion on the overall seal performance.
Operating Speed
The rotational speed of the equipment also influences material selection, as high-speed operation can generate significant heat and place increased stress on the seal components. Materials with good heat dissipation properties and resistance to thermal distortion, such as silicon carbide and tungsten carbide, are often chosen for high-speed applications. Additionally, the use of hydrodynamic features on the seal faces, such as grooves or vanes, can help to generate a thin fluid film between the faces, reducing friction and heat generation at high speeds.
Environmental Regulations
Certain materials, such as asbestos and lead, are now restricted or prohibited in many applications due to their potential health and environmental risks. Seal materials must comply with relevant regulations, such as REACH, RoHS, and BSEA, to ensure their suitability for use in specific industries and regions.
Shaft Size
Larger shafts may require more robust seal materials to handle the increased surface area and potential for misalignment or deflection. Additionally, the surface finish and condition of the shaft can influence the selection of compatible seal materials. Rough or damaged shaft surfaces may necessitate the use of harder, more wear-resistant face materials to compensate for the increased abrasion and maintain an effective seal.
Equipment Type
Different equipment types, such as pumps, mixers, or compressors, may have specific requirements for seal materials based on their operating conditions, design features, and industry standards. For example, seals used in food processing equipment must comply with FDA regulations and be suitable for contact with food products, while seals in chemical processing plants may need to resist highly corrosive or aggressive media.
Total Cost of Ownership
While some materials may have a higher initial cost, they can offer significant long-term savings through increased seal life, reduced maintenance requirements, and minimized downtime. The costs associated with seal failures, such as lost production, environmental cleanup, and reputational damage, can far outweigh the upfront material costs. Therefore, it is essential to evaluate the full lifecycle costs and benefits of different material options.