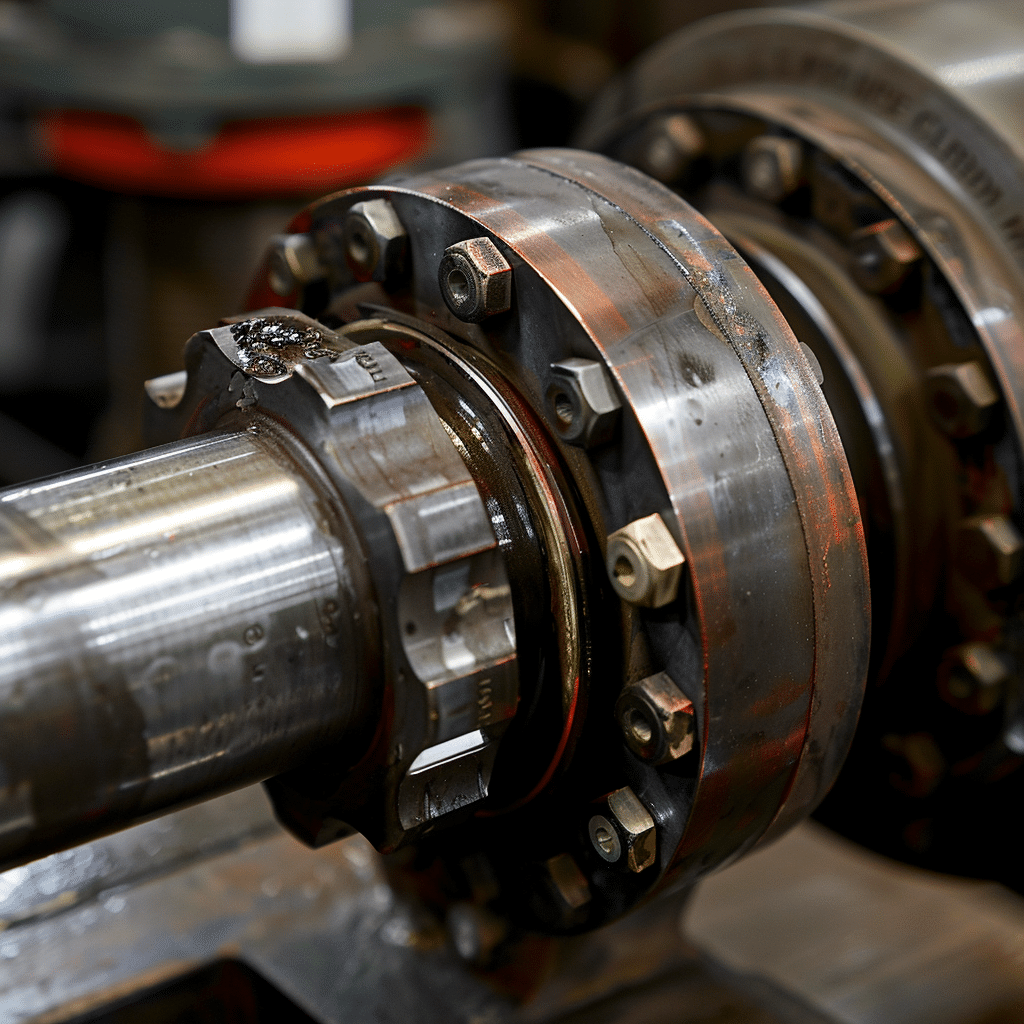
Mechanical Seal Flush Vs Quench
Mechanical Seal Flush Systems
Mechanical seal flush systems are designed to introduce a clean, compatible liquid into the seal chamber to cool, lubricate, and flush away any contaminants from the sealing faces. This helps to extend the life of the mechanical seal and prevent premature failure. Flush systems are commonly used in applications where the process fluid is dirty, abrasive, or not suitable for direct contact with the seal faces.
The flush fluid is typically introduced into the seal chamber at a pressure slightly higher than the process fluid to prevent process fluid from entering the seal chamber. The flow rate of the flush fluid is carefully controlled to ensure adequate cooling and lubrication without causing excessive wear on the seal faces.
API Piping Plans for Flush Systems
The American Petroleum Institute (API) has established standard piping plans for mechanical seal flush systems. These plans specify the arrangement of piping, instrumentation, and controls for various flush configurations. Some common API piping plans for flush systems include:
- API Plan 11: A recirculation from the pump discharge through a flow control orifice to the seal chamber.
