Dry gas seals are essential for reducing emissions and leakage in rotating machinery. However, even these advanced seals have a small but measurable leak rate that can be impacted by various factors. Left unchecked, excessive leakage leads to lost product, reduced efficiency, and potential safety hazards.
In this blog post, we’ll dive into the typical leak rates of dry gas seals, examine the key factors that influence leakage, and discuss methods for accurately measuring and testing seal performance to ensure optimal operation.
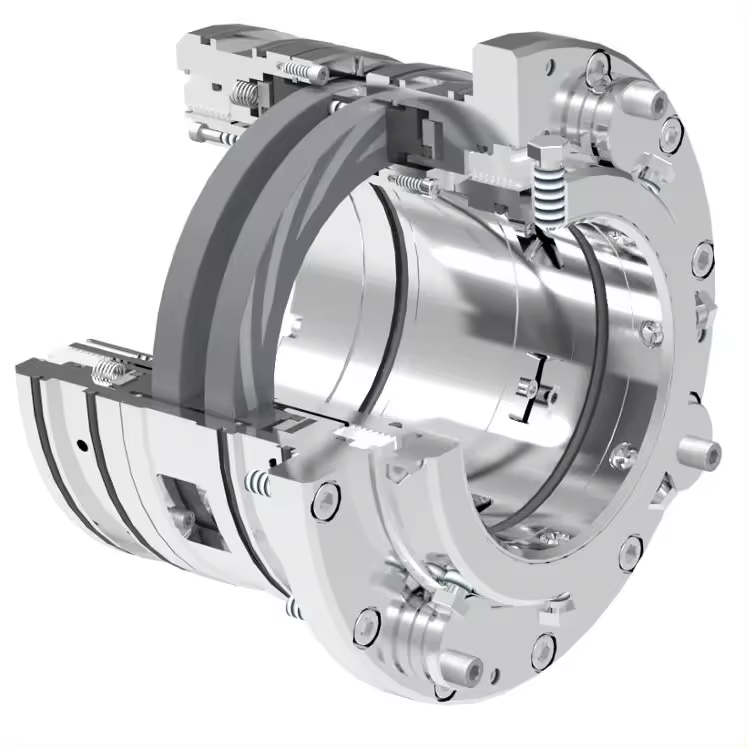
Typical Leak Rates of Dry Gas Seals
Under normal operating conditions, a typical dry gas seal will leak at a rate of 0.5 to 3 standard cubic feet per minute (scfm) across each individual seal interface. For a standard system consisting of two seals in tandem, this results in a total seal leakage rate between 1 to 6 scfm. This leakage rate is dramatically lower than what is observed with dual wet seal arrangements, which typically exhibit leakages ranging from 40 to 200 scfm under similar conditions.
In fact, converting from a wet seal to a dry gas seal system can reduce seal-related emissions by up to 97%. For a compressor operating at a suction pressure of 1000 psi, a dual wet seal system leaking at 100 scfm would lose approximately 52.6 million standard cubic feet of process gas per year. In contrast, a dry gas seal system with a total leakage of 3 scfm would only lose around 1.6 million scf annually – a reduction of 51 million scf of emissions.
Factors Affecting Dry Gas Seal Leak Rates
Operating Pressure
Higher pressures generally result in increased leakage due to the greater pressure differential across the seal faces. As pressure builds, it becomes more challenging to maintain the thin gas film between the rotating and stationary seal rings.
Seal Size
Larger seals, with greater surface area along the sealing interface, are more prone to leakage compared to smaller seals. This is because maintaining a uniform gas film across a larger area becomes increasingly difficult.
Seal Design
Factors such as the geometry of the seal faces, groove patterns, and lift features all contribute to the seal’s ability to generate and maintain a stable gas film. Advanced seal designs, such as bidirectional tapered grooves or micro-structures on the seal faces, can enhance gas film stiffness and reduce leakage.
Gas Properties
Gas viscosity, molecular weight, and compressibility affect the behavior of the gas film between the seal faces. Lower viscosity gases tend to leak more readily, while higher molecular weight gases can help reduce leakage. The presence of contaminants or condensates in the gas can also disrupt the gas film and lead to increased leakage.
Operating Speed
Higher speeds generally lead to increased lift and a more stable gas film, which can help reduce leakage. However, excessively high speeds can also cause vibration and dynamic instability, compromising seal performance.
Temperature
Higher temperatures can cause thermal expansion of the seal components, potentially altering the clearances and contact pressures at the sealing interface. Additionally, elevated temperatures may degrade the physical properties of the seal materials over time, leading to increased wear and leakage.
Contamination
Contaminants can cause abrasive wear, erosion, or chemical degradation of the seal faces, resulting in increased leakage paths. Even small amounts of contamination can disrupt the thin gas film and compromise sealing effectiveness.
Seal Gas Pressure
Seal gas is typically injected between the primary and secondary seals to provide a barrier and prevent process gas leakage to the atmosphere. Insufficient seal gas pressure can allow process gas to leak past the primary seal, while excessive pressure can cause seal gas to leak into the process.
Measuring and Testing Dry Gas Seal Leak Rates
Measuring Vent Flow
One of the most straightforward methods for measuring dry gas seal leak rates is to monitor the flow rate of the gas vented from the seal housing. This is typically done using flow meters installed in the vent lines. By measuring the steady-state vent flow during normal operation, operators can determine the total leakage rate across both the primary and secondary seals. Comparing the measured values with the manufacturer’s specifications or historical data can help identify any deviations or abnormalities in seal performance.
Pressure Decay Method
The pressure decay method involves isolating the seal chamber and monitoring the pressure drop over time. This test is usually conducted during compressor shutdown or maintenance periods. The seal chamber is pressurized to a known initial pressure, and then the pressure decay is recorded over a specific time interval. By analyzing the rate of pressure decay, the leak rate can be calculated using the ideal gas law. This method provides a quantitative assessment of seal leakage and can help detect any significant deviations from normal performance.
Helium Leak Detection
Helium leak detection is a highly sensitive technique used to pinpoint the location and magnitude of seal leaks. In this method, a small amount of helium gas is introduced into the seal gas supply or injected directly into the seal chamber. A helium leak detector, equipped with a mass spectrometer, is then used to scan the seal area and identify any helium escaping through the leakage paths. This method allows for precise localization of leaks and can detect even minute leakage rates, making it valuable for troubleshooting and seal integrity assessments.
Bubble Tests
Bubble tests provide a visual indication of gas leakage from dry gas seals. During a bubble test, a leak detection solution is applied to the seal area while the compressor is pressurized. If there are any leaks present, bubbles will form at the leak locations. This method is simple and quick, making it useful for initial leak checks or on-site troubleshooting. However, it is qualitative in nature and does not provide a precise measurement of the leak rate. Bubble tests are often used in conjunction with other leak detection methods for a comprehensive seal performance assessment.