Welded metal bellows seals are a critical component in various industrial applications, offering reliable sealing solutions in demanding environments.
This blog post will provide a comprehensive guide on the key factors to consider when choosing welded metal bellows seals, enabling you to make an informed decision tailored to your unique requirements.
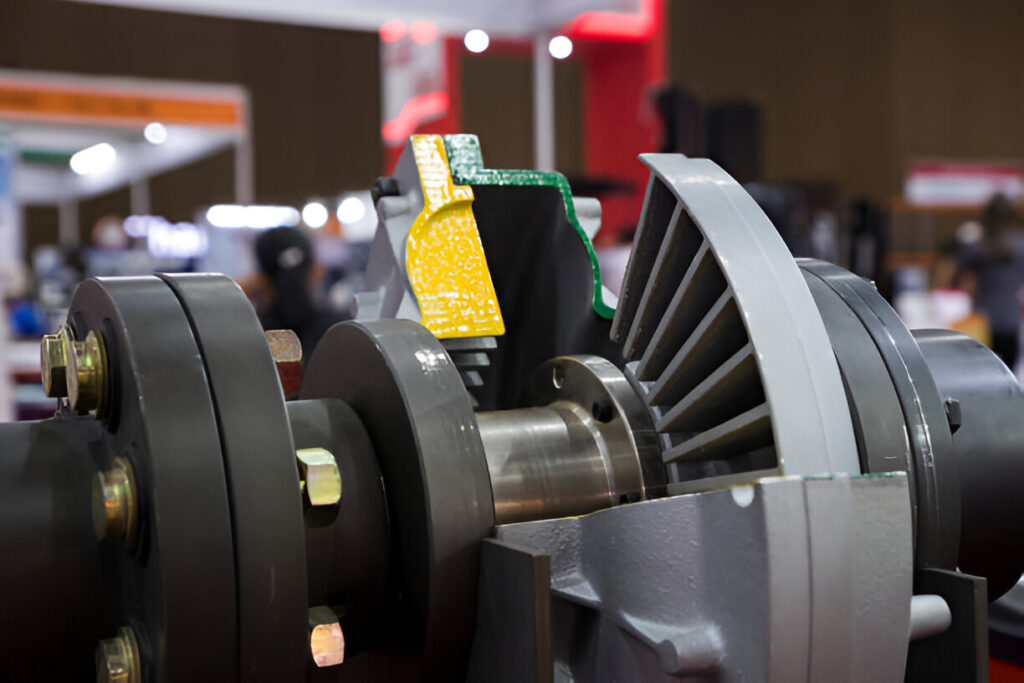
Types of Welded Metal Bellows Seals
Flat Welded Metal Bellows Seals
Flat welded metal bellows seals consist of a series of thin, flat metal discs welded together at their inner and outer edges. This design creates a flexible, accordion-like structure that allows for axial movement while maintaining a secure seal. Flat welded metal bellows seals are commonly used in applications with limited space, as their compact design enables them to fit into tight spaces where other types of seals may not be suitable.
Formed Welded Metal Bellows Seals
Formed welded metal bellows seals feature a series of metal discs that are shaped into a convex or concave profile before being welded together. This design provides greater flexibility and allows for more significant axial movement compared to flat welded metal bellows seals. Formed welded metal bellows seals are ideal for applications that require a higher degree of movement or where greater flexibility is needed to accommodate misalignment or vibration.
Nested Ripple Welded Metal Bellows Seals
Nested ripple welded metal bellows seals are a specialized type of formed welded metal bellows seal. They feature a series of shaped metal discs with alternating convex and concave profiles, which are nested together and welded at their edges. This unique design allows for even greater flexibility and axial movement compared to standard formed welded metal bellows seals. Nested ripple welded metal bellows seals are well-suited for applications with extreme temperature fluctuations, high pressure, or significant misalignment.
Edge-Welded Metal Bellows Seals
Edge-welded metal bellows seals are created by welding together a series of metal discs at their outer edges only, leaving the inner edges free. This design allows for greater radial movement and flexibility compared to other types of welded metal bellows seals. Edge-welded metal bellows seals are commonly used in applications where radial movement is required, such as in rotating shafts or in situations where the seal must accommodate lateral misalignment.
How to Select the Right Welded Metal Bellows Seals
Plate Shape
Common plate shapes include flat, single convolution, and multi-convolution designs.
- Flat plates offer simplicity but may have limited flexibility.
- Single convolution plates provide improved flexibility and sealing capabilities in low-pressure environments.
- Multi-convolution plates, with their multiple waves or ripples, deliver superior flexibility and are ideal for applications with high axial, angular, or lateral movement.
Material Selection
Some common materials include:
- Stainless steel (304, 316, 321): Offers excellent corrosion resistance and strength for general-purpose applications.
- Inconel (625, 718): Provides superior high-temperature strength and corrosion resistance in aggressive environments.
- Hastelloy (C-22, C-276): Delivers outstanding corrosion resistance in highly corrosive media, such as acids and chlorides.
- Titanium (Grade 2, Grade 5): Combines high strength-to-weight ratio and exceptional corrosion resistance, ideal for aerospace and marine applications.
Welding Integrity
Welding integrity is paramount for the reliability and performance of welded metal bellows seals. High-quality welds ensure a strong, leak-tight seal that can withstand the demands of the application. Techniques such as tungsten inert gas (TIG) welding or laser welding are commonly employed to achieve precise, consistent welds. Proper weld penetration, minimal porosity, and the absence of defects are key indicators of welding integrity. Conducting non-destructive testing, such as radiographic or ultrasonic inspections, can verify the quality of the welds and ensure the seal’s integrity.
Thickness
Thinner plates offer increased flexibility but may have limited pressure handling capabilities. Thicker plates provide greater strength and pressure resistance but may reduce flexibility. Typical thickness ranges from 0.1 mm to 0.5 mm.
Pressure Ratings and Seal Balance
Pressure ratings indicate the maximum allowable working pressure (MAWP) the seal can withstand without failure. It is essential to choose a seal with a pressure rating that safely exceeds the maximum expected system pressure.
Seal balance refers to the ratio of the effective area of the bellows exposed to the process fluid compared to the effective area exposed to the atmospheric side. Properly balanced seals minimize the net force acting on the bellows, reducing stress and extending seal life. The three main types of seal balance are:
- Unbalanced: The entire effective area of the bellows is exposed to the process fluid, resulting in higher stress on the seal.
- Balanced: The effective areas exposed to the process fluid and atmospheric side are equal, minimizing the net force on the bellows.
- Pressure-balanced: An additional piston or diaphragm is used to further reduce the net force on the bellows, enhancing seal performance in high-pressure applications.