Improper split seal installation can lead to premature failure and costly downtime. This common issue plagues many facilities, resulting in reduced equipment lifespan and reliability.
Follow our step-by-step guide on how to properly install a split seal, covering critical aspects like cleaning, positioning, securing, and final checks. Implementing these best practices will ensure optimal seal performance and longevity for your machinery.
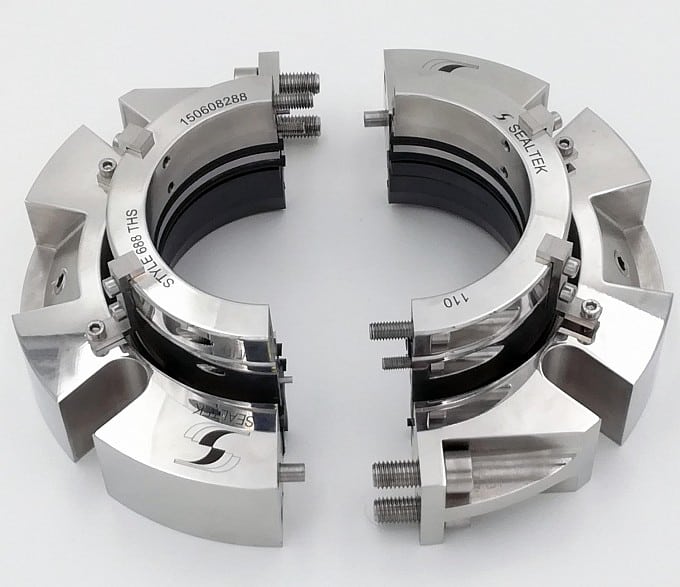
Step 1: Clean the surfaces
Before installing a split seal, it’s essential to clean all mating surfaces thoroughly. Remove any dirt, debris, oil residue or corrosion from the shaft, housing bore, and gland plate using an appropriate solvent and clean cloth.
Step 2: Positioning the Seal
Place the seal in the proper orientation based on the direction of shaft rotation and the location of the pressurized fluid. Split seals are designed for a specific rotational direction.
Carefully open the seal and place it around the shaft without pinching or damaging the sealing elements. The two halves of the split seal are typically held together by an O-ring or clips.
Step 3: Seating the Seal
Gently slide the seal into the housing bore until it bottoms out and is seated squarely. Make sure the split line is aligned properly, usually at the 12 o’clock position, and that the seal halves mate flush with no gaps or steps. The seal faces should be perpendicular to the shaft centerline.
If the seal utilizes setting or centering clips, install those at this point per the manufacturer’s instructions. These help maintain the seal’s position during assembly.
Step 4: Add lubricant
For seal designs that incorporate O-rings, apply a thin coat of appropriate lubricant to the O-rings before final assembly. Use only lubricants compatible with the O-ring material and the process fluid.
Also apply a thin film of lubricant to the shaft surface where the seal will contact it. This allows the sealing elements to slide smoothly into place without catching or tearing on the shaft.
Step 5: Securing the Seal
Set the operating height of the seal
The operating height or working length of the seal must be set to maintain proper contact between the seal faces. This is typically done by compressing the seal between the housing bore and gland plate to a specific dimension provided by the manufacturer. Use gauges or a depth micrometer to achieve the correct compression.
Check the position of the rotor assembly on the shaft
Verify that the seal rotor is positioned correctly on the shaft. It should be located per the manufacturer’s dimensional specifications relative to a reference point, often the face of the seal chamber or bearing housing. This ensures optimal contact and wear-in of the seal faces.
Install the primary ring
For split seals with a separate primary ring that houses the spring and rotating face, install this over the shaft and into the gland plate, engaging any pins or anti-rotation lugs. The primary ring should slide freely on the shaft without binding.
Install the cover plate or gland
Position the cover plate or gland over the primary ring and bolt it to the seal chamber face. Make sure the gland is oriented correctly, with any flush ports or quench/drain connections facing the proper direction. Center the gland on the shaft to prevent contact with rotating parts.
Tighten the fasteners
Snug up the gland bolts gradually, alternating from one side to the other to draw the gland up evenly. This prevents cocking and binding of the seal. Torque the bolts to the manufacturer’s recommended value using a calibrated wrench. Do not overtighten, as this can distort the seal faces and cause leakage.
Step 6: Final Checks
After installation, a few final checks will help ensure the split seal is ready for operation:
Ensure proper fluid levels
Make sure the pump is properly filled with the process fluid and that it is circulating through the seal chamber. The fluid cools and lubricates the seal faces. Check that the fluid is at the proper level in the seal chamber and that there are no air pockets.
Check for free rotation
Slowly rotate the shaft by hand to verify that the seal allows smooth rotation without binding or excessive resistance. Listen for any rubbing or scraping sounds that could indicate contact of the seal faces or improper installation.
Check for leaks
Start up the equipment and run it at normal operating conditions while monitoring the seal for any signs of leakage. Visually inspect the drain line and the atmosphere-side of the seal for any fluid collecting, dripping or spraying. Also check for excessive heat, noise or vibration from the seal area during operation.