Mechanical seals are critical components in the machinery industry, used to prevent leakage and maintain system integrity in rotating equipment. While all mechanical seals serve this primary purpose, they can be broadly categorized into two types based on their design and operating principles: pressurized and unpressurized seals.
This blog post will delve into the fundamental differences between these two seal types, examining factors such as fluid compatibility, pressure dynamics, leakage behavior, complexity, and typical applications. By understanding the distinctions and advantages of each type, engineers and maintenance professionals can make informed decisions when selecting and implementing mechanical seals in their systems.
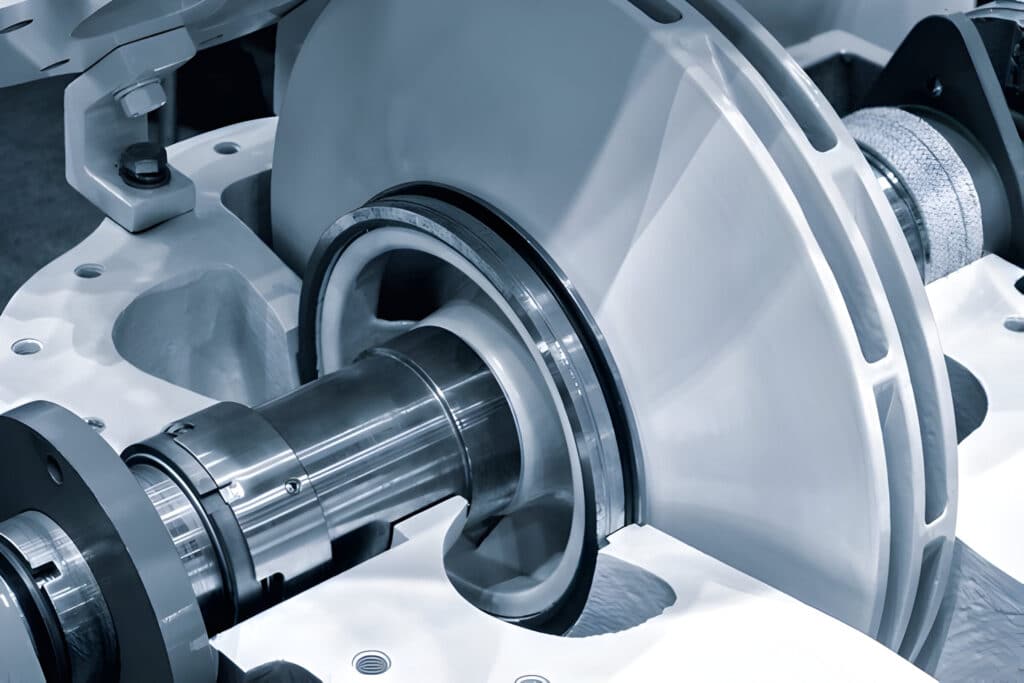
What Is Pressurized Mechanical Seal
A pressurized mechanical seal, also known as an externally pressurized seal, is a type of mechanical seal that relies on an external fluid source to maintain a higher pressure in the seal cavity than the process fluid. This external fluid, typically a clean, compatible liquid or gas, is introduced into the seal chamber at a pressure slightly higher than the stuffing box pressure.
The pressurized fluid creates a positive pressure differential across the sealing faces, ensuring that the clean barrier fluid flows from the seal cavity into the process fluid. This positive outward flow prevents the ingress of process fluid into the seal chamber, thus protecting the sealing faces from contamination and extending seal life.
Pressurized mechanical seals are commonly used in applications involving dirty, abrasive, or corrosive process fluids, as well as in high-pressure or high-temperature environments. The external pressurization helps to maintain a stable fluid film between the sealing faces, reducing wear and enhancing seal performance.
What Is Unpressurized Mechanical Seal
An unpressurized mechanical seal, also referred to as a self-energized seal or a conventional mechanical seal, operates without an external pressurization source. In this type of seal, the sealing action is achieved through a combination of spring force and hydraulic pressure generated by the process fluid itself.
The seal consists of a stationary and a rotating face, with the stationary face typically being spring-loaded to maintain contact with the rotating face. As the shaft rotates, the process fluid enters the seal chamber and generates hydraulic pressure that pushes the sealing faces together, creating a thin fluid film between them. This fluid film helps to lubricate the faces and prevent direct contact, reducing friction and wear.
Unpressurized mechanical seals are generally simpler in design and less expensive compared to pressurized seals. They are suitable for applications with clean, non-abrasive process fluids and moderate operating conditions. However, since the sealing effectiveness depends on the pressure and properties of the process fluid, unpressurized seals may experience leakage if the fluid pressure drops below a certain level or if the fluid contains abrasive particles that can damage the sealing faces.
Key Differences Between Pressurized and Unpressurized Mechanical Seals
Pressurized and unpressurized mechanical seals differ in several key aspects, including fluid type, pressure relationship, leakage direction, primary purpose, applications, seal support system, and complexity and cost.
Fluid Type
Pressurized mechanical seals are suitable for handling a wide range of fluids, including liquids, gases, and multiphase fluids. These seals can effectively contain fluids with various properties, such as high viscosity, high temperature, or corrosive nature.
On the other hand, unpressurized mechanical seals are primarily designed for liquid applications and may not be suitable for handling gases or multiphase fluids.
Pressure Relationship
In pressurized mechanical seals, the fluid pressure inside the seal chamber is higher than the atmospheric pressure surrounding the seal. This pressure differential helps to maintain a positive seal and prevent leakage.
Conversely, unpressurized mechanical seals operate with the fluid pressure inside the seal chamber being equal to or lower than the atmospheric pressure.
Leakage Direction
Due to the pressure relationship, pressurized mechanical seals are designed to contain fluid within the seal chamber, preventing leakage to the atmosphere. If any leakage occurs, it is typically directed back into the process fluid.
In contrast, unpressurized mechanical seals allow a controlled amount of leakage from the process fluid to the atmosphere, which is then collected or drained away.
Primary Purpose
The primary purpose of pressurized mechanical seals is to provide a robust sealing solution for critical applications where fluid containment is of utmost importance. These seals are designed to minimize or eliminate leakage, even under challenging conditions.
Unpressurized mechanical seals, on the other hand, focus on providing a reliable sealing solution while allowing a small amount of controlled leakage for lubrication and cooling of the seal faces.
Applications
Pressurized mechanical seals find extensive use in industries such as oil and gas, petrochemical, chemical processing, and power generation, where high-pressure and high-temperature fluids are encountered. These seals are well-suited for applications involving hazardous or environmentally sensitive fluids.
Unpressurized mechanical seals are commonly used in applications with lower pressure and temperature requirements, such as water pumps, general industrial pumps, and mixers.
Seal Support System
Pressurized mechanical seals often require a seal support system to maintain the necessary fluid pressure and temperature within the seal chamber. This system may include components such as barrier fluid reservoirs, pressure regulators, and heat exchangers.
Unpressurized mechanical seals typically do not require an extensive seal support system, as they rely on the process fluid itself for lubrication and cooling.
Complexity and Cost
Due to the additional components and design considerations required for pressurized mechanical seals, they tend to be more complex and expensive compared to unpressurized mechanical seals. The seal support system adds to the overall complexity and cost of the sealing solution.
Unpressurized mechanical seals have a simpler design and fewer components, making them more cost-effective for applications where a small amount of controlled leakage is acceptable.