In the realm of mechanical seals, elastomers are polymeric materials that exhibit elastic properties. These versatile materials are employed in various seal components, such as O-rings, bellows, and secondary seals, to provide effective sealing and prevent fluid leakage.
Elastomers possess unique characteristics, including flexibility, resilience, and resistance to chemicals and extreme temperatures, making them indispensable in demanding industrial applications. The selection of the appropriate elastomer for a specific mechanical seal depends on factors such as the fluid being sealed, operating temperature, pressure, and chemical compatibility.
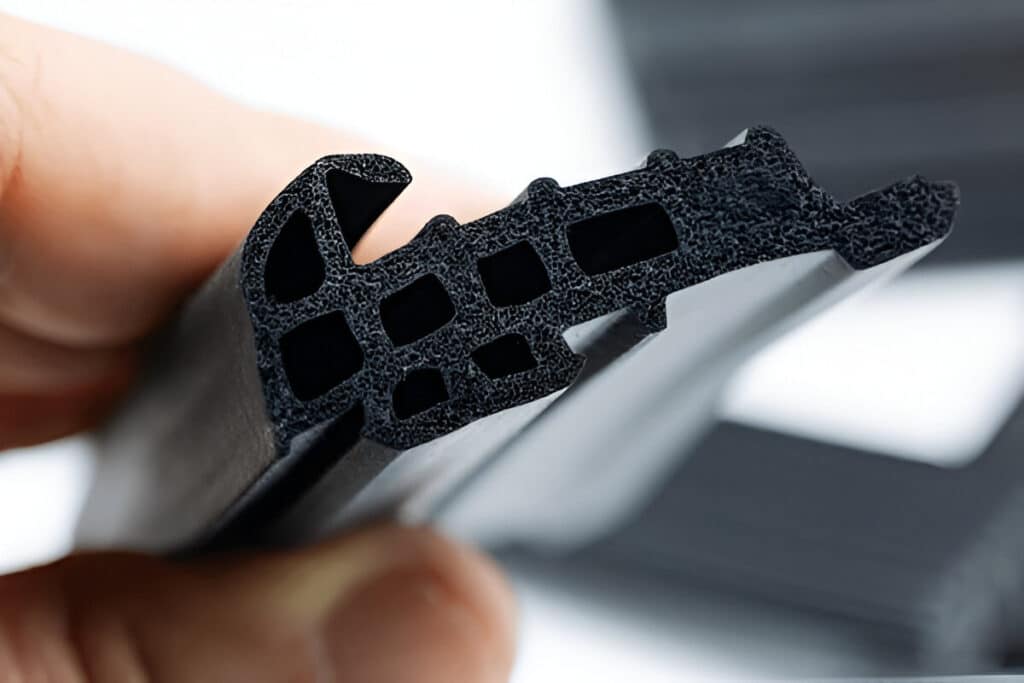
What is Elastomer in Mechanical Seal
An elastomer is a crucial component in mechanical seals, providing sealing and flexibility in a wide range of applications. Elastomers are polymeric materials that exhibit elastic properties, allowing them to deform under stress and return to their original shape when the stress is removed. In mechanical seal designs, elastomers are commonly used as secondary seals, such as O-rings, gaskets, and bellows, to prevent leakage and accommodate shaft movement.
One common application of elastomers in mechanical seals is the elastomer bellows seal. This type of seal consists of an elastomeric bellows that acts as both the secondary seal and the spring element, providing axial flexibility and maintaining a constant sealing force. Elastomer bellows seals are compact, easy to install, and can operate independently of the direction of rotation, making them versatile for various pump types and sizes.
Characteristics of Elastomers
- Elasticity and Flexibility: Elastomers possess the ability to deform under stress and return to their original shape once the stress is removed. This elasticity allows elastomer bellows and other seal components to accommodate shaft movement, misalignment, and vibration without compromising the sealing function.
- Durometer Hardness: The durometer hardness of an elastomer refers to its resistance to indentation and is a measure of its firmness. Softer elastomers provide better sealing against irregular surfaces, while harder elastomers offer improved abrasion resistance and are suitable for higher-pressure applications.
- Compression Set Resistance: Compression set resistance is the ability of an elastomer to maintain its sealing force and return to its original shape after being subjected to prolonged compression. Elastomers with high compression set resistance minimize the risk of seal failure due to permanent deformation, ensuring consistent sealing performance over extended periods.
- Tensile Strength: Tensile strength refers to the maximum stress an elastomer can withstand before breaking. Elastomers used in mechanical seals must have sufficient tensile strength to resist the forces generated by the sealed fluid pressure and the spring load of the seal assembly.
