In the dynamic world of machinery, seals serve as critical components that prevent leakage and maintain optimal performance. Two prominent types of seals, labyrinth seals and carbon seals, employ distinct mechanisms to achieve this goal.
This blog post will delve into the fundamental differences between these two sealing technologies, exploring their unique characteristics, applications, and advantages in various industrial settings.
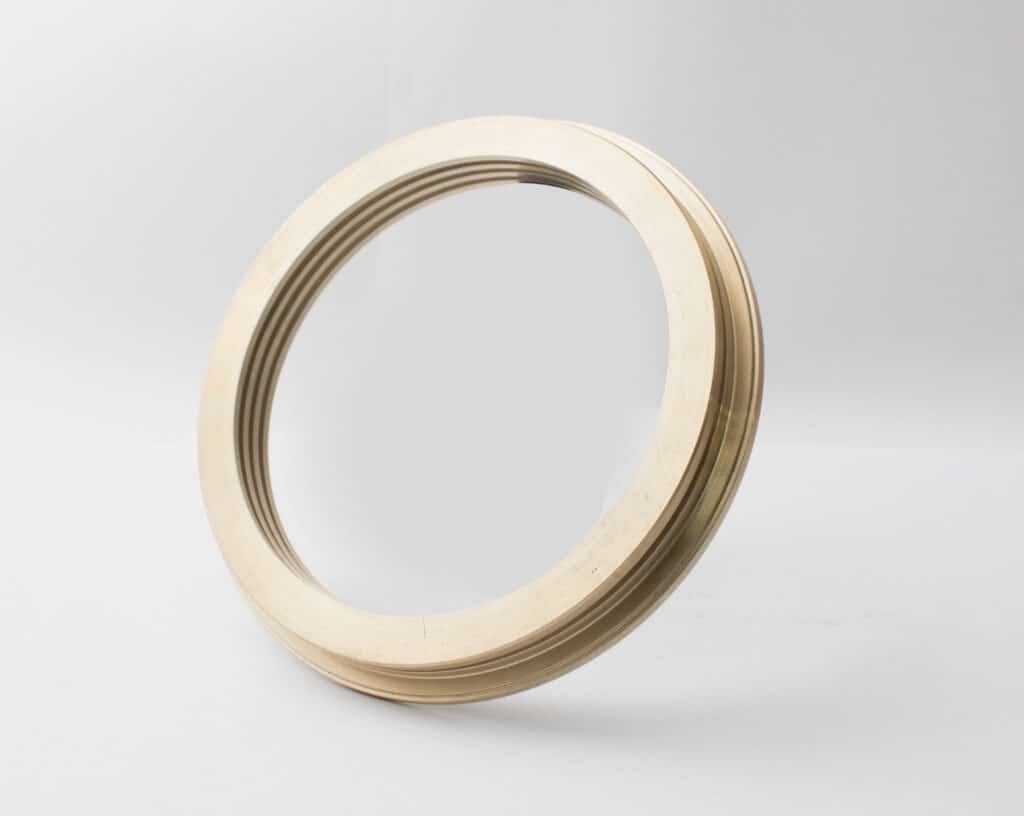
What Is Labyrinth Seal
A labyrinth seal is a type of non-contact seal that relies on a tortuous path to minimize leakage between rotating and stationary components. It consists of a series of alternating teeth or knives on the rotating part and corresponding grooves or a honeycomb surface on the stationary part. As fluid attempts to pass through the seal, it encounters resistance due to the complex path, resulting in a pressure drop and reduced leakage. Labyrinth seals are commonly used in turbomachinery, such as gas turbine engines, compressors, and steam turbines, to control the flow of gases or liquids while allowing for relative motion between components.
Advantages of Labyrinth Seals
Low Friction and Wear
One of the primary advantages of labyrinth seals is their non-contact nature. Unlike contact seals, such as mechanical seals or carbon ring seals, labyrinth seals do not rely on physical contact between the rotating and stationary components. This eliminates friction and minimizes wear, resulting in longer seal life and reduced maintenance requirements.
High-Temperature Compatibility
Labyrinth seals are well-suited for high-temperature applications. They can be manufactured from materials that withstand elevated temperatures, such as stainless steel, Inconel, or ceramic composites. This makes them ideal for use in gas turbine engines, where operating temperatures can exceed 1000°C.
Tolerance to Misalignment and Shaft Movement
The non-contact design of labyrinth seals allows for some degree of misalignment and shaft movement without compromising sealing performance. This tolerance is particularly useful in applications where shaft vibration or thermal expansion is expected, as the seal can accommodate these changes without excessive leakage or damage.
