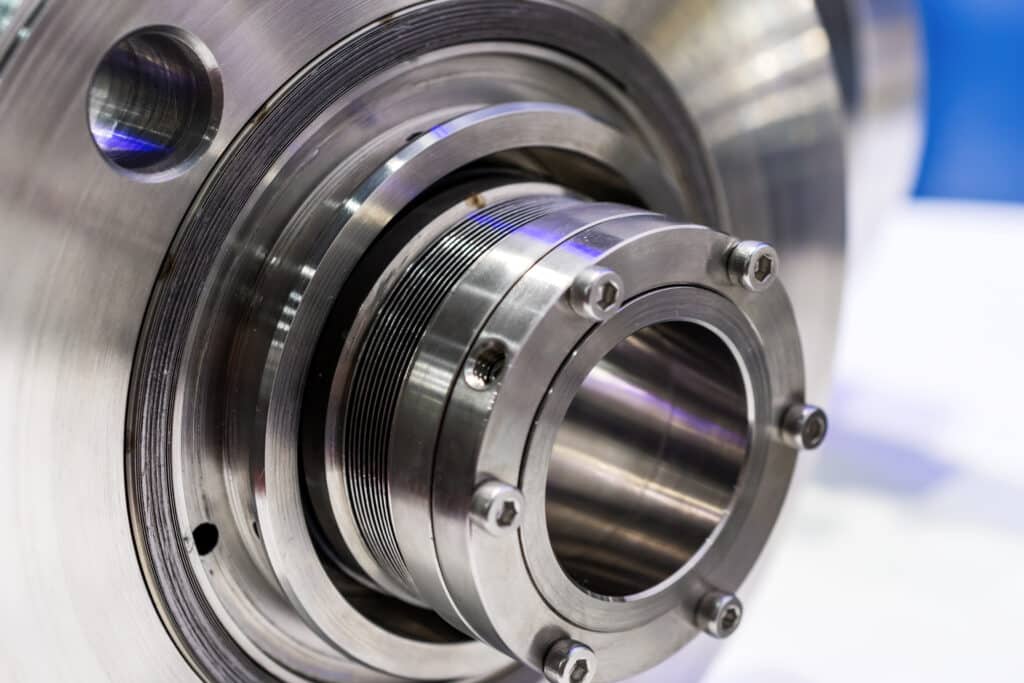
Rillen oder Kerben auf der Dichtungsfläche
Tiefe, konzentrische Rillen oder Kerben auf der Dichtungsfläche sind eines der häufigsten Anzeichen für Schäden an Gleitringdichtungen. Diese Rillen können durch abrasive Partikel im Prozessmedium, Wellenvibrationen oder den Kontakt mit den rotierenden Dichtungskomponenten während des Betriebs verursacht werden. Mit der Zeit beeinträchtigen die Rillen die Integrität der Dichtungsfläche, was zu Undichtigkeiten und vorzeitigen Ausfällen führt.
Ungleichmäßiger Verschleiß der Spur
Ein ungleichmäßiges Verschleißmuster auf der Dichtungsfläche oder dem Dichtungsring kann auf eine Fehlausrichtung hinweisen. Wellendurchbiegungoder Lagerprobleme. Wenn die Verschleißspur auf einer Seite tiefer ist als auf der anderen, deutet dies darauf hin, dass die Dichtung keinen konstanten Kontakt mit der Gegenfläche hat. Dieser ungleichmäßige Verschleiß kann durch unsachgemäße Installation, Wellenvibration oder übermäßige axiale Bewegung der Pumpenwelle verursacht werden.
Gebrochene oder gerissene Dichtungsfläche
Eine gebrochene oder gerissene Dichtungsfläche ist ein ernstes Problem, das sofortiger Aufmerksamkeit bedarf. Thermoschocks, plötzliche Veränderungen der Flüssigkeitstemperatur oder übermäßiger Druck können dazu führen, dass das spröde Dichtungsflächenmaterial reißt oder zersplittert. Dichtungsflächenbrüche können auch durch mechanische Stöße während der Installation oder Inbetriebnahme verursacht werden. Sobald die Dichtungsfläche beschädigt ist, geht die Dichtfunktion verloren, was zu erheblichen Flüssigkeitslecks und möglichen Geräteschäden führen kann.
Absplitterungen, Risse im Dichtring
Ähnlich wie Schäden an der Dichtungsfläche können Absplitterungen oder Risse im Dichtungsring die Dichtungsleistung beeinträchtigen und zu vorzeitigem Versagen führen. Mechanische Stöße, thermische Belastung oder Schmutz in der Prozessflüssigkeit können dazu führen, dass der Dichtungsring absplittert oder reißt. Ein beschädigter Dichtungsring kann keine dichte Abdichtung gegenüber der Dichtungsfläche aufrechterhalten, was zu Flüssigkeitslecks und verringerter Pumpeneffizienz führt.
Quietschendes oder knallendes Geräusch
Ungewöhnliche Geräusche aus dem Dichtungsbereich, wie Quietschen, Quietschen oder Knallen, können auf ein Problem mit dem Gleitringdichtung. Diese Geräusche können durch Trockenlauf, unzureichende Schmierung oder Kontakt zwischen rotierenden und stationären Dichtungskomponenten verursacht werden. Quietschgeräusche können auch durch das Zusammenfallen von Dampfblasen in der Flüssigkeit entstehen, ein Phänomen, das als Kavitation.
Gebrochener oder abgesplitterter Dichtungsring
Ein gerissener oder abgesplitterter Dichtungsring kann die Dichtleistung beeinträchtigen und zu einem vorzeitigen Ausfall führen. Dieser Schaden kann durch mechanische Stöße während der Installation oder des Betriebs, thermische Belastung oder abrasive Partikel in der Prozessflüssigkeit verursacht werden. Ein beschädigter Dichtungsring kann keine dichte Abdichtung gegenüber der Gegendichtfläche aufrechterhalten, was zu Flüssigkeitslecks und einer verringerten Pumpeneffizienz führt.
Ansammlung von Kohlenstaub auf der Außenseite der Dichtung
Eine Ansammlung von feinem Kohlenstaub um die Außenseite der Gleitringdichtung ist ein Zeichen für Dichtungsverschleiß und mögliches Versagen. Da die Kohlenstoffdichtungsflächen während des Betriebs aneinander reiben, nutzen sie sich langsam ab und erzeugen Kohlenstaub. Wenn dieser Staub auf der Außenseite der Dichtungsbrille oder Stopfbuchse sichtbar ist, deutet dies darauf hin, dass die Dichtungsflächen übermäßig verschleißen und die Dichtleistung beeinträchtigt sein kann.
FAQs
Wie lange sollte eine Gleitringdichtung halten?
Im Durchschnitt gut gewartete Gleitringdichtung kann in einer typischen industriellen Anwendung 2–5 Jahre halten, bevor es ausgetauscht werden muss.