- API Plan 13: A flush from an external source, such as a clean water supply, through a flow control device to the seal chamber.
- API Plan 32: A flush from an external source, with a cyclone separator to remove particulates before the fluid enters the seal chamber.
Mechanical Seal Quench Systems
Mechanical seal quench systems are used to introduce a barrier fluid, typically a gas, into the atmospheric side of the seal faces. The purpose of a quench system is to prevent the process fluid from escaping to the atmosphere and to provide a clean environment for the atmospheric side of the seal.
In a quench system, the barrier fluid is maintained at a pressure higher than the atmospheric pressure but lower than the process fluid pressure. This creates a differential pressure across the seal faces, preventing process fluid from leaking out while also preventing the ingress of atmospheric contaminants.
Quench systems are commonly used in applications where the process fluid is hazardous, toxic, or flammable, and where emissions must be minimized to comply with environmental regulations.
API Piping Plans for Quench Systems
API has also established standard piping plans for mechanical seal quench systems. Some common API piping plans for quench systems include:
- API Plan 51: A quench with a clean, non-pressurized fluid, such as steam condensate or nitrogen, vented to a safe location.
- API Plan 62: A quench with a clean, pressurized gas, such as nitrogen, supplied from an external source and vented to a safe location.
- API Plan 65A: A quench with a clean, pressurized liquid, such as glycol, supplied from an external source and vented to a safe location.
When to Select Mechanical Seal Flush
A mechanical seal flush system should be selected when:
- The process fluid is dirty, abrasive, or not suitable for direct contact with the seal faces.
- The process fluid has poor lubricating properties, and additional lubrication is required to prevent premature seal wear.
- The process fluid temperature is high, and additional cooling is needed to prevent thermal damage to the seal faces.
- The process fluid tends to crystallize or solidify at the seal faces, requiring continuous flushing to prevent buildup.
When to Select Mechanical Seal Quench
A mechanical seal quench system should be selected when:
- The process fluid is hazardous, toxic, or flammable, and emissions must be minimized to comply with environmental regulations.
- The process fluid tends to react with atmospheric moisture or oxygen, causing corrosion or other problems on the atmospheric side of the seal.
- The sealing environment requires a clean, inert barrier fluid to prevent contamination or reactions with the process fluid.
- The process fluid has a high vapor pressure, and a quench system is needed to prevent the formation of a vapor film between the seal faces.
FAQs
Can Flush and Quench Be Used Together?
Yes, in some cases, both a flush and a quench system may be used together on the same mechanical seal. This configuration is known as a double flush or tandem seal arrangement. The flush system is used to cool and lubricate the process side of the seal, while the quench system provides a barrier fluid on the atmospheric side of the seal. This combination offers enhanced protection against process fluid leakage and helps to extend seal life in challenging applications.
What Is the Water Quality for Mechanical Seal Flush?
The water quality for a mechanical seal flush system should be clean, free of particulates, and chemically compatible with the seal materials and the process fluid. In general, the flush fluid should meet the following criteria:
- Filtration: The flush fluid should be filtered to remove particles larger than 10-25 microns, depending on the specific seal design and application.
- Hardness: The flush fluid should have a low total hardness, typically less than 50 ppm as calcium carbonate (CaCO3), to prevent the formation of scale deposits on the seal faces.
- PH: The flush fluid should have a neutral to slightly alkaline pH, typically between 7.0 and 9.5, to minimize corrosion and ensure compatibility with seal materials.
- Chloride content: The flush fluid should have a low chloride content, typically less than 50 ppm, to minimize the risk of stress corrosion cracking in stainless steel seal components.
How Much Water Is Required for a Mechanical Seal Flush?
In general, the flush flow rate should be sufficient to maintain a minimum velocity of 1-2 ft/s (0.3-0.6 m/s) through the seal chamber to ensure adequate cooling and flushing action.
A common rule of thumb for estimating the required flush flow rate is to provide 0.25-0.5 gpm per inch of seal size (2-4 liters/min per 25 mm of seal size). For example, a 2-inch (50 mm) mechanical seal would typically require a flush flow rate of 0.5-1 gpm (4-8 liters/min).