Mechanical seals are critical components in many industrial machines, preventing leaks and ensuring optimal performance. While lubricating these seals can extend their lifespan and improve efficiency in certain situations, it’s not always necessary or recommended.
In this blog post, we’ll explore when oiling mechanical seals is beneficial, situations where it should be avoided, the types of lubricants best suited for the task, and best practices for proper lubrication. By understanding these key aspects, maintenance professionals can make informed decisions to optimize seal performance and longevity.
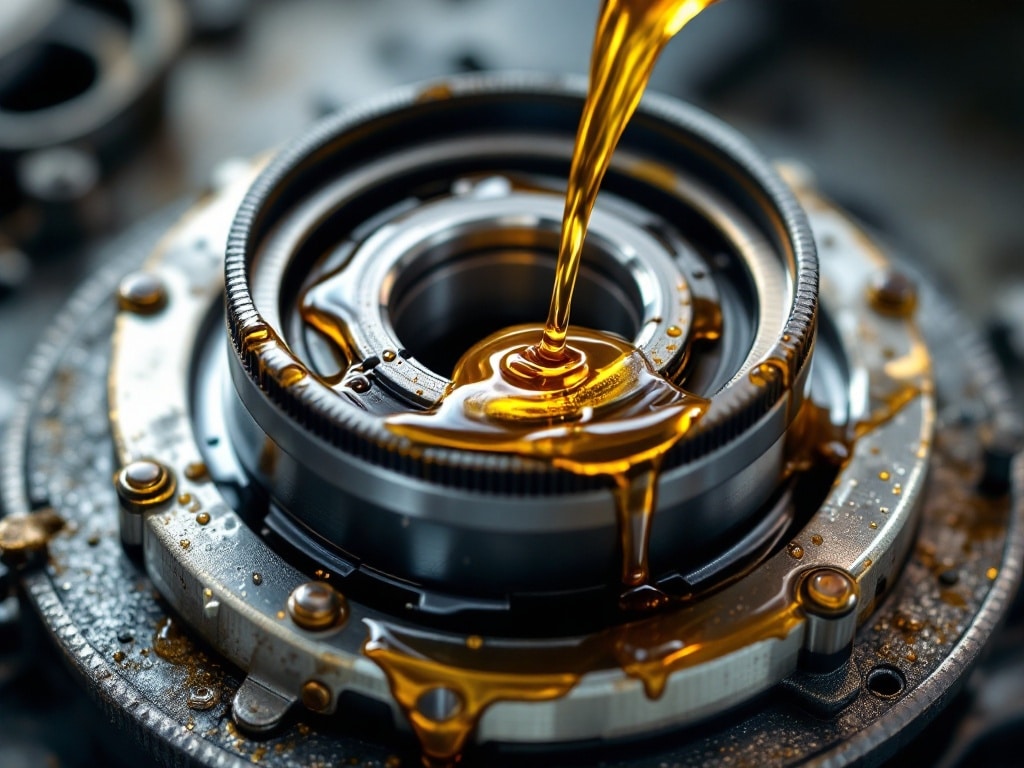
When Oiling is Necessary
High-Temperature Applications
In mechanical seals operating under high-temperature conditions, lubricating the seal faces becomes necessary to prevent excessive wear and heat generation. The lubricant helps to dissipate heat and reduce friction between the rotating and stationary seal faces, thereby extending the seal life and maintaining optimal performance.
Dry-Running Conditions
Mechanical seals that operate in dry-running conditions, such as those found in mixers, agitators, and some pumps, require lubrication to prevent damage to the seal faces. Without proper lubrication, the seal faces can quickly overheat and fail, leading to leakage and equipment downtime.
Abrasive or Corrosive Media
When handling abrasive or corrosive media, lubricating the mechanical seal is often necessary to protect the seal faces from damage. The lubricant forms a protective barrier between the seal faces and the media, reducing wear and corrosion while ensuring proper sealing.
Intermittent Operation
Mechanical seals subject to frequent starts and stops or intermittent operation may require lubrication to prevent dry-running during startup. Lubricating the seal faces helps to establish a fluid film between the faces, reducing wear and ensuring smooth operation.
