In the machinery industry, seal failure can lead to costly downtime, safety hazards, and environmental contamination. Without proper support, seals are prone to leaking, overheating, and rapid wear.
Seal failures not only disrupt production, but can also result in product loss, equipment damage, and noncompliance with regulations. The consequences can be severe, from lost profits to reputational harm.
Seal support systems are the key to preventing these issues. By providing lubrication, controlling pressure and temperature, flushing contaminants, and containing leaks, seal support systems ensure reliable, long-lasting seal performance across a wide range of industrial applications.
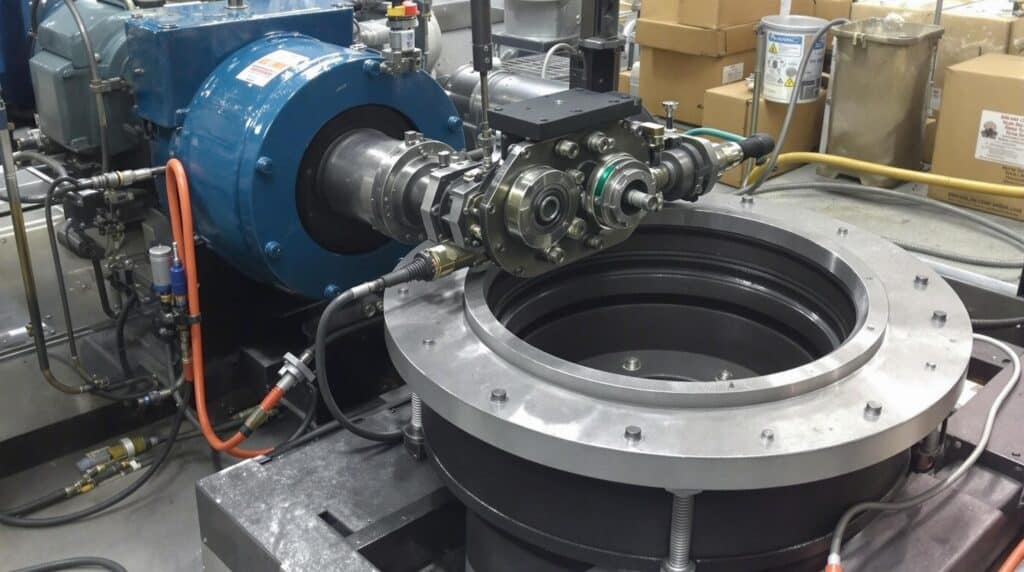
What is a Seal Support System
A seal support system is an auxiliary system designed to optimize the performance and longevity of mechanical seals in rotating equipment such as pumps, compressors, and mixers. The primary purpose of a seal support system is to provide a controlled environment for the mechanical seal to operate effectively, thereby minimizing seal failure and enhancing overall system reliability.
Seal support systems achieve this by regulating the conditions in the seal chamber, which is the space between the inboard and outboard sides of the mechanical seal. By carefully controlling factors such as pressure, temperature, and fluid properties within this chamber, seal support systems ensure that the mechanical seal operates within its designed parameters.
Purpose and Functions of Seal Support Systems
- Lubrication of seal faces: It supplies a clean, cool, and compatible lubricating fluid (such as oil, glycol, or water) to the interface between the stationary and rotating seal faces.
- Pressure and temperature control: They can be designed to regulate the pressure in the seal chamber to be slightly higher than the process fluid pressure, preventing the ingress of process fluid and contaminants into the sealing area. Temperature control is achieved by circulating a cooling medium or using heat exchangers to dissipate excess heat generated by the sealing process.
- Flushing and removal of contaminants: The flushing action is typically achieved by circulating a clean fluid through the seal chamber, which carries away any accumulated debris, dissolved solids, or crystallized particles.
- Containment of process fluids: Seal support systems act as a barrier between the process fluid and the environment, providing a secondary containment mechanism in addition to the mechanical seal itself. The seal support system collects and contains any minor leakage that may occur, preventing it from escaping into the surroundings.
- Monitoring and safeguarding: Advanced seal support systems often incorporate monitoring and safeguarding features to detect and respond to abnormal conditions. These can include pressure, temperature, and level sensors that continuously monitor the seal support fluid and the seal chamber.
Types of Seal Support Systems
Process Side Support Systems
Process side support systems are located on the side of the seal closest to the process fluid. Their primary function is to control the environment immediately around the inboard seal faces. This is accomplished by circulating a barrier fluid at a pressure slightly higher than the process fluid, which prevents process fluid from entering the seal chamber. The barrier fluid also helps lubricate and cool the seal faces.
Common process side support systems include:
- API Plan 53A – Provides a pressurized external barrier fluid reservoir
- API Plan 54 – Uses an external pumping device to circulate barrier fluid
- API Plan 55 – Utilizes a bladder accumulator to provide pressurized barrier fluid
Dual or In-Between Support Systems
Dual seal support systems are used with double seals and are located between the inboard and outboard seal faces. They maintain a barrier fluid at a pressure lower than the process fluid but higher than atmospheric pressure. This creates a controlled environment that prevents process fluid from leaking to atmosphere while also keeping the seal faces lubricated and cooled.
Examples of dual support systems include:
- API Plan 52 – Unpressurized buffer fluid reservoir with or without circulation
- API Plan 53B – Pressurized barrier fluid reservoir with circulation
- API Plan 54 – Pressurized external barrier fluid pumping device
Atmospheric Side Support Systems
Atmospheric side support systems are located on the side of the seal exposed to the atmosphere. They are designed to collect and control any leakage that may occur past the outboard seal faces. These systems often incorporate a reservoir to contain the leakage and may include provisions for monitoring leakage rates.
Atmospheric side support systems include:
- API Plan 65A – Collects and controls seal leakage with a drain connection
- API Plan 75 – Captures leakage and routes it to a vapor recovery system
- API Plan 76 – Returns collected leakage back to the process stream
Applications of Seal Support Systems
- Oil and Gas: In both upstream and downstream oil and gas operations, seal support systems are used on pumps, compressors, and other rotating equipment to prevent hydrocarbon leakage and comply with strict emissions regulations.
- Chemical Processing: Chemical plants rely on seal support systems to contain hazardous and corrosive fluids, protect against atmospheric contamination, and ensure worker safety.
- Pharmaceuticals: In the pharmaceutical industry, seal support systems prevent contamination of the process fluid, minimize the risk of leakage, and enable compliance with stringent FDA regulations.
- Food and Beverage: Seal support systems in food and beverage applications must meet strict hygiene standards to prevent product contamination. The support systems help maintain the integrity of the seals, even with frequent temperature and pressure changes during cleaning cycles.
- Mining: In mining operations, seal support systems are exposed to abrasive slurries, high vibration, and extreme temperatures. API Plan 54 and 65A systems are commonly used to flush away abrasive particles and contain any leakage.
- Wastewater Treatment: Seal support systems in wastewater treatment plants help prevent the escape of noxious gases and contaminated water into the environment. Dual pressurized systems (API Plan 53B) are often used to provide a positive barrier against process fluid leakage.
- Pulp and Paper Processing: In pulp and paper mills, seal support systems must handle abrasive pulp slurries, corrosive chemicals, and high temperatures. API Plan 65A and 75 systems are frequently used to collect and dispose of any seal leakage.
- Refrigeration Compression: Seal support systems in refrigeration compressors prevent the leakage of refrigerants, which can be harmful to the environment and pose safety risks. API Plan 76 systems are often used to return any refrigerant leakage back to the compressor suction.