Are you tired of constantly replacing mechanical seals in your industrial machinery? Premature seal failure can lead to costly downtime and maintenance expenses.
The lifespan of mechanical seals varies widely depending on factors like operating conditions, seal design, and materials used. Without understanding these critical factors, you could be setting yourself up for frequent and expensive seal replacements.
In this blog post, we’ll dive into the typical lifespans of different mechanical seal types and examine the key variables that impact seal longevity.
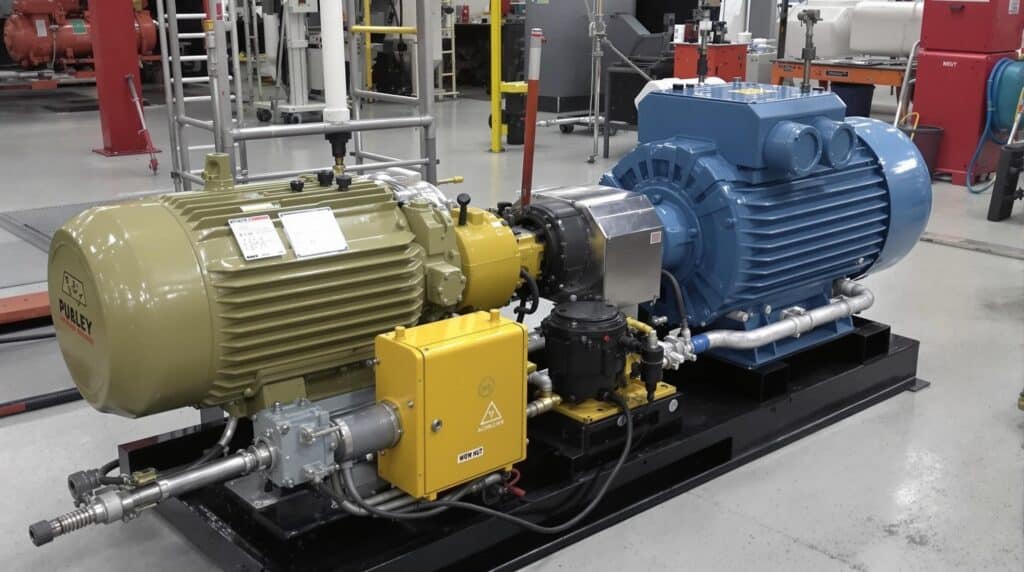
Typical Lifespan of Mechanical Seals
Seal Type | Typical Lifespan (Years) | Notes |
---|---|---|
Elastomeric Bellows | 1-3 | Limited by elastomer durability; best for clean, low-pressure applications. |
Pusher Seals | 2-5 | Balanced designs tend to last longer. Subject to wear at dynamic O-rings. |
Metal Bellows | 3-6 | Resistant to pressure and temperature extremes; may be damaged by excessive vibration. |
Split Seals | 3-5 | Convenient to install/replace; secondary seals are potential failure points. |
Gas Seals | 5-7+ | Designed for optimal performance in gas service; sensitive to particulates and liquids. |
Dry-Running Gas Seals | 6-10+ | Advanced face materials enable the seal to run without liquid lubrication. |
General/Standard | 1.5 – 3 | Under normal operating conditions. This is a baseline, and numerous factors can influence the actual lifespan. Some can last much longer in ideal conditions, others may fail sooner if conditions are harsh (high temps, pressures, abrasive/corrosive fluids.) |
Cartridge Seals | Often longer than standard | Due to pre-assembled nature, reducing chances of installation errors. |
Factors Affecting Mechanical Seal Lifespan
Operating Conditions
- Temperature: Extreme temperatures, both high and low, can cause thermal expansion or contraction of seal components, leading to increased wear and reduced lifespan.
- Pressure: High pressure can cause deformation of seal faces, resulting in leakage and premature failure.
- Shaft Speed: Higher shaft speeds generate more heat and increase wear on the seal faces, reducing seal life.
- Fluid Compatibility: The sealed fluid must be compatible with the seal materials to prevent chemical attack, corrosion, or swelling of elastomers.
Seal Design
- Face Flatness and Width: Seal faces must be flat and have sufficient width to maintain a stable fluid film between the faces, minimizing wear.
- Balance Diameter: Properly balanced seals ensure even pressure distribution across the seal faces, reducing wear and extending seal life.
- Spring Selection: The spring must provide adequate force to maintain face contact under all operating conditions without causing excessive wear.
Materials
Seal Face Materials
Material Type | Typical Lifespan (Years) |
---|---|
Carbon Graphite | 1-5 |
Silicon Carbide (SiC) | 3-7 |
Tungsten Carbide (WC) | 5-10 |
Ceramic (Aluminum Oxide) | 2-5 |
Stainless Steel | 2-5 |
Elastomers
Elastomer | Material Type | Typical Lifespan (Years) |
---|---|---|
Nitrile (NBR) | Synthetic Rubber | 1-3 |
Viton (FKM) | Fluorocarbon Rubber | 2-5 |
Ethylene Propylene (EPR/EPDM) | Synthetic Rubber | 3-7 |
Silicone (VMQ) | Silicone Rubber | 1-4 |
PTFE (Teflon) | Fluoropolymer | 3-10 |
FFKM (Kalrez) | Perfluorocarbon Rubber | 5-10+ |