Pump seal failure is one of the most frequent problems in industrial pumping systems, causing costly downtime and repairs. Understanding why seals fail helps prevent these issues and keeps your equipment running smoothly.
Mechanical Causes
Mechanical problems account for nearly 40% of all seal failures. These issues typically stem from improper installation or equipment wear.
Misalignment and Installation Errors
Shaft misalignment causes 15-20% of mechanical seal failures in pumps. When the pump shaft doesn’t line up properly with the motor shaft, it creates uneven pressure on the seal faces.
This misalignment forces the seal to flex with every rotation. Over time, this constant flexing breaks down the seal material and causes leaks.
Installation errors are equally damaging. Common mistakes include using the wrong tools, applying uneven pressure during installation, or contaminating the seal faces with dirt or oil from fingers.
Worn Bearings/Shafts and Vibration
Worn bearings create excessive shaft movement, which damages seals within 500-1000 operating hours. When bearings wear out, they allow the shaft to wobble instead of rotating smoothly.
This wobbling creates gaps between the seal faces. These gaps let fluid escape and allow contaminants to enter the sealing area.
Vibration levels above 0.3 inches per second typically indicate bearing problems. Regular vibration monitoring can catch these issues before they destroy your seals.
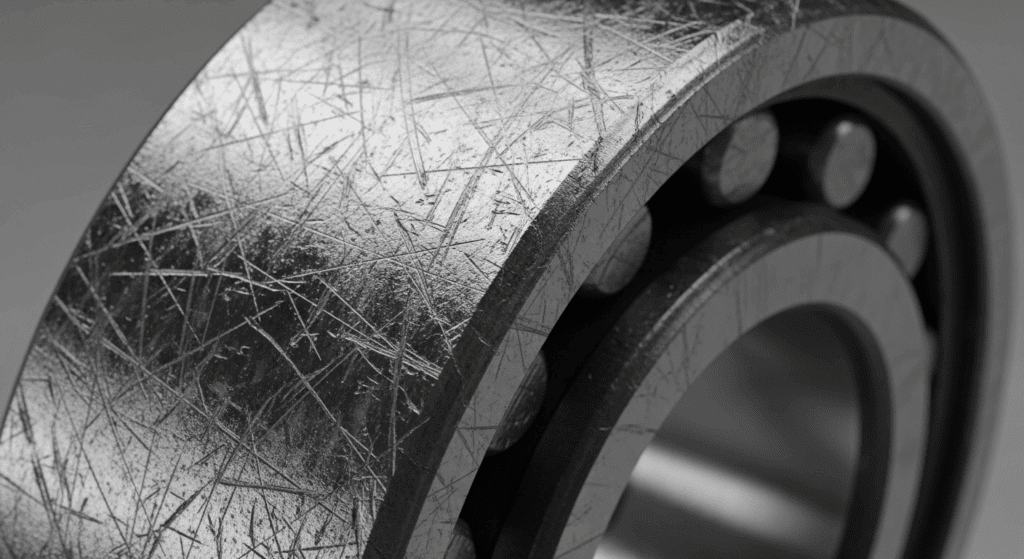
Thermal-mechanical Stress (Heat Checking)
Heat checking appears as small cracks on the seal face, resembling a spider web pattern. This happens when the seal faces experience rapid temperature changes of 50°F or more.
The constant expansion and contraction from temperature swings creates stress fractures. These fractures grow larger with each heat cycle until the seal fails completely.
