Buffer fluid and barrier fluid are two critical components used in mechanical seals, but many people don’t understand the key differences between them.
Using the wrong type of fluid can lead to seal failure, reduced performance, and costly downtime.
In this post, we’ll break down exactly what buffer fluids and barrier fluids are, highlight their key differences in areas like pressure and application, cover the various types of fluids used, and explain the essential properties to look for when selecting one.
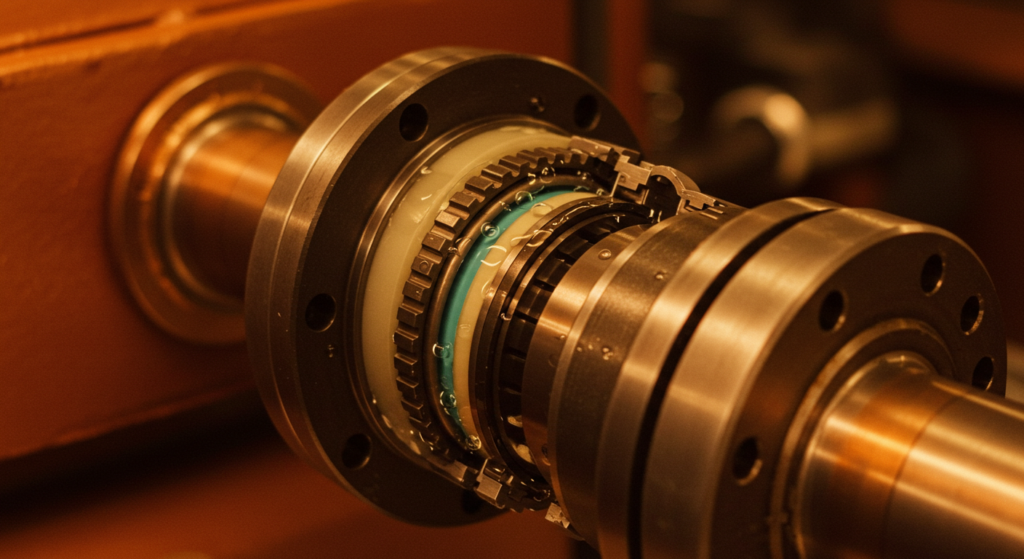
What Is Buffer Fluid
Buffer fluid is a liquid used in dual mechanical seals to provide lubrication and cooling to the sealing surfaces. In a dual seal arrangement, the buffer fluid is maintained at a pressure lower than the process fluid but higher than the atmospheric pressure. This fluid acts as a barrier between the process fluid and the atmosphere, preventing process fluid leakage to the environment.
What Is a Barrier Fluid
Barrier fluids are used in single or double mechanical seals to provide a complete separation between the process fluid and the atmosphere. The barrier fluid is maintained at a pressure higher than the process fluid, creating a positive flow into the seal chamber. This positive pressure ensures that any leakage that occurs will be from the barrier fluid into the process, rather than the process fluid escaping to the environment.
Key Differences Between Buffer Fluids and Barrier Fluids
Pressure
Buffer fluid pressure is typically maintained at a level slightly higher than the seal chamber pressure. This positive pressure differential prevents process fluid from entering the buffer fluid system.
Barrier fluid pressure is kept significantly higher than the seal chamber pressure, often 1.4 to 2.8 bar (20 to 40 psi) above. The high pressure of the barrier fluid provides a physical barrier that completely isolates the process fluid from the atmosphere.
Purpose
Buffer fluids serve to provide lubrication and cooling to the mechanical seal faces, extending seal life and reliability. They also prevent crystallization or coking of the process fluid at the seal faces.
Barrier fluids go a step further by completely isolating the process fluid from the environment. The barrier fluid creates a liquid seal, preventing any contact between the process fluid and atmosphere.
Application
Buffer fluid systems are commonly used in applications where moderate amounts of process fluid leakage across the seal faces can be tolerated. They are suitable for non-hazardous process fluids and in situations where some seal emissions are permissible.
Barrier fluid systems are used in industries such as oil and gas, petrochemical, pharmaceutical, and others dealing with aggressive chemicals often require the use of barrier fluids to ensure maximum safety and regulatory compliance.
Leakage
In a buffer fluid system, a small amount of leakage across the seal faces is expected and managed. The buffer fluid leaking into the process is compensated by a make-up stream from an external reservoir.