Disadvantages of Labyrinth Seals
Higher Leakage Compared to Contact Seals
While labyrinth seals effectively reduce leakage, they typically have higher leakage rates compared to contact seals like mechanical seals or carbon ring seals. The non-contact nature of labyrinth seals inherently allows for some fluid to pass through the tortuous path, especially if the clearances are not tightly controlled.
Sensitivity to Clearances
The performance of labyrinth seals heavily depends on the clearance between the rotating and stationary components. Smaller clearances generally result in better sealing but also increase the risk of contact and wear if shaft movement or misalignment occurs. Larger clearances, on the other hand, allow for more tolerance to movement but at the expense of higher leakage rates.
Potential for Clogging
In some applications, particularly those involving dirty or particle-laden fluids, labyrinth seals can be susceptible to clogging. Debris can accumulate in the grooves or between the teeth, reducing the seal’s effectiveness and potentially causing damage.
Limited Pressure Differential Capability
Labyrinth seals have a limited ability to handle high pressure differentials across the seal. As the pressure differential increases, the leakage rate through the seal also increases. In applications with very high pressure differentials, multiple stages of labyrinth seals or alternative sealing technologies, such as dry gas seals or mechanical seals, may be required to achieve acceptable leakage rates.
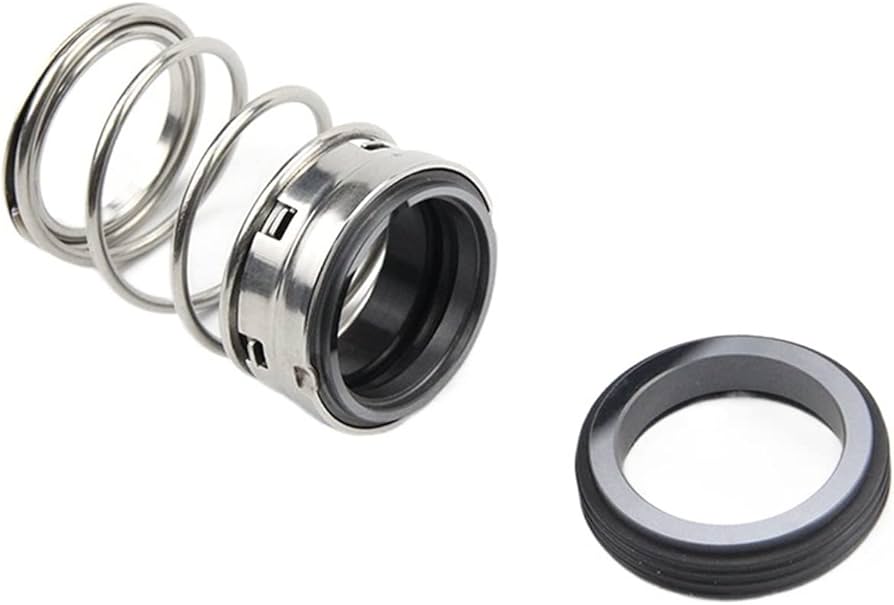
What Is Carbon Seal
Carbon seals, also known as carbon ring seals or mechanical seals, are a type of dynamic seal that provides a positive seal between rotating and stationary components. Unlike labyrinth seals, which rely on a series of clearances to reduce leakage, carbon seals create a physical barrier to prevent fluid or gas escape.
The design of carbon seals typically consists of a stationary carbon ring that is spring-loaded against a rotating mating ring. As the shaft rotates, the carbon ring maintains contact with the mating ring, creating a sealed interface. This configuration allows carbon seals to effectively contain fluids or gases, even under high pressure and temperature conditions.
Advantages of Carbon Seals
Low Leakage Rates
One of the primary advantages of carbon seals is their ability to maintain extremely low leakage rates. The tight clearances and positive sealing action of the carbon rings result in minimal fluid or gas escape, making them ideal for applications where leakage control is critical.
Long Service Life
Carbon seals are known for their durability and long service life. The carbon materials used in these seals have excellent wear resistance, allowing them to withstand prolonged contact with the rotating mating ring. Additionally, carbon seals can operate with minimal lubrication, reducing the need for frequent maintenance and extending the overall life of the sealing system.
Disadvantages of Carbon Seals
Higher Initial Cost
One of the main disadvantages of carbon seals is their higher initial cost compared to other sealing technologies, such as labyrinth seals. The precision manufacturing process and high-quality materials used in carbon seals contribute to their increased expense.
Limited Tolerance to Misalignment
Carbon seals have limited tolerance to shaft misalignment or runout. Any significant deviation from the optimal alignment can lead to increased wear and premature failure of the sealing components.