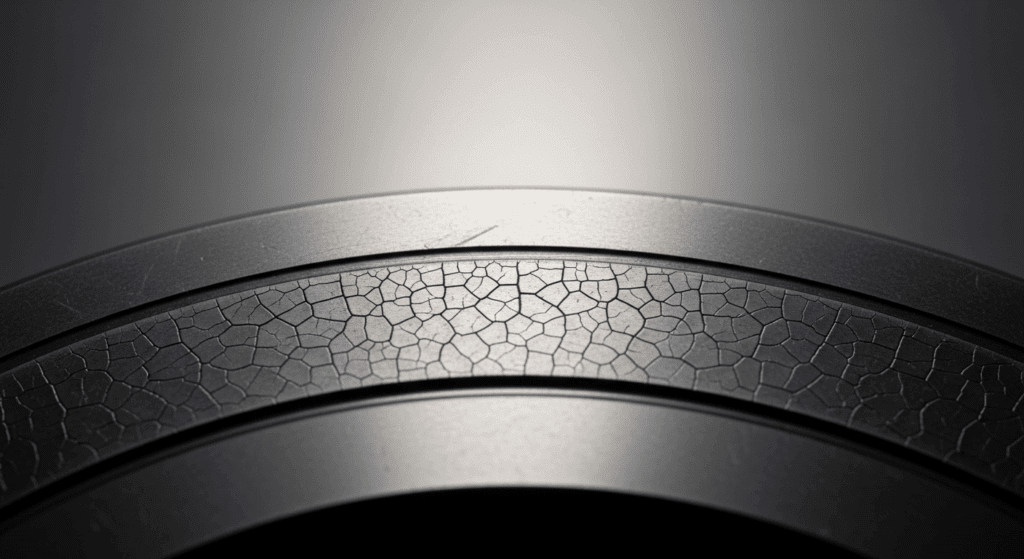
Operational Causes
How you run your pump directly impacts seal life. Operating mistakes can destroy a new seal in minutes or slowly damage it over months.
Dry Running / Loss of Lubrication
Running a pump dry destroys mechanical seals in less than 30 seconds. The seal faces need a thin film of liquid between them to prevent direct contact.
Without this liquid film, the faces rub together and generate extreme heat. Temperatures can reach 1000°F in seconds, melting or cracking the seal materials.
Loss of lubrication often happens when tanks run empty or when vapor locks form in the suction line. Installing low-level switches and proper venting prevents most dry-running incidents.
Cavitation and Vaporization
Cavitation occurs when pump suction pressure drops below the liquid’s vapor pressure. This creates tiny bubbles that violently collapse near the seal faces.
Each bubble collapse creates a microscopic hammer blow. Thousands of these impacts per second erode the seal face material like sandblasting.
Vaporization happens when liquid flashes to vapor at the seal interface. This vapor prevents proper lubrication and causes the same dry-running damage mentioned earlier.
Pressure Spikes and Hydraulic Shock
Pressure spikes exceeding 150% of normal operating pressure can instantly damage seals. These spikes often occur when valves close too quickly or when pumps start against closed discharge valves.
Hydraulic shock (water hammer) creates pressure waves that slam into the seal faces. A single severe shock can crack seal faces or blow out elastomers.
Installing pressure relief valves and using soft-start motors reduces these damaging pressure events. Proper valve operation procedures also prevent most hydraulic shock incidents.
Operating Outside Design Limits
Every mechanical seal has specific pressure, temperature, and speed limits. Operating beyond these limits shortens seal life dramatically.
Running a seal rated for 150 psi at 200 psi reduces its life by 75%. Similarly, exceeding temperature limits by just 25°F can cut seal life in half.
Always verify your operating conditions match the seal’s design specifications. When process conditions change, you may need different seal materials or designs.
Environmental Causes
The environment around your pump affects seal performance just as much as how you operate it. External factors can attack seal materials or interfere with proper operation.
Solids Contamination
Solid particles as small as 10 microns can damage seal faces. These particles get between the sealing surfaces and act like grinding compound.
Sandy or gritty fluids are obvious problems. But even clean-looking fluids can contain damaging particles from pipe scale, rust, or process contamination.
Installing proper filtration removes most harmful particles. Flush systems that continuously clean the seal area also extend seal life in contaminated services.
