Seals are critical components in a wide range of machinery and industrial applications, preventing fluid leakage and ensuring efficient operation. Among the various types of seals, back-to-back and face-to-face configurations are commonly used in rotary equipment.
This article will explore the key differences between back-to-back and face-to-face seals, including their orientation, mounting arrangements, pressure handling capabilities, space requirements, maintenance considerations, and typical applications. By understanding these distinctions, engineers and maintenance professionals can make informed decisions when selecting and maintaining seals for their specific machinery needs.
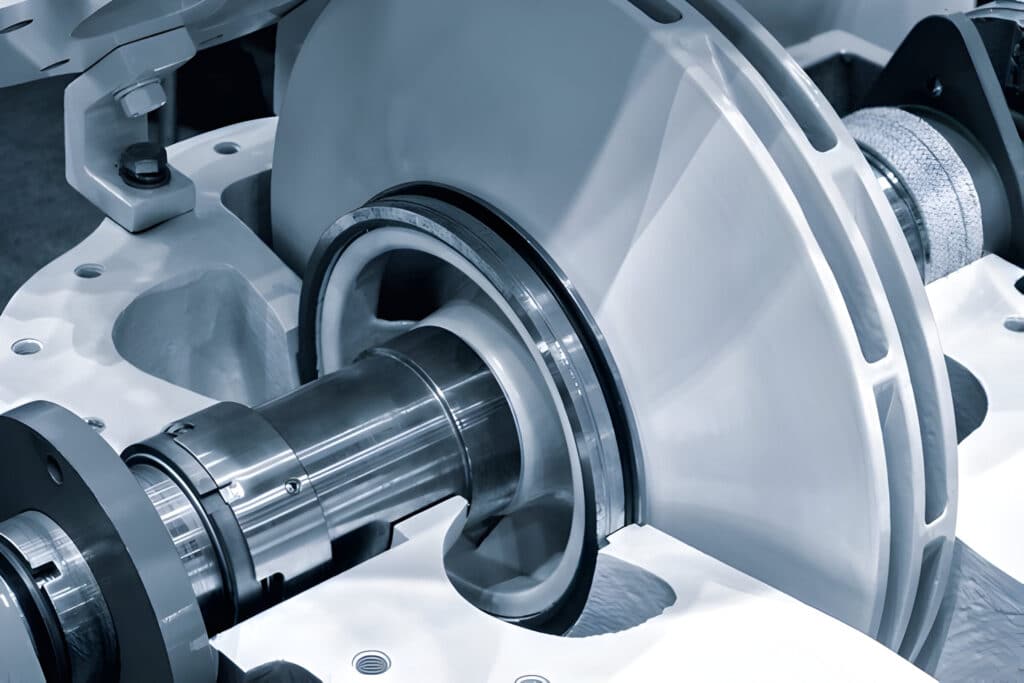
What Is Back-to-Back Seal
A back-to-back seal, also known as a double seal or tandem seal, is a type of mechanical seal arrangement commonly used in rotating equipment such as pumps, mixers, and compressors. In this configuration, two mechanical seals are mounted in series, with their rotating faces arranged in opposite directions, facing away from each other.
The primary seal, located closest to the process fluid, acts as the main barrier against leakage. The secondary seal, positioned behind the primary seal, serves as a backup in case the primary seal fails. A buffer fluid, typically a compatible lubricating liquid, is circulated between the two seals to lubricate, cool, and maintain a stable environment for the sealing faces.
Back-to-back seals offer enhanced reliability and safety compared to single seals, as the secondary seal provides an additional layer of protection against leakage. This arrangement is particularly beneficial in applications involving hazardous, toxic, or environmentally sensitive fluids, where seal failure could lead to significant consequences.
What Is Face-to-Face Seal
A face-to-face seal, also referred to as a double opposed seal or tandem opposed seal, is another type of mechanical seal arrangement used in rotating equipment. In this configuration, two mechanical seals are mounted in series, with their rotating faces arranged in the same direction, facing towards each other.
Similar to the back-to-back arrangement, the primary seal in a face-to-face configuration is located closest to the process fluid and acts as the main barrier against leakage. The secondary seal is positioned behind the primary seal and serves as a backup in case of primary seal failure.
However, unlike the back-to-back arrangement, the face-to-face configuration allows for the use of a pressurized barrier fluid between the two seals. This barrier fluid is maintained at a higher pressure than the process fluid, creating a positive pressure differential across the primary seal faces. As a result, any leakage that may occur would be the clean barrier fluid leaking into the process, rather than the process fluid escaping to the atmosphere.
Face-to-face seals are commonly used in applications where contamination of the process fluid must be avoided at all costs, such as in the food, pharmaceutical, or semiconductor industries. The pressurized barrier fluid helps prevent process fluid leakage and maintains the integrity of the sealed system.
Difference Between Back-to-Back and Face-to-Face Seals
Seal Face Orientation
The primary difference between back-to-back and face-to-face seals lies in the orientation of their seal faces. In back-to-back seals, the seal faces are arranged in opposite directions, facing away from each other. Conversely, face-to-face seals have their seal faces oriented towards each other, with the sealing surfaces in direct contact.
Mounting Arrangement
Back-to-back seals are typically mounted within a gland or housing, with the seal faces pressed against the gland walls. This arrangement allows for a more compact and space-efficient design. Face-to-face seals, on the other hand, are mounted between two components, such as flanges or housings, with the seal faces directly contacting each other.
Pressure Handling
Back-to-back seals excel at handling higher pressures compared to face-to-face seals. The opposing orientation of the seal faces in back-to-back seals allows them to effectively distribute and balance the pressure forces, reducing the risk of seal failure. Face-to-face seals, while still capable of handling moderate pressures, may have limitations in high-pressure applications due to the direct contact between the seal faces.
Space Requirements
Back-to-back seals offer a more compact design, as they can be mounted within a single gland or housing. This space-saving feature makes them suitable for applications with limited installation space. Face-to-face seals, due to their mounting arrangement between two components, typically require more space for installation and operation.
Maintenance
The maintenance requirements for back-to-back and face-to-face seals differ. Back-to-back seals often require less frequent maintenance, as the seal faces are protected within the gland or housing, reducing exposure to contaminants and wear. Face-to-face seals, with their directly contacting seal faces, may be more susceptible to wear and contamination, necessitating more frequent inspection and replacement.
Applications
Back-to-back seals find extensive use in high-pressure applications, such as hydraulic systems, pumps, and compressors. Their ability to handle higher pressures and their compact design make them well-suited for these demanding environments. Face-to-face seals are commonly employed in lower-pressure applications, such as fluid transfer systems, where their simpler mounting arrangement and direct seal face contact are advantageous.