- Elongation at Break: Elongation at break is the maximum elongation an elastomer can undergo before rupturing. Elastomers with high elongation at break can accommodate significant deformation without failure, providing a safety margin in case of unexpected stress or movement.
- Chemical Resistance: Elastomers used in mechanical seals must resist degradation when exposed to the sealed fluid and the surrounding environment.
- Temperature Resistance: The operating temperature range is another critical factor in selecting the appropriate elastomer for a mechanical seal. Elastomers must maintain their properties and sealing performance across the expected temperature range of the application.
Types of Elastomers Used in Mechanical Seals
Nitrile (NBR)
Nitrile, also known as Buna-N, is a popular elastomer choice for mechanical seals due to its excellent resistance to oils, fuels, and other hydrocarbon-based fluids. It offers good abrasion resistance and can withstand temperatures ranging from -30°C to 110°C. NBR is commonly used in applications involving petroleum products, such as automotive fluids and lubricants.
Fluoroelastomer (FKM)
Fluoroelastomers, often referred to as Viton®, exhibit exceptional chemical resistance and can withstand high temperatures up to 200°C. They are resistant to a wide range of aggressive chemicals, including acids, bases, and solvents. FKM is an ideal choice for mechanical seals in chemical processing, pharmaceutical, and oil and gas industries.
Silicone (VMQ)
Silicone elastomers are known for their excellent thermal stability and flexibility over a wide temperature range, from -60°C to 230°C. They offer good resistance to ozone, UV radiation, and weathering. However, silicone has limited resistance to oils and solvents. It is often used in food and beverage, medical, and pharmaceutical applications.
Ethylene Propylene Diene Monomer (EPDM)
EPDM is a versatile elastomer with excellent resistance to heat, ozone, and weathering. It can withstand temperatures from -50°C to 150°C and is compatible with a variety of fluids, including water, steam, and mild chemicals. EPDM is commonly used in automotive, HVAC, and industrial applications.
Perfluoroelastomer (FFKM)
Perfluoroelastomers, such as Kalrez® and Chemraz®, are the most chemically resistant elastomers available. They can withstand extreme temperatures up to 327°C and are compatible with virtually all chemicals, including highly aggressive acids, bases, and solvents. FFKM is used in critical applications where seal failure can have severe consequences, such as in semiconductor manufacturing and chemical processing.
Hydrolysis-resistant polyurethane (HPU)
HPU elastomers are specifically designed to resist hydrolysis, which is the degradation of the elastomer due to exposure to water and high temperatures. They offer excellent abrasion resistance and can withstand temperatures up to 120°C. HPU is commonly used in mechanical seals for pumps handling water, wastewater, and other aqueous solutions.
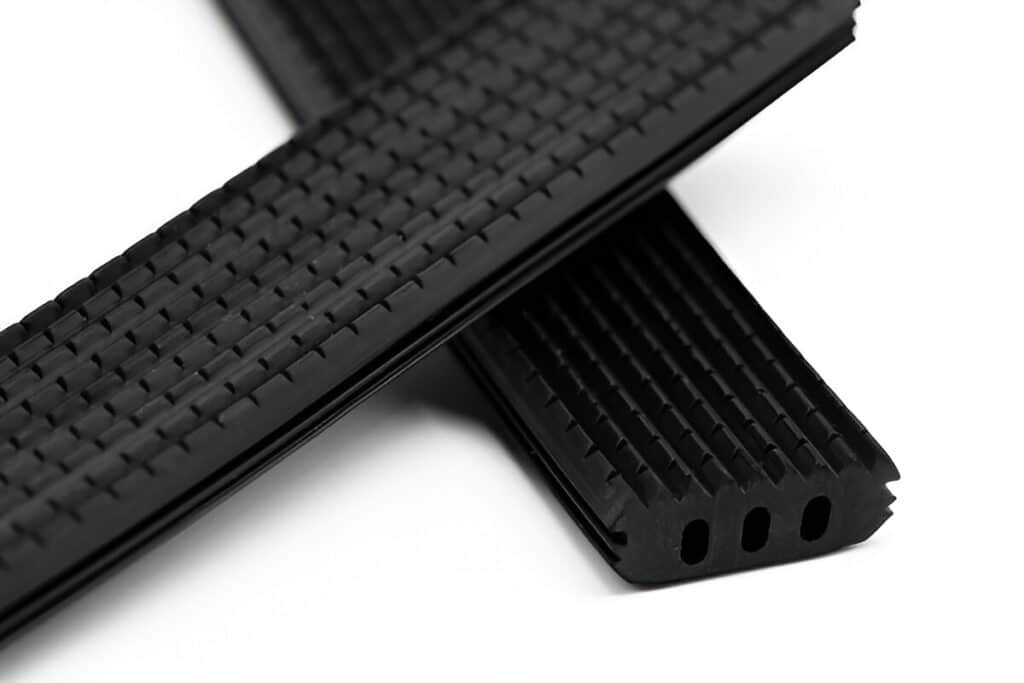
Advantages of Elastomers
Excellent Sealing Performance
Elastomers used in mechanical seals provide excellent sealing performance across a wide range of applications. Their elasticity and flexibility allow them to conform closely to the surfaces they are sealing, creating a tight barrier that prevents leakage. This is especially important in dynamic applications such as centrifugal pumps, where the seal must accommodate shaft movement while maintaining a reliable seal.