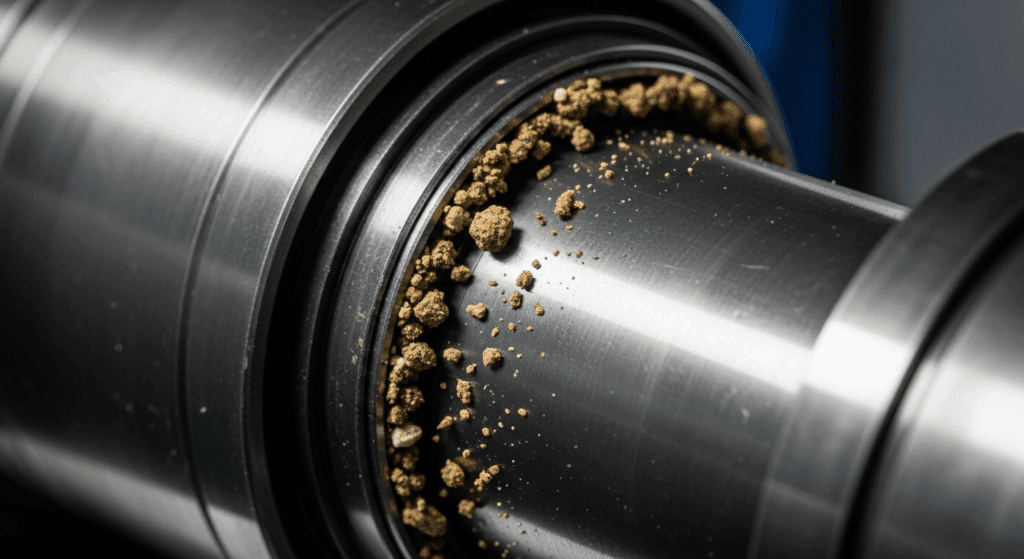
Corrosive / Chemical Attack
Chemical attack breaks down seal materials at the molecular level. The wrong material in the wrong chemical can fail in hours instead of years.
Elastomers swell, harden, or dissolve when exposed to incompatible chemicals. Metal components pit, crack, or erode when corrosion occurs.
Always verify chemical compatibility before selecting seal materials. When in doubt, consult compatibility charts or conduct immersion tests.
Extreme Temperatures
Temperatures below -20°F make elastomers brittle and prone to cracking. At the other extreme, temperatures above 400°F break down most seal materials.
Rapid temperature changes cause even more damage than steady extreme temperatures. A 100°F temperature swing can crack hard seal faces through thermal shock.
Using temperature-appropriate materials and avoiding rapid temperature changes prevents most thermal failures. Heat exchangers or cooling flush systems help in extreme temperature applications.
External Vibration and Shock
Nearby equipment can transmit vibration through piping and foundations to your pump. This external vibration adds to any existing pump vibration.
Construction activities, forklift traffic, or other pumps can create shock loads. These sudden impacts jar seal faces apart momentarily, allowing leakage and contamination.
Proper foundation design and vibration isolation reduce external vibration effects. Flexible connectors in piping also help isolate pumps from external vibration sources.
Material-Related Causes
Even the best seal design fails if you use the wrong materials. Material selection affects every aspect of seal performance, from chemical resistance to wear life.
Material Incompatibility
Using incompatible materials causes 25% of premature seal failures. Each seal material has specific chemical and temperature limitations.
For example, Buna-N rubber swells and softens in petroleum oils. Viton breaks down in steam service. Carbon graphite can’t handle strong oxidizers.
Always match seal materials to your specific service conditions. Consider temperature, pressure, chemical composition, and pH when selecting materials.
Abrasion and Erosion
Abrasion occurs when solid particles wear away seal faces through direct contact. Even soft particles like flour or sugar can be abrasive over time.
Erosion happens when high-velocity flow washes away seal material. This is especially problematic with slurries or high-speed pumps.
Hard face materials like silicon carbide resist abrasion better than soft materials. Special face designs can also redirect flow to minimize erosion.
Extrusion Under Pressure
High pressure forces soft seal components into clearance gaps. This extrusion damages O-rings, gaskets, and other elastomeric parts.
Pressure cycling makes extrusion worse. Each pressure spike pushes material further into gaps until pieces break off.
Using backup rings and selecting proper durometer materials prevents most extrusion problems. Minimizing clearances also reduces extrusion risk.
Compression Set and Hardening
Compression set occurs when elastomers permanently deform under constant compression. The material loses its ability to spring back and seal properly.
Heat and chemical exposure accelerate compression set. An O-ring that should last years might fail in months under harsh conditions.
Regular seal replacement before compression set occurs prevents unexpected failures. Choosing high-quality elastomers also extends service life.
Fatigue and Material Wear
All seal materials experience fatigue over time. Constant pressure changes, temperature cycles, and mechanical stress gradually weaken materials.
Normal wear slowly removes material from seal faces. This wear accelerates when conditions aren’t ideal or when maintenance is neglected.