Mechanical seals are critical components in rotating equipment that prevent leakage and ensure optimal performance. To maintain proper functioning and extend the lifespan of these seals, a flush system is often employed.
In this blog post, we will dive into the specifics of mechanical seal flushes, exploring their purpose, types, operational principles, key components, and diverse applications across industries.
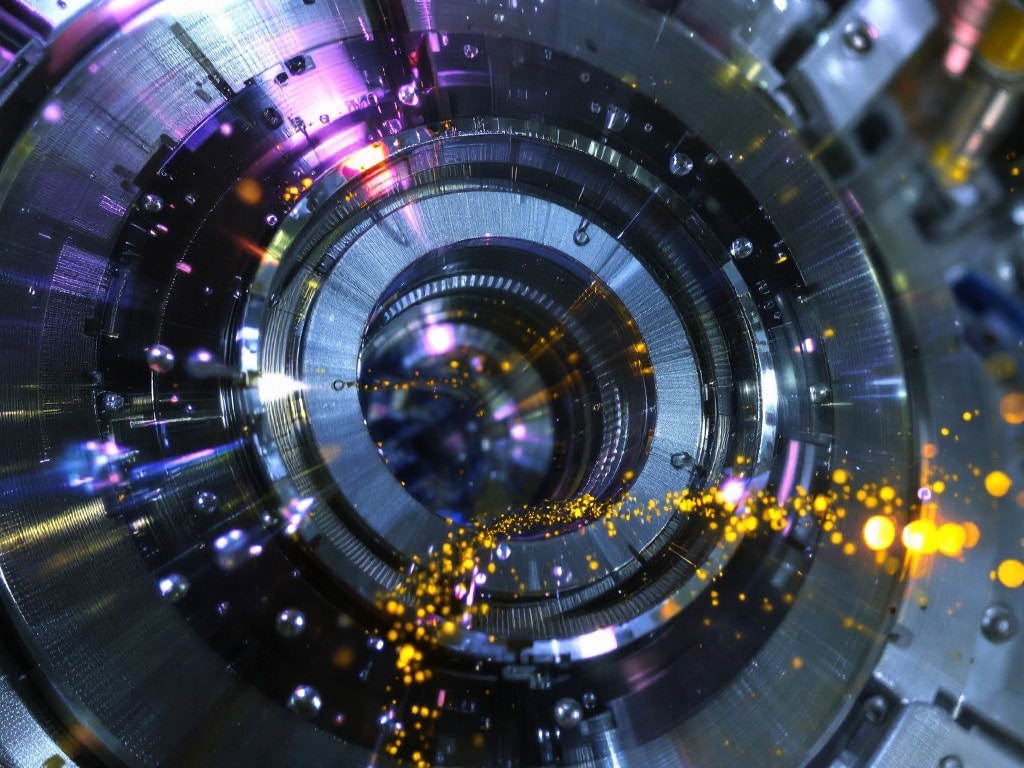
What Is Flush
In the context of mechanical seals, flush refers to the process of introducing a clean, compatible liquid into the seal chamber to cool, lubricate, and clean the sealing surfaces. The flush liquid is typically pumped from an external source and circulated through the seal chamber before being discharged or recirculated back to the source.
Purpose of Mechanical Seal Flush
The primary purposes of using a flush in mechanical seals include:
- Cooling: The flush liquid helps dissipate heat generated by the friction between the rotating and stationary seal faces, preventing overheating and premature seal failure.
- Lubrication: The flush liquid provides lubrication to the sealing surfaces, reducing friction and wear, thereby extending the seal life.
- Cleaning: The flush helps prevent the accumulation of solids, debris, or process fluid on the sealing surfaces, which can cause abrasion, clogging, or seal failure.
- Pressure control: In some cases, the flush liquid is used to maintain a higher pressure in the seal chamber than the process fluid, preventing the ingress of contaminants into the seal.
Types of Mechanical Seal Flushes
There are two main types of mechanical seal flushes: single mechanical seal with flush and double mechanical seal with flush.
