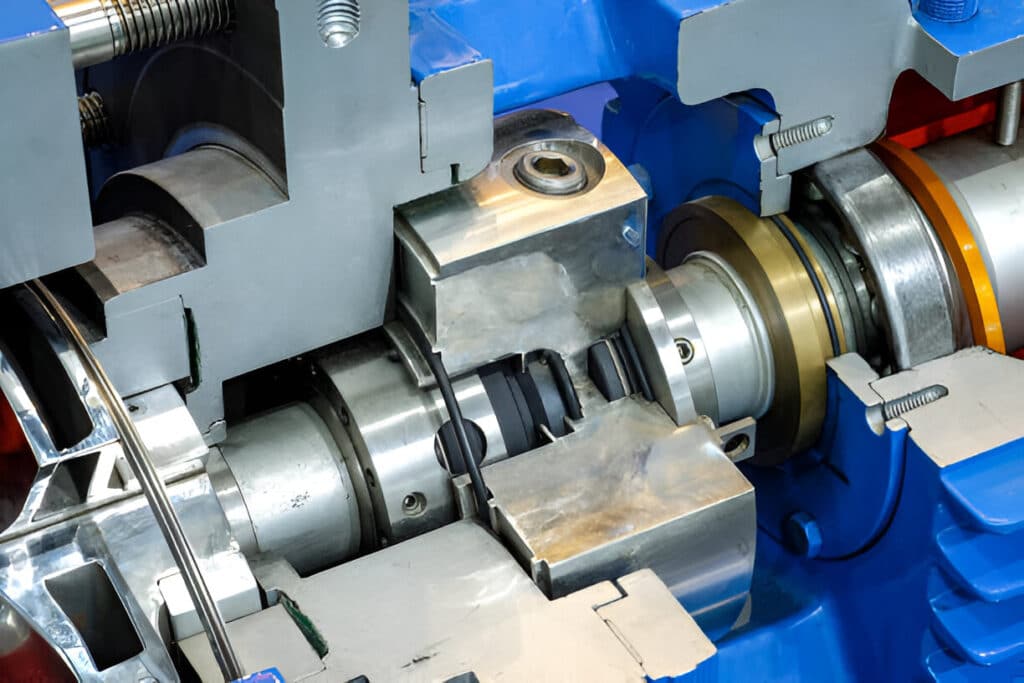
What Is Pusher Mechanical Seal
A pusher mechanical seal is a type of seal that uses a spring element to maintain seal face contact and prevent fluid leakage. The spring element, often a single coil spring or multiple springs, pushes the primary sealing elements together to create a seal between the stationary and rotating parts of the seal. This design is commonly used in centrifugal pumps and other rotating equipment.
How Does Pusher Mechanical Seal Work
In operation, the spring element pushes the rotating seal ring against the stationary seal ring, creating a tight seal between the two faces. This prevents fluid leakage from the pump shaft while allowing for shaft rotation. The secondary sealing elements provide additional sealing between the stationary and rotating components of the seal assembly.
One key characteristic of pusher seals is that the secondary sealing elements move axially with the rotating seal face as it wears down over time. This maintains a constant sealing force between the faces, compensating for wear. However, this axial movement also results in a limited pressure range and higher potential for leakage compared to non-pusher designs.
Advantages of Pusher Mechanical Seal
- Versatility: Pusher seals can be used in a wide range of applications, including centrifugal pumps, mixers, and other rotating equipment.
- Simple design: The straightforward design of pusher seals makes them easy to install, maintain, and replace.
- Cost-effective: Due to their simple construction, pusher seals are generally more affordable than non-pusher seals.
- Wide range of materials: Pusher seals can be manufactured using various materials, such as carbon, ceramic, and tungsten carbide, to suit different application requirements.
Disadvantages of Pusher Mechanical Seal
- Limited pressure and speed capabilities: Pusher seals are not suitable for high-pressure or high-speed applications due to their design limitations.
- Increased wear: The constant contact between the sealing faces in pusher seals can lead to faster wear, reducing seal life.
- Sensitivity to misalignment: Pusher seals are more sensitive to shaft misalignment, which can cause premature seal failure.
- Higher leakage rates: Compared to non-pusher seals, pusher seals typically have higher leakage rates due to their design.
What Is Non-pusher Mechanical Seal
Non-pusher mechanical seals, also known as bellows seals or cartridge seals, use a flexible bellows element to maintain contact between the sealing faces. The bellows, made of metal or elastomeric materials, acts as both the secondary sealing element and the spring mechanism. This design eliminates the need for additional springs, resulting in a more compact and leak-tight seal.
How Does Non-pusher Mechanical Seal Work
In operation, the bellows compress and expand to maintain a constant closing force on the seal faces, ensuring proper sealing even under varying pressure and temperature conditions. The absence of sliding components, such as pusher sleeves and O-rings, minimizes wear and extends seal life.
Advantages of Non-pusher Mechanical Seal
- Improved seal performance: Non-pusher seals provide better sealing performance, with lower leakage rates compared to pusher seals.
- Higher pressure and speed capabilities: The design of non-pusher seals allows them to operate at higher pressures and speeds than pusher seals.
- Reduced wear: The absence of additional springs in non-pusher seals results in less wear on the sealing faces, extending seal life.
- Increased tolerance to misalignment: Non-pusher seals are more forgiving of shaft misalignment, reducing the risk of premature seal failure.
Disadvantages of Non-pusher Mechanical Seal
- Higher cost: Due to their more complex design and advanced materials, non-pusher seals are generally more expensive than pusher seals.
- Limited sizes: Non-pusher seals are available in a narrower range of sizes compared to pusher seals.
- Reduced versatility: Non-pusher seals may not be suitable for all applications, particularly those with high levels of particulates or abrasive media.
- More complex installation: The installation of non-pusher seals can be more challenging due to their cartridge design and precise alignment requirements.
When to Use Pusher Mechanical Seal
- General-purpose centrifugal pumps handling non-hazardous, low-pressure fluids
- Equipment with larger shaft diameters and wider seal chamber gaps
- Applications where cost is a primary concern
- Situations where frequent seal replacement is expected or maintenance resources are limited
When to Use Non-pusher Mechanical Seal
- High-pressure, high-speed applications, such as boiler feed pumps or compressors
- Hazardous or toxic fluid services that require minimal leakage
- Equipment with limited seal chamber space or tight clearances
- Applications where extended seal life and reduced maintenance are priorities