Sensitivity to Pressure and Temperature Fluctuations
While carbon seals can handle a wide range of operating conditions, they are more sensitive to sudden pressure or temperature fluctuations compared to labyrinth seals. Rapid changes in these parameters can cause thermal expansion or contraction of the sealing components, potentially affecting the seal’s performance or leading to damage.
Requires Lubrication
Unlike labyrinth seals, which can operate without lubrication, carbon seals require a thin film of lubrication between the carbon ring and the mating ring to reduce friction and wear. This lubrication is typically provided by the process fluid itself or an external lubrication system. The need for lubrication adds complexity to the sealing system and may require additional maintenance.
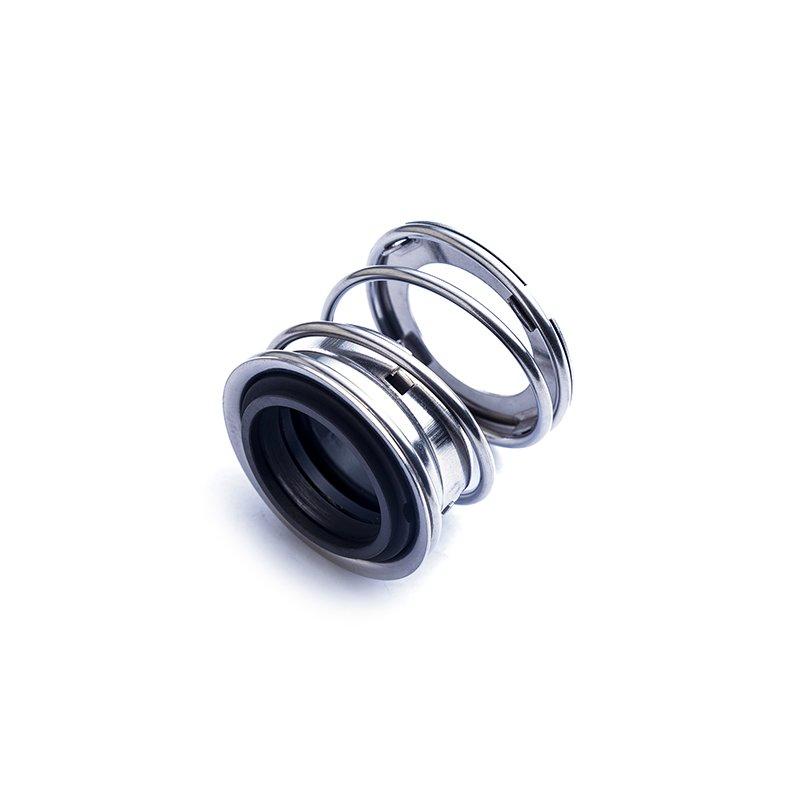
Key Differences Between Labyrinth Seals and Carbon Seals
Design and Operation
The fundamental difference between labyrinth seals and carbon seals lies in their design and operation. Labyrinth seals are non-contacting seals that consist of a series of alternating teeth and grooves on the rotating and stationary components. These seals operate by creating a tortuous path for the fluid, causing pressure drops and reducing leakage.
In contrast, carbon seals are positive contact seals that utilize carbon rings pressed against a rotating shaft or face to create a seal. The carbon rings are typically held in place by springs or other resilient elements, ensuring constant contact with the sealing surface.
Leakage Control
Labyrinth seals rely on the creation of turbulent flow through the labyrinth passages to minimize leakage. While they do not provide a complete seal, labyrinth seals can effectively reduce leakage to acceptable levels in many applications.
On the other hand, carbon seals provide a positive seal, offering superior leakage control compared to labyrinth seals. The direct contact between the carbon rings and the sealing surface prevents fluid from escaping, making carbon seals ideal for applications requiring stringent leakage control.
Wear and Maintenance
Labyrinth seals are non-contacting seals and, therefore, experience minimal wear during operation. They are generally more tolerant of contaminants and can operate for extended periods without requiring frequent maintenance or replacement.
In contrast, carbon seals are subject to wear due to the constant contact between the carbon rings and the sealing surface. This wear can lead to increased leakage over time and may necessitate periodic replacement of the carbon rings.
Applications
Labyrinth seals are commonly used in gas turbine engines, compressors, and steam turbines, where they are effective in sealing high-pressure, high-temperature gases. They are also used in bearing sumps to prevent oil leakage and contamination.
Carbon seals, on the other hand, are widely used in pumps, mixers, and other rotating equipment handling liquids or gases. They are particularly suitable for applications requiring low leakage rates, such as in the chemical, petrochemical, and pharmaceutical industries. Carbon seals are also used in combination with other seal technologies, such as dry gas seals, to provide enhanced sealing performance in demanding operating conditions.