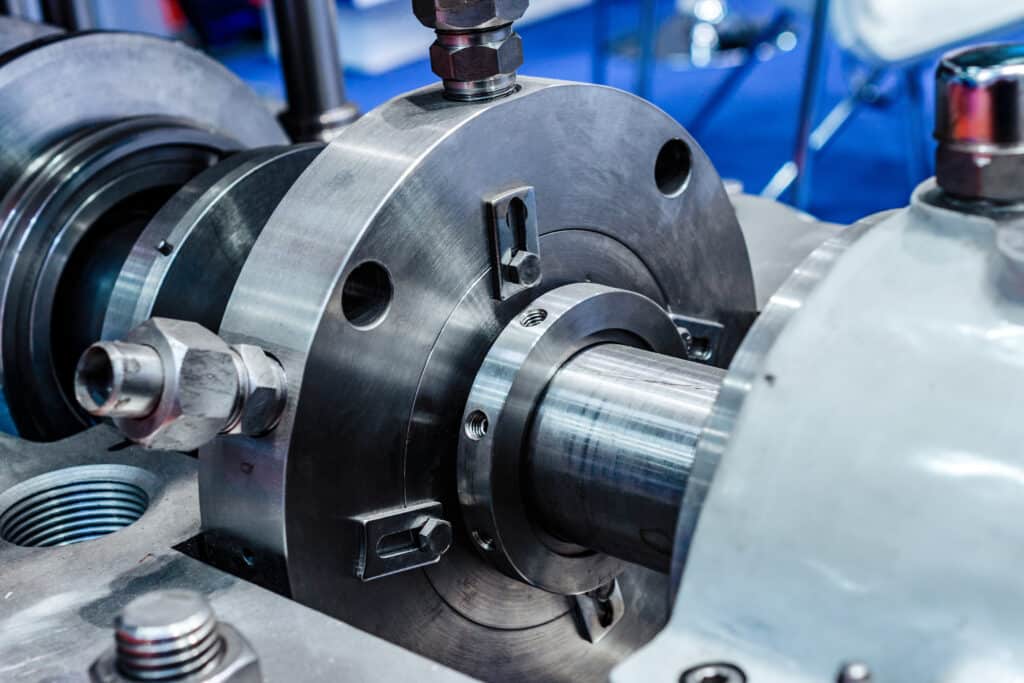
What is Seal Water
Seal water, also known as flush water or barrier fluid, is a clean, cool liquid used to lubricate, cool, and flush the sealing surfaces of mechanical seals in pumps and other rotating equipment. The seal water is typically introduced into the seal chamber through a port or inlet, where it flows around the seal faces and exits through a drain or outlet.
The most common type of seal water is plain, clean water, but other fluids such as glycol, oil, or specially formulated barrier liquids may be used depending on the application and the type of mechanical seal.
Do Mechanical Seals Require Seal Water
The majority of mechanical seals, particularly those used in centrifugal pumps and other rotating equipment handling non-lubricating, abrasive, or corrosive fluids, require some form of seal water or barrier fluid to function properly and achieve acceptable service life.
However, there are some exceptions:
- Dry-running mechanical seals
- Seal-less pumps
Function of Seal Water
- Lubrication: The seal water creates a thin, hydrodynamic film between the stationary and rotating seal faces, reducing friction and wear.
- Cooling: The continuous flow of cool seal water through the seal chamber helps to dissipate the heat generated by friction and the process fluid.
- Flushing: The seal water helps to flush away any debris, contaminants, or precipitates that may accumulate on the seal faces or in the seal chamber.
- Barrier: In double or tandem seal arrangements, the seal water acts as a barrier fluid, preventing the process fluid from reaching the atmosphere or the bearings. The seal water is maintained at a higher pressure than the process fluid, creating a positive flow path that keeps the process fluid contained within the pump.
- Leakage control: The seal water provides a controlled leakage path for any fluid that may pass through the primary seal faces. This leakage is typically collected and drained away, preventing it from entering the bearings or the environment.
