Seal chambers and stuffing boxes are two essential components in rotating equipment that serve to prevent fluid leakage and protect the shaft and bearings. While both are designed to control leakage around a shaft, they differ in their design, sealing method, functionality, maintenance requirements, cost, and optimal applications.
In this article, we will dive deep into the key differences between seal chambers and stuffing boxes, exploring their unique characteristics, advantages, and limitations across various dimensions. By the end, you’ll have a thorough understanding of when and why to use each type of shaft sealing solution in different machinery contexts.
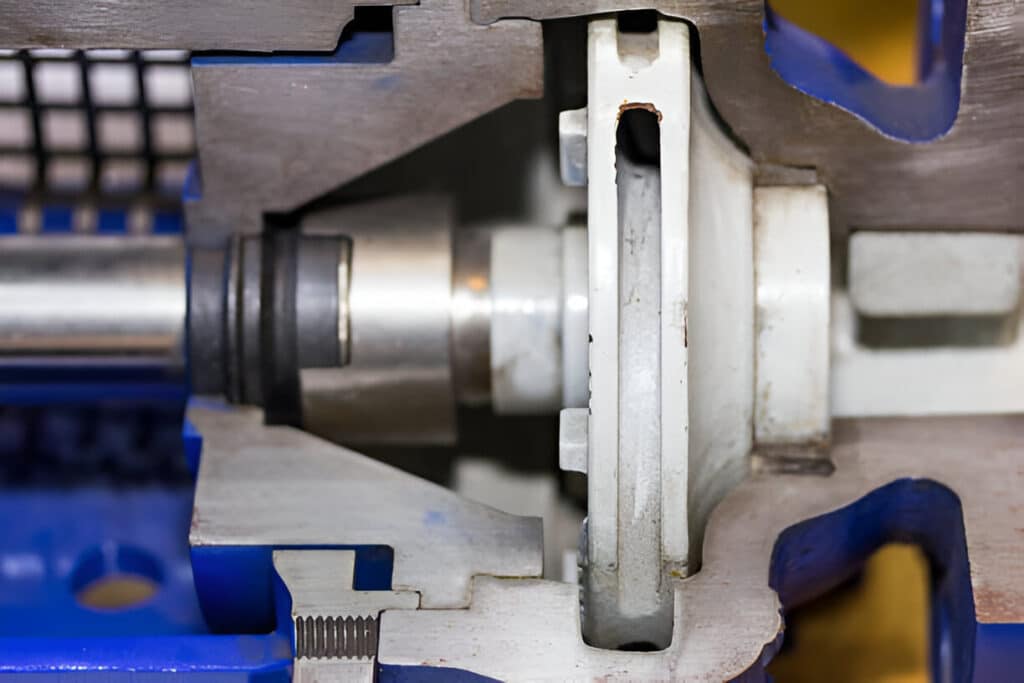
What Is a Seal Chamber
A seal chamber, also known as a stuffing box, is an integral component of a pump that houses the sealing system. Its primary purpose is to prevent the pumped fluid from escaping the pump casing while also preventing external contaminants from entering the pump.
The seal chamber is typically located where the pump shaft enters the pump casing. It provides a controlled environment for the sealing system, which can consist of various types of seals such as mechanical seals, packing, or lip seals.
Imagine the seal chamber as a protective barrier between the inside and outside of the pump. Just like how a submarine needs a watertight door to keep the water out and the air in, the seal chamber acts as a barrier to keep the pumped fluid inside the pump and contaminants out.
Functions of Seal Chambers
The seal chamber in a pump serves several important functions:
- Housing the mechanical seal: The primary purpose of the seal chamber is to provide a secure and stable environment for the mechanical seal. The chamber is designed to accommodate the seal components, ensuring they remain properly aligned and protected during pump operation.
- Lubricating the seal faces: The seal chamber is filled with a lubricating fluid, typically the pumped liquid or a compatible barrier fluid. This fluid lubricates the seal faces, reducing friction and wear, which helps extend the life of the mechanical seal.
- Cooling the seal: The lubricating fluid in the seal chamber also acts as a coolant, dissipating heat generated by the friction between the seal faces. Effective cooling prevents overheating and premature failure of the seal components.
- Maintaining pressure: The seal chamber is designed to maintain a consistent pressure environment for the mechanical seal. This pressure is usually slightly higher than the pump’s discharge pressure, preventing process fluid from entering the seal chamber and causing contamination or damage to the seal.
Components of a Seal Chamber
A typical seal chamber consists of the following components:
- Gland plate: The gland plate is the main body of the seal chamber, which is bolted to the pump housing. It provides a mounting surface for the stationary seal components and forms the outer boundary of the seal chamber.
- Throttle bushing: The throttle bushing is a cylindrical component that fits around the pump shaft and helps regulate the flow of lubricating fluid into and out of the seal chamber. It also helps maintain the proper pressure within the chamber.
- Seal chamber cover: The seal chamber cover is a removable component that allows access to the seal chamber for installation, maintenance, and replacement of the mechanical seal. It is typically secured to the gland plate using bolts or studs.
- Seal chamber ports: The seal chamber is equipped with ports for introducing and evacuating lubricating fluid. These ports may include fluid inlet, outlet, and recirculation connections, depending on the specific design and application.
Types of Seals Used in Seal Chambers
Single Mechanical Seals
Single mechanical seals are the most common type of seal used in seal chambers. They consist of a stationary seal face (usually made of a hard material like silicon carbide) and a rotating seal face (typically made of a softer material like carbon). The seal faces are pressed together by springs and hydraulic pressure, creating a tight seal that prevents leakage.
Double Mechanical Seals
Double mechanical seals provide an extra level of protection against leakage and are often used in applications involving hazardous or toxic fluids. They feature two sets of seal faces, with a barrier fluid circulated between them. The barrier fluid is maintained at a higher pressure than the pumped fluid, ensuring that any leakage flows from the barrier fluid into the process fluid, rather than the other way around.
Cartridge Seals
Cartridge seals are pre-assembled units that combine the mechanical seal components and gland plate into a single, easy-to-install package. They are designed to simplify seal installation and replacement, reducing downtime and maintenance costs.