External flush systems have become increasingly prevalent in mechanical seals. These systems, which position the flush mechanism outside the main component, offer distinct advantages over traditional internally flush configurations.
In this blog post, we will delve into the intricacies of external flush systems, exploring their working principles and the benefits they provide. We will also examine the challenges associated with implementing external flush and highlight key applications where this approach excels compared to internal flush systems.
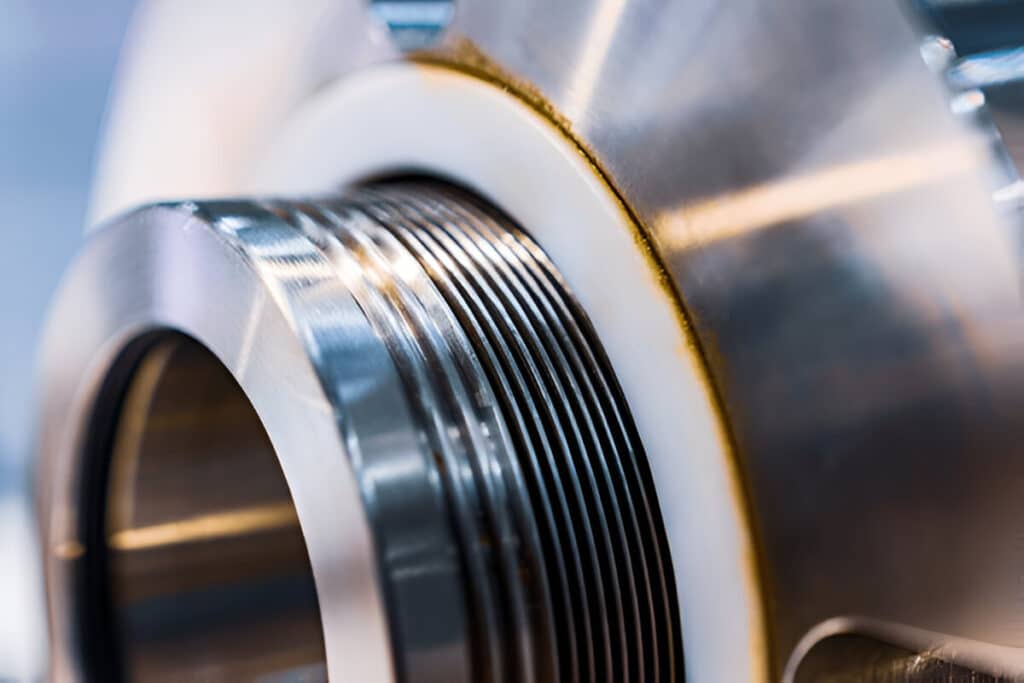
What Is External Flush
External flush is a method of introducing clean, cool fluid from an outside source into the seal chamber of a mechanical seal. Unlike internal flush, which recirculates process fluid from the pump discharge back to the seal, external flush uses a separate fluid supply. This fluid is typically maintained at a higher pressure than the sealed fluid, creating a positive flow into the seal chamber.
The external flush fluid serves several important purposes:
- It cools and lubricates the seal faces, reducing heat generation from friction and extending seal life.
- It prevents process fluid from entering the seal chamber, which is especially important when dealing with abrasive, corrosive, or polymerizing fluids that could damage the seal faces.
- It maintains a stable environment in the seal chamber, reducing the impact of process fluid variations or upset conditions on seal performance.
By providing a clean, stable environment for the mechanical seal, external flush can significantly improve seal reliability and longevity in challenging applications.
How External Flush Systems Work
In an external flush system, clean fluid is supplied to the mechanical seal from a source separate from the process fluid. This is typically achieved using a small flush pot or reservoir that is continuously filled with the flush fluid. The fluid is then pressurized using a pump or pressure-increasing device like a piston accumulator.
The pressurized flush fluid is piped into the seal chamber through a port, usually located in the gland plate behind the seal faces. A common arrangement is to connect the flush line between the stationary face and the gland plate, directing flow across the atmospheric side of the seal faces.
As the high-pressure flush fluid enters the seal chamber, it creates a positive flow toward the process side of the seal. This pressure differential prevents process fluid from entering the seal chamber, while continually washing away any heat or contaminants generated at the seal faces.