Optimizing Seal Water Usage
Monitor Seal Water Pressure and Flow
Insufficient pressure or flow can lead to inadequate seal face lubrication, overheating, and premature wear, while excessive pressure or flow can cause seal face erosion, turbulence, and increased water consumption.
To optimize seal water usage, regularly monitor and adjust the seal water pressure and flow to maintain the manufacturer’s recommended values for each specific seal and application.
Flow Control Valves
Install flow control valves in the seal water supply line to regulate the flow rate and pressure delivered to the seal chamber. These valves can be manual or automatic, with the latter being preferred for more precise control and responsiveness to changing conditions.
Some common types of flow control valves used in seal water systems include:
- Needle valves: These valves provide fine adjustment of flow rate and are suitable for low-flow applications.
- Globe valves: These valves offer good control over a wide range of flow rates and are commonly used in seal water systems.
- Pressure reducing valves (PRVs): These valves automatically maintain a constant output pressure regardless of variations in the input pressure, ensuring a stable seal water supply.
Flow Meters
Incorporate flow meters in the seal water line to accurately measure and monitor the seal water flow rate.
Some common types of flow meters used in seal water systems include:
- Rotameters: These simple, cost-effective devices use a float to indicate the flow rate on a calibrated scale.
- Turbine meters: These meters measure flow rate by counting the rotations of a turbine wheel driven by the seal water flow.
- Magnetic flow meters: These non-invasive meters use electromagnetic principles to measure the flow rate without any moving parts or pressure drop.
Smart Water Control Systems
Implement advanced, automated seal water control systems that continuously monitor and adjust the seal water pressure and flow based on real-time data from sensors and meters. These smart systems can optimize seal water usage by delivering the exact amount of water required for each operating condition, minimizing waste and ensuring consistent seal performance.
Implement a Seal Water Recovery System
In applications where seal water is scarce, expensive, or environmentally sensitive, consider implementing a seal water recovery system to recycle and reuse the flush water. These systems typically involve collecting the used seal water, filtering or treating it to remove contaminants, and returning it to the seal water supply tank for reuse.
Seal Water Pots
For rotating equipment located far from a continuous seal water supply, seal water pots or reservoirs can be used to provide a local source of clean, pressurized flush water. These pots are typically installed near the pump or seal and are filled with a fixed volume of seal water that is circulated through the seal chamber by a small pump or the equipment’s rotating shaft.
Seal water pots can help optimize seal water usage by reducing the length of piping required and minimizing the potential for leaks or pressure losses. They also provide a buffer against supply interruptions and can be easily monitored and maintained to ensure consistent seal water quality.
Water Filtration
Proper filtration of the seal water supply is essential for removing any dirt, debris, or contaminants that could damage the seal faces or clog the flush ports. Filters with a micron rating appropriate for the specific seal and application should be installed in the seal water line and regularly inspected and replaced to maintain optimal flow and cleanliness.
In addition to mechanical filtration, other water treatment methods such as softening, deionization, or reverse osmosis may be necessary for applications with high purity requirements or where the available water supply contains harmful minerals or chemicals.
FAQs
How much water is required for a mechanical seal flush
As a general rule, the seal water flow rate should be sufficient to maintain a minimum pressure differential of 1 bar (15 psi) between the seal water and the process fluid, and to keep the seal faces cool and lubricated.
Typical seal water flow rates range from 0.5 to 2 liters per minute (0.13 to 0.53 gallons per minute) for small to medium-sized seals, and up to 10 liters per minute (2.6 gallons per minute) or more for large, high-pressure seals.
Can you run a mechanical seal dry
In general, most mechanical seals cannot be run dry without causing rapid wear and damage to the seal faces. The seal faces require a thin film of lubrication to prevent direct contact and friction between the stationary and rotating surfaces.
However, there are some specialized mechanical seals that are designed to run dry for short periods or even continuously. These “dry-running” seals typically use advanced face materials such as silicon carbide, tungsten carbide, or diamond-like carbon (DLC) coatings that can withstand high temperatures and friction without lubrication.