Machinery relies on critical components to prevent leaks and ensure reliable operation. However, many are unclear about the differences between two key sealing solutions: gaskets and mechanical seals.
Choosing the wrong type of seal for an application can lead to excessive leakage, frequent failures, higher maintenance costs, and unplanned downtime.
In this blog post, we’ll clarify what gaskets and mechanical seals are, and highlight their key differences in areas like allowed motion, leakage, installation, maintenance, cost, materials, and common applications. Armed with this knowledge, you’ll be able to select the ideal sealing solution for your machinery.
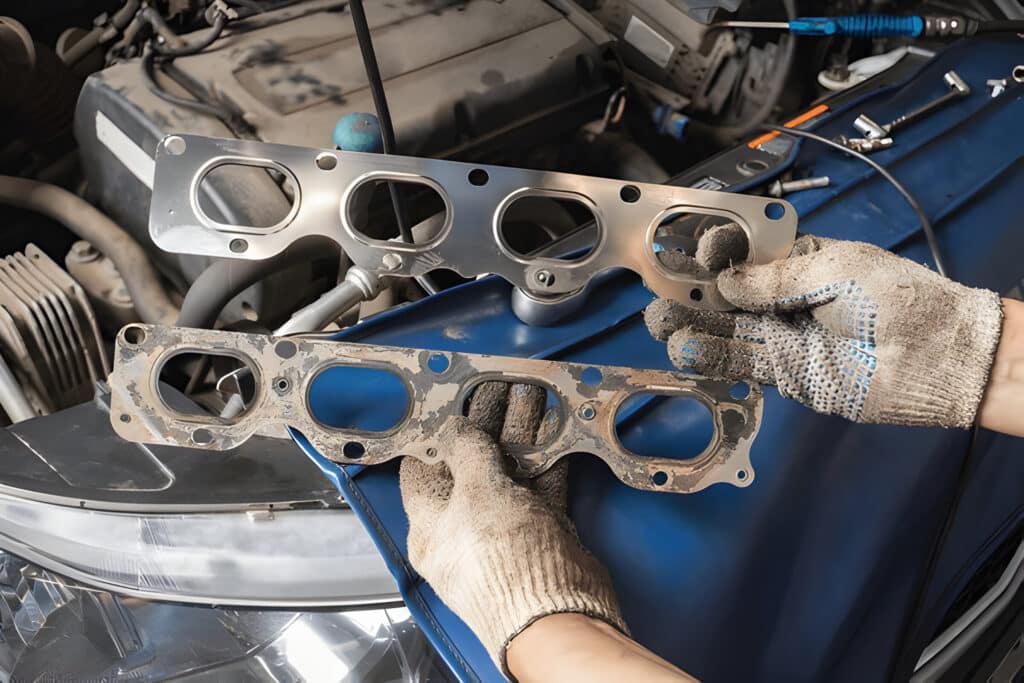
What Is Gasket
A gasket is a mechanical seal that fills the space between two or more mating surfaces, generally to prevent leakage from or into the joined objects while under compression. Gaskets allow for “less-than-perfect” mating surfaces on machine parts where they can fill irregularities.
What Is Mechanical Seal
A mechanical seal is a device that helps join systems or mechanisms together by preventing leakage (e.g. in a pumping system), containing pressure, or excluding contamination.
A mechanical seal contains several sealing points made from extremely flat and smooth surfaces (lapped faces), spring-loaded to close the seal, and secondary elastomeric seals designed to prevent leakage.
Difference Between Gasket and Mechanical Seal
Motion
Gaskets have no moving parts and provide a static seal. They rely on compression between two stationary flanges to prevent leakage.
Mechanical seals have moving parts and provide a dynamic seal between components that move relative to one another, such as a rotating shaft and stationary pump housing. The sealing surfaces slide against each other to accommodate shaft rotation while maintaining a tight seal.
Leakage
Gaskets allow for a small amount of controlled leakage, as they deform to fill surface irregularities.
Mechanical seals are precision-engineered devices designed to eliminate leakage completely.
Installation
Gaskets are relatively simple to install, typically requiring only proper alignment and bolt torque to compress the gasket between the mating flanges. Specialized training is generally not required.
Installing mechanical seals is a more complex process that requires careful handling of the seal components, precise alignment, and often specialized tools.
Maintenance
Gaskets require periodic inspection and replacement as they degrade over time due to age, temperature cycling, and exposure to the sealed media. Replacing a gasket is generally straightforward.
Mechanical seals have a longer service life but require more involved maintenance when service is needed. Seal face wear, spring fatigue, and secondary seal degradation necessitate periodic overhaul by skilled personnel and often require replacement of the entire seal cartridge.
Cost
Gaskets are an economical sealing solution, with costs dependent on the selected material, size, and quantity. Even exotic gasket materials are relatively inexpensive.
Mechanical seals have a significantly higher initial cost due to their precision manufacturing and exotic face material combinations.
Materials
Gasket materials are selected based on chemical compatibility, temperature resistance, and required compressibility. Common options include elastomers, graphite, PTFE, and fiber materials.
Mechanical seal faces are made from highly wear-resistant, precision-machinable materials like silicon carbide, tungsten carbide, and carbon. Secondary seals use elastomers and flexible graphite or PTFE wedges.
Application
Gaskets excel in large diameter, low pressure applications with chemically compatible media and allowable leakage, such as pipe flanges and heat exchangers.
Mechanical seals are the preferred choice for high pressure, high temperature, and high speed rotating equipment where leakage is undesirable or hazardous, such as pumps, compressors, and agitators.