Barrier fluid system is designed to eliminate leakage of process fluid to atmosphere. The high pressure of the barrier fluid forces any leakage to occur from the barrier fluid into the process, rather than the other way around. This ensures containment of hazardous fluids.
Types of Buffer and Barrier Fluids
Water
Water is the simplest and most economical option for non-corrosive applications with moderate temperature requirements. It offers good heat transfer properties but may result in seal face corrosion in some cases.
Glycol Solutions
Glycol-based fluids, such as ethylene glycol or propylene glycol mixed with water, provide improved corrosion protection and an extended operating temperature range compared to plain water.
Kerosene and Diesel Fuels
In the hydrocarbon processing industry, light-end hydrocarbons like kerosene or diesel may be used. These offer good compatibility with the process fluid but may pose flammability concerns.
Alcohols
Low molecular weight alcohols such as ethanol or methanol can be employed in low-temperature services. These offer good flammability resistance and heat transfer but may have compatibility issues with certain seal materials.
Petroleum-Based Oils
Mineral oils are commonly used for their excellent lubricity and compatibility with many elastomer seal materials. They are suitable for a wide operating temperature range.
Synthetic Oils
For high-temperature applications or improved oxidative stability, synthetic lubricants like polyalphaolefins (PAO), polyglycols, or perfluoropolyethers (PFPE) are utilized.
Heat Transfer Fluids
In high-temperature services, heat transfer fluids such as aromatic compounds or silicone-based fluids may be necessary to provide efficient cooling and heat dissipation from the seal faces.
Properties of Buffer and Barrier Fluids
- Safety: The fluid should be non-toxic and non-hazardous to minimize risks to personnel and the environment in case of leakage or spillage. It should have a high flash point and auto-ignition temperature.
- Non-flammability: For applications involving flammable process fluids or high temperatures, the buffer/barrier fluid must be non-flammable to prevent fires or explosions. Fluids with high flash points, such as certain synthetic oils, are preferred in these cases.
- Lubricity: The fluid should provide adequate lubrication to the mechanical seal faces to prevent excessive wear, friction, and heat generation.
- Heat Transfer: In some applications, the buffer/barrier fluid serves as a heat transfer medium to dissipate heat away from the seal faces. The fluid should have a high specific heat capacity and thermal conductivity to effectively remove heat and prevent thermal damage to the seals.
- Compatibility: The fluid must be compatible with the mechanical seal materials, the process fluid, and other system components to prevent degradation, corrosion, or adverse chemical reactions.
- Stability: The buffer/barrier fluid should maintain its properties over a wide range of operating temperatures and pressures. It should resist degradation, oxidation, and sludge formation to ensure long-term performance and minimize the need for frequent fluid replacement.
- Low Gas Solubility: In systems handling gases or volatile liquids, the buffer/barrier fluid should have low gas solubility to prevent the formation of bubbles or foam, which can disrupt the sealing interface and cause leakage.
- Specific Gravity: The fluid’s specific gravity should be compatible with the piping system design and the required pressure differential across the mechanical seal. In some cases, a fluid with a higher specific gravity may be needed to provide the necessary pressure head.
- Cost-effectiveness: While meeting the necessary performance requirements, the buffer/barrier fluid should also be cost-effective in terms of initial price, consumption rate, and maintenance costs.
Piping Plans for Buffer and Barrier Fluid Systems
- Plan 52: This plan uses an external reservoir to provide buffer fluid to the seal cavity. The reservoir is maintained at a pressure lower than the process pressure, allowing for leakage to flow back to the reservoir. A cooling coil or heat exchanger may be used to control the fluid temperature.
- Plan 53A: In this plan, a pressurized barrier fluid is supplied to the seal cavity from an external reservoir. The barrier fluid pressure is maintained higher than the process pressure to prevent process fluid from entering the seal cavity. A pumping ring or circulating device is used to circulate the barrier fluid.
- Plan 53B: Similar to Plan 53A, this plan uses a pressurized barrier fluid but with a bladder accumulator instead of an external reservoir. The accumulator maintains the barrier fluid pressure and compensates for thermal expansion or contraction.
- Plan 53C: This plan is a variation of Plan 53A that incorporates a piston accumulator instead of a bladder accumulator. The piston accumulator provides a positive pressure differential and helps maintain a constant barrier fluid pressure.
- Plan 54: This plan uses an external source to provide a pressurized barrier fluid to the seal cavity. The barrier fluid is maintained at a pressure higher than the process pressure and is continuously circulated through the seal cavity using a pumping ring or circulating device. A heat exchanger may be included for temperature control.