Single Mechanical Seal with Flush
A single mechanical seal with flush consists of one set of sealing surfaces (one rotating and one stationary face) and a flush port. The flush liquid is introduced into the seal chamber through the flush port, which is typically located on the gland plate or seal housing. The flush liquid flows across the sealing surfaces, providing cooling, lubrication, and cleaning before exiting the seal chamber.
Double Mechanical Seal with Flush
A double mechanical seal with flush features two sets of sealing surfaces (two rotating and two stationary faces) arranged in tandem. The space between the two seals, known as the buffer zone, is filled with a compatible barrier fluid, which is typically pressurized higher than the process fluid.
In this arrangement, the flush liquid is introduced into the buffer zone, providing cooling, lubrication, and cleaning to both sets of sealing surfaces. The flush liquid is then either discharged or recirculated back to the source. Double mechanical seals with flush offer enhanced sealing performance and are commonly used in applications involving hazardous, toxic, or environmentally sensitive fluids.
How Mechanical Seal Flush Works
In a mechanical seal flush system, a clean, cool liquid is introduced into the seal chamber to control the environment around the seal faces. The flush liquid enters the seal chamber at a pressure slightly higher than the pressure inside the pump or vessel. This positive pressure differential ensures that the flush liquid flows through the seal faces and prevents process fluid from entering the seal chamber.
As the flush liquid passes through the seal faces, it lubricates and cools the faces, reducing friction and heat generation. The flush also helps to carry away any debris or contaminants that may have accumulated on the seal faces, keeping them clean and free from damage.
The flush liquid then exits the seal chamber through a drain or vent, either returning to the flush system for recirculation or being discharged to a safe location. The continuous flow of flush liquid through the seal chamber helps to maintain a stable environment for the mechanical seal, extending its life and improving its performance.
Components of Flush
The main components of a mechanical seal flush system include:
- Flush liquid reservoir: A tank or container that holds the flush liquid, which is typically a clean, compatible fluid such as water, glycol, or oil.
- Flush liquid pump: A pump that circulates the flush liquid through the system and maintains the necessary pressure differential.
- Pressure regulating valve: A valve that controls the pressure of the flush liquid entering the seal chamber, ensuring it remains slightly higher than the process fluid pressure.
- Flow control valve: A valve that regulates the flow rate of the flush liquid through the seal chamber, optimizing lubrication and cooling.
- Piping and fittings: The network of pipes, hoses, and connectors that carry the flush liquid to and from the seal chamber.
- Heat exchanger (optional): A device that cools the flush liquid before it enters the seal chamber, helping to maintain a stable temperature.
- Filtration system (optional): A system that removes contaminants from the flush liquid, ensuring it remains clean and effective.
Applications of Flush
Chemical Processing
In chemical processing plants, mechanical seals are often exposed to harsh, corrosive, or toxic fluids. Flush systems help to protect the seals by providing a clean, compatible barrier fluid that prevents direct contact between the seal faces and the process fluid.
Pharmaceutical Manufacturing
Pharmaceutical manufacturing requires strict control over the purity and quality of the products. Mechanical seal flush systems help to maintain a sterile environment by preventing contamination of the process fluid and ensuring the seal faces remain clean and debris-free.
Food and Beverage Production
In food and beverage production, mechanical seals must be kept free from contamination to ensure product safety and quality. Flush systems provide a clean, food-grade lubricant that helps to maintain seal cleanliness and prevent the ingress of bacteria or other contaminants.
Oil and Gas Industry
In the oil and gas industry, mechanical seals are subjected to high pressures, extreme temperatures, and abrasive fluids. Flush systems help to cool and lubricate the seal faces, extending their life and preventing premature failure in these demanding conditions.
Power Generation
Power generation plants rely on mechanical seals to contain and control the flow of steam, water, and other fluids. Flush systems help to maintain the integrity of these seals, ensuring reliable operation and minimizing downtime.