Mechanical seals are essential components in rotary equipment, preventing fluid leakage and ensuring efficient operation. Among the various seal arrangements, the face-to-face configuration offers unique advantages and considerations.
This post will explore the face-to-face mechanical seal arrangement in depth, including its definition, key benefits, potential drawbacks, and common applications across industries. By understanding the characteristics of this seal configuration, engineers and maintenance professionals can make informed decisions when designing or maintaining critical equipment.
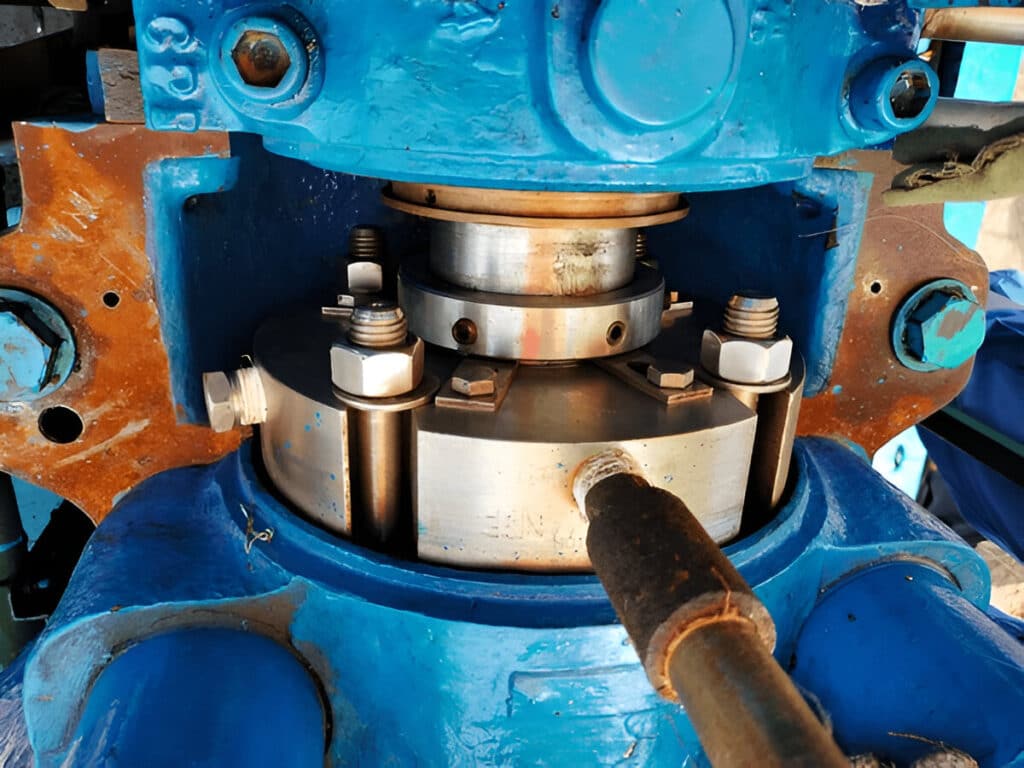
What Is Face-to-Face Arrangement
In the world of mechanical seals, face-to-face arrangement refers to a specific configuration where two mechanical seals are installed within the same seal chamber, with their sealing faces positioned facing each other.
To better understand how a face-to-face arrangement works, let’s break it down step by step. In a typical mechanical seal, there are two main components: a stationary part (usually the seal ring) and a rotating part (the mating ring). These two parts create a sealing interface that prevents fluid leakage. Now, imagine having two sets of these sealing components installed in a single seal chamber, with their sealing faces oriented towards each other. That’s essentially what a face-to-face arrangement looks like.
One key aspect of this configuration is the presence of a barrier fluid between the two seals. The barrier fluid is typically pressurized to a level higher than the process fluid, creating a positive pressure differential. This ensures that any leakage that might occur would be from the barrier fluid into the process, rather than the other way around. As a result, face-to-face arrangements offer an extra layer of protection against process fluid contamination and environmental emissions.
Advantages of Face-to-Face Arrangement
Increased Cooling Capacity
One key advantage of the face-to-face mechanical seal arrangement is its enhanced cooling capacity compared to other configurations. By positioning the seal faces opposite each other, this design allows for more effective heat dissipation. The increased surface area exposure enables the sealing fluid to absorb and carry away heat more efficiently.
Reduced Seal Face Deformation
The symmetric nature of the face-to-face arrangement helps to evenly distribute pressure across the seal faces. This balanced loading minimizes the potential for uneven deformation or distortion of the sealing surfaces. By maintaining a more consistent contact pattern between the faces, the face-to-face design promotes better sealing performance and longer seal life compared to arrangements where the faces are loaded asymmetrically.
Simplified Installation and Maintenance
Face-to-face mechanical seals offer advantages in terms of simplifying installation and maintenance procedures. The opposed configuration of the seal faces allows for easier alignment during assembly, as the faces naturally want to mate flush against each other. This self-aligning characteristic reduces the time and skill required for proper installation. Additionally, when maintenance or seal replacement is needed, the face-to-face arrangement facilitates quicker and more straightforward disassembly and reassembly processes.
Disadvantages of Face-to-Face Arrangement
Limited Space Requirements
The opposed configuration of the seal faces necessitates a larger overall seal envelope compared to other arrangements like back-to-back or tandem seals. The increased space demands can pose challenges in applications where equipment size or clearances are restricted.
Potential for Increased Leakage
Another drawback of face-to-face seals is the potential for higher leakage rates under certain conditions. If the sealing fluid pressure becomes greater than the closing force acting on the seal faces, it can cause the faces to separate slightly.
Applications of Face-to-Face Arrangement
High-Pressure Applications
Face-to-face mechanical seals are commonly used in high-pressure applications due to their excellent pressure handling capabilities. The opposed face configuration allows for robust sealing performance even under elevated pressures. Industries such as oil and gas, petrochemical, and power generation often utilize face-to-face seals in pumps, compressors, and other rotating equipment where high-pressure sealing is critical.
High-Temperature Environments
The enhanced cooling capacity of face-to-face seals also makes them advantageous in high-temperature applications. Industries like chemical processing, refining, and power generation often involve processes with elevated temperatures. Face-to-face seals can effectively manage the heat generated in these environments, helping to prevent premature seal failure and maintain reliable operation.
Rotating Equipment with Axial Space Constraints
In some rotating equipment designs, axial space is limited, making it challenging to accommodate certain seal arrangements. Face-to-face mechanical seals can be a viable solution in these situations. While they require increased radial space compared to other configurations, their axial space requirements are often more compact.