The used flush fluid then exits the seal chamber through the normal leakage paths along the shaft and out the gland vent and drain. Some flush fluid may also enter the process stream, which is acceptable as long as the flush fluid is compatible with the process and maintains the pressure differential.
To ensure a proper external flush, several key parameters must be controlled:
- Flush fluid pressure: Typically maintained at 15-25 psi above the seal chamber pressure to ensure positive flow.
- Flush fluid temperature: Cooled to help remove heat from the seal faces.
- Flush fluid cleanliness: Filtered to prevent introducing abrasives to the seal faces.
- Flush fluid flow rate: Sized to provide adequate cooling and lubrication without excessive dilution of the process fluid.
When properly implemented, an external flush system creates a highly controlled microenvironment for the mechanical seal, optimizing its performance and reliability. By isolating the seal from the process fluid and providing clean, stable conditions, external flush allows mechanical seals to operate successfully in applications that would otherwise prove too challenging.
Benefits of External Flush
Improved cooling and lubrication
With an external flush system, a dedicated supply of clean, cool fluid is continuously circulated through the seal chamber. This provides more effective heat removal and lubrication compared to relying solely on the process fluid, as is the case with internal flush systems. The cleaner, cooler fluid helps extend seal life, especially in high-temperature or high-pressure applications.
Reduced contamination
External flush systems introduce a separate, clean fluid into the seal chamber, which helps prevent process contaminants from entering and damaging the sealing surfaces. In contrast, internal flush systems rely on the process fluid itself, which may contain abrasive particles, corrosive chemicals, or other harmful substances that can accelerate seal wear and failure.
Greater flexibility in fluid selection
Since external flush systems use a dedicated fluid supply, the type of fluid can be optimized for the specific sealing requirements, such as viscosity, lubricating properties, and compatibility with seal materials. This allows for better performance and longer seal life. Internal flush systems, on the other hand, are limited to using the process fluid, which may not have ideal properties for sealing.
Easier monitoring and maintenance
External flush systems typically include provisions for monitoring fluid pressure, temperature, and flow rate, as well as for sampling the fluid to check for contaminants or degradation. This allows for proactive maintenance and early detection of potential problems. Internal flush systems do not provide these monitoring and maintenance capabilities, making it more difficult to ensure optimal seal performance.
Challenges of External Flush
Added complexity and cost
Implementing an external flush system requires additional piping, valves, instrumentation, and a separate fluid reservoir, which increases the overall complexity and cost of the sealing system compared to an internal flush design. The extra components also require more space and can be challenging to retrofit into existing equipment.
Potential for leakage and contamination
With more piping and connections, external flush systems introduce additional potential leak points, which can lead to fluid loss, environmental concerns, and safety hazards. If the external flush fluid becomes contaminated, it can actually harm the sealing surfaces rather than protect them, so careful fluid management is critical.
Increased maintenance requirements
The additional components and fluid handling requirements of external flush systems necessitate more frequent inspection, testing, and maintenance compared to simpler internal flush designs.
Compatibility concerns
The external flush fluid must be compatible not only with the seal materials but also with the process fluid in case of accidental mixing. This can limit the choice of flush fluids and may require special consideration in system design to prevent cross-contamination.
Applications of External Flush
High-temperature processes
In applications where the process fluid temperature exceeds the limits of the seal materials or the fluid’s lubricating properties, an external flush system can provide a cooler, more suitable fluid to extend seal life. This is common in industries such as oil and gas processing, chemical manufacturing, and power generation.
Highly abrasive or corrosive fluids
When handling fluids with high levels of abrasive particles or corrosive substances, an external flush system can help protect the sealing surfaces by introducing a clean, non-abrasive, and non-corrosive fluid into the seal chamber.
Processes with high solids content
In applications involving fluids with a high concentration of suspended solids, such as paper pulp or food slurries, an external flush system can help prevent the buildup of solids in the seal chamber, which could otherwise lead to clogging and premature seal failure.
Hazardous or toxic fluids
When dealing with dangerous fluids that pose environmental or safety risks in case of leakage, an external flush system can provide an additional barrier and help contain any potential leaks. The flush fluid can also be selected to be more environmentally friendly and less hazardous than the process fluid.