Chemical Compatibility
Another key advantage of elastomers in sealing applications is their chemical resistance. Different elastomer compounds are formulated to withstand exposure to various chemicals, solvents, oils, and other fluids. For example, fluoroelastomers (FKM) exhibit excellent resistance to many aggressive chemicals, fuels, and oils, making them suitable for use in demanding industrial environments. Similarly, EPDM elastomers have good resistance to water, steam, and many polar solvents.
Temperature Resistance
Elastomers used in mechanical seals are also capable of operating across a broad temperature range. Different elastomer compounds have varying temperature capabilities, with some able to handle extreme high or low temperatures. Fluoroelastomers, for instance, can withstand temperatures up to 200°C or higher, while silicone elastomers maintain their properties at temperatures as low as -60°C.
Abrasion and Wear Resistance
In applications involving abrasive media or particulates, elastomers provide good abrasion and wear resistance compared to other sealing materials. The resilient nature of elastomers allows them to absorb impact from abrasive particles without permanent damage. Some elastomer compounds, such as hydrolysis-resistant polyurethane (HPU), are specifically formulated for enhanced abrasion resistance.
Vibration and Shock Absorption
The inherent damping properties of elastomers make them excellent at absorbing vibration and shock loads in mechanical systems. In applications with high vibration or sudden impact forces, elastomeric components in mechanical seals help protect the sealing surfaces and other critical components from damage. The elastomer acts as a buffer, dissipating energy and reducing the transmission of vibration to the seal faces.
Cost-effectiveness
Elastomers are generally more cost-effective than other specialized sealing materials. The raw materials and manufacturing processes for elastomers are typically less expensive compared to exotic alloys or advanced ceramics. Additionally, the versatility of elastomers allows them to be used in a wide range of mechanical seal designs and applications, reducing the need for costly custom solutions.
Factors Affecting Elastomer Performance
Operating Temperature
Elastomers have specific temperature limits beyond which their mechanical properties deteriorate. For example, nitrile (NBR) is suitable for temperatures from -30°C to 110°C, while fluoroelastomers (FKM) can withstand -20°C to 200°C. Exceeding the recommended temperature range can cause the elastomer to harden, soften, or degrade, compromising the seal’s performance and service life.
Chemical Compatibility
The elastomer must withstand the chemical environment without excessive swelling, shrinking, or degradation. Different elastomers offer resistance to various chemicals:
- Nitrile (NBR): Resistant to mineral oils, greases, and some fuels
- Fluoroelastomer (FKM): Excellent resistance to aggressive chemicals, oils, and solvents
- EPDM: Good resistance to ketones, alcohols, and brake fluids, but poor resistance to oils
- FFKM: Superior chemical resistance, withstanding a wide range of harsh chemicals
Incompatibility between the elastomer and the medium can lead to seal failure and leakage.
Pressure
High pressures can cause excessive compression set, reducing the elastomer’s ability to maintain a proper seal. The pressure limit depends on the elastomer type and seal design. For instance, a rubber bellows seal with a compact design can handle higher pressures compared to a standard O-ring.
Abrasion and Wear
In applications involving abrasive particles or media, the elastomer must exhibit good abrasion resistance to prevent premature wear. Harder elastomers, such as FKM or FFKM, generally offer better abrasion resistance compared to softer materials like silicone or EPDM. However, harder elastomers may compromise sealing performance in dynamic applications requiring flexibility.
Shaft Speed and Runout
The elastomer must accommodate shaft movement and runout in dynamic sealing applications. High shaft speeds can generate heat and cause the elastomer to wear faster. Excessive shaft runout or misalignment can lead to uneven wear and leakage. Elastomers with good compression set resistance and elasticity, such as FKM or FFKM, are better suited for high-speed applications. Proper seal design, such as incorporating a coil spring or convolutions, can help compensate for shaft movement and maintain sealing effectiveness.