Mechanical seals are critical components in centrifugal pumps, preventing leaks and ensuring reliable operation. However, with the wide range of seal types available, selecting the optimal seal for a specific application can be a challenge. Choosing the wrong seal can lead to reduced performance, increased maintenance costs, and unexpected downtime.
In this blog post, we will explore the different types of mechanical seals for centrifugal pumps, helping you make an informed decision for your industrial needs.
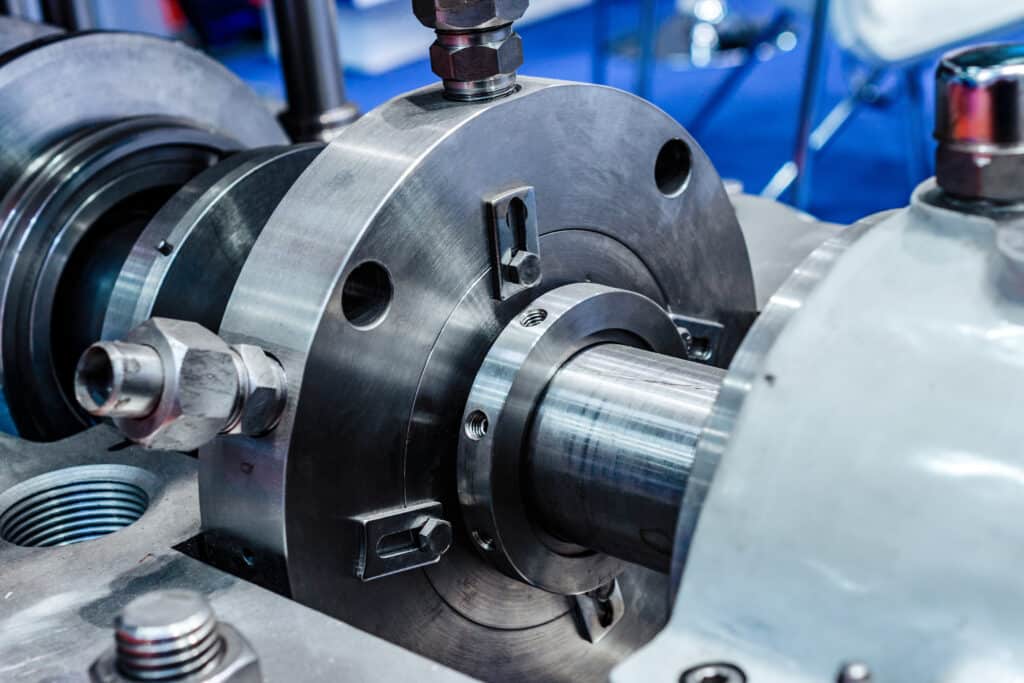
Based on Spring Mechanism
Single Spring Mechanical Seals
Single spring mechanical seals utilize a single spring to maintain the contact pressure between the rotating and stationary seal faces. The spring is typically located behind the rotating seal face, applying a constant force to keep the faces in contact. Single spring seals are suitable for general-purpose applications with moderate pressure and temperature requirements.
Multi-Spring Mechanical Seals
Multi-spring mechanical seals employ multiple springs, usually arranged in a circular pattern, to provide even pressure distribution across the seal faces. The use of multiple springs ensures better stability and alignment compared to single spring designs. Multi-spring seals can handle higher pressures and are less susceptible to vibration and shaft misalignment.
Wave Spring Mechanical Seals
Wave spring mechanical seals feature a wavy or sinusoidal-shaped spring that applies pressure to the seal faces. The wave spring design allows for a more compact seal assembly while providing consistent contact pressure. Wave spring seals are often used in applications with limited space and can accommodate moderate to high pressures.
Conical Spring Mechanical Seals
Conical spring mechanical seals incorporate a conical-shaped spring that exerts pressure on the seal faces. The conical design provides a progressive increase in contact pressure as the spring is compressed, resulting in better sealing performance under varying conditions. Conical spring seals are well-suited for high-pressure applications and can compensate for thermal expansion and contraction.
Based on Balancing Features
Balanced and Unbalanced Seals
Mechanical seals can be classified as balanced or unbalanced based on their design and pressure distribution across the seal faces.
Unbalanced seals have the full system pressure acting on the backside of the rotating seal face, resulting in higher contact pressure and increased wear.
Balanced seals incorporate a stepped or tapered design that reduces the effective pressure on the seal faces, leading to lower contact pressure, reduced friction, and extended seal life. Balanced seals are preferred for high-pressure applications and when energy efficiency is a concern.
Based on Secondary Seal and Drive Mechanism
Pusher and Non-Pusher Seals
Pusher seals have a secondary seal, typically an O-ring or V-ring, that moves axially with the primary seal face. The secondary seal “pushes” the primary seal face against the stationary face, maintaining contact pressure.
Non-pusher seals, also known as bellows seals, utilize a flexible bellows element to provide the axial movement and sealing force without the need for a dynamic secondary seal.
Conventional Seals
Conventional mechanical seals consist of separate components that are assembled and installed individually. They require careful alignment and adjustment during installation to ensure proper operation. Conventional seals offer flexibility in terms of material selection and can be customized for specific applications. However, they may be more prone to installation errors and require more maintenance compared to other seal types.
Cartridge Seals
Cartridge seals are pre-assembled units that contain all the necessary seal components, including the seal faces, springs, and secondary seals, within a single cartridge. They are designed for easy installation and removal, reducing the risk of incorrect assembly and alignment issues. Cartridge seals are widely used in various industries due to their reliability, standardized design, and simplified maintenance procedures.
Factors to Consider When Choosing a Mechanical Seal
Type of Fluid
For chemically aggressive or corrosive fluids, seal faces and secondary sealing elements must be constructed from compatible materials that can withstand attack. Fluids with abrasive particles necessitate hard face materials like silicon carbide to resist wear and maintain a tight seal.
Fluids that tend to crystallize or leave deposits require consideration of features like enlarged flow paths and flush ports to prevent clogging. For high purity applications, seals with low friction, non-contacting faces are preferred to minimize heat generation and particulate contamination of the fluid.
Fluid Pressure
Higher pressures generally require more robust seal face materials, stronger springs, and improved cooling and lubrication at the sealing interface.
Unbalanced seals are typically limited to lower pressure applications, while balanced seal designs allow for reliable operation at higher pressures by reducing hydraulic loading on the seal faces. For very high pressures, double seals with a barrier fluid maintained at a higher pressure than the pumpage may be necessary.
Temperature
Elastomers used in secondary seals must remain flexible and chemically resistant at the expected operating temperature.
At elevated temperatures, seal faces require special features like thermal insulating sleeves, heat-dissipating face materials, and internal flow modifiers to prevent heat buildup and maintain lubrication. Extremely high or low temperatures may necessitate the use of component or cartridge seals with cooling jackets or heat exchangers to maintain acceptable operating conditions at the seal faces.