When Oiling is Not Recommended
Standard Operating Conditions
In most standard operating conditions, mechanical seals are designed to run without additional lubrication. The sealed fluid itself acts as a lubricant, creating a thin fluid film between the seal faces that prevents direct contact and minimizes wear.
Contamination Concerns
Introducing lubricants to a mechanical seal can potentially lead to contamination of the sealed fluid. In applications where product purity is critical, such as in the food, beverage, or pharmaceutical industries, oiling the mechanical seal is not recommended to avoid contamination risks.
Incompatible Materials
Some lubricants may not be compatible with the materials used in the mechanical seal or the sealed fluid. Using incompatible lubricants can cause seal face damage, swell elastomers, or degrade the sealed fluid, leading to premature seal failure and leakage.
Sufficient Lubrication from Sealed Fluid
When the sealed fluid has adequate lubricating properties, additional oiling of the mechanical seal is unnecessary. In these cases, the sealed fluid itself provides sufficient lubrication to the seal faces, ensuring optimal performance and seal life.
Types of Lubricants for Mechanical Seals
Mineral Oil-Based Lubricants
Mineral oil-based lubricants are commonly used for lubricating mechanical seals due to their excellent compatibility with most elastomers and their ability to provide adequate lubrication at a reasonable cost. These lubricants are derived from refined crude oil and are available in various viscosities to suit different applications. They offer good stability, water resistance, and protection against wear and corrosion.
Synthetic Lubricants
Synthetic lubricants, such as polyalphaolefin (PAO) and polyalkylene glycol (PAG), are designed to provide superior performance compared to mineral oil-based lubricants. They offer enhanced thermal and oxidative stability, allowing them to maintain their properties at higher temperatures. Synthetic lubricants also provide excellent lubricity, reducing friction and wear on the mechanical seal faces. However, they may not be compatible with all seal materials, so it is important to consult the seal manufacturer’s recommendations before use.
Silicone-Based Lubricants
Silicone-based lubricants are known for their excellent thermal stability and compatibility with a wide range of elastomers. They are particularly useful in applications where the mechanical seal is exposed to extreme temperatures or aggressive chemicals. Silicone lubricants provide good lubricity and are resistant to oxidation and water contamination. However, they may not be suitable for use with certain plastics or painted surfaces, as they can cause swelling or softening.
Food-Grade Lubricants
In applications where the mechanical seal is used in food processing or pharmaceutical equipment, food-grade lubricants must be used to ensure compliance with industry regulations. These lubricants are typically based on synthetic or vegetable oils and are formulated to meet the stringent requirements of the FDA (Food and Drug Administration) or other relevant authorities. Food-grade lubricants are non-toxic, odorless, and tasteless, ensuring that they do not contaminate the products being processed.
Best Practices for Lubricating Mechanical Seals
Consult the Manufacturer’s Recommendations
Before lubricating a mechanical seal, it is crucial to consult the manufacturer’s recommendations. The manufacturer will provide guidance on the type of lubricant compatible with the seal materials, as well as the recommended viscosity and application method. Following these recommendations ensures optimal seal performance and longevity.
Ensure Proper Lubrication Quantity
Applying the correct amount of lubricant is essential for proper mechanical seal function. Overlubrication can lead to excess heat generation and seal failure, while underlubrication can result in increased friction and wear. The manufacturer’s guidelines should be followed closely to determine the appropriate lubrication quantity for each specific seal design.
Maintain Lubricant Cleanliness
Contamination of the lubricant can severely impact the performance and lifespan of a mechanical seal. Dirt, debris, and other contaminants can cause abrasive wear on the seal faces, leading to premature failure. When lubricating a mechanical seal, ensure that the lubricant is clean and free from any contamination. Use filtered lubricants and clean application tools to minimize the risk of introducing contaminants into the system.
Regularly Monitor and Maintain Lubrication
Regular monitoring and maintenance of the mechanical seal lubrication are essential for optimal performance. Periodically inspect the seal for signs of leakage, damage, or excessive wear. If the lubricant appears contaminated or degraded, it should be replaced with fresh lubricant. Establishing a lubrication maintenance schedule based on the manufacturer’s recommendations and the specific operating conditions of the equipment can help extend the life of the mechanical seal and prevent unexpected failures.