Cartridge seals and lip seals are two distinct types of sealing solutions commonly employed in rotating equipment across various industries. While both serve to prevent leakage and contamination, they differ in their design, materials, and application suitability.
Cartridge seals offer a pre-assembled, self-contained sealing unit that combines multiple components, whereas lip seals consist of a flexible sealing element that creates a barrier against the shaft surface. This blog post will delve into the intricacies of these sealing technologies, examining their unique characteristics, performance capabilities, and typical use cases in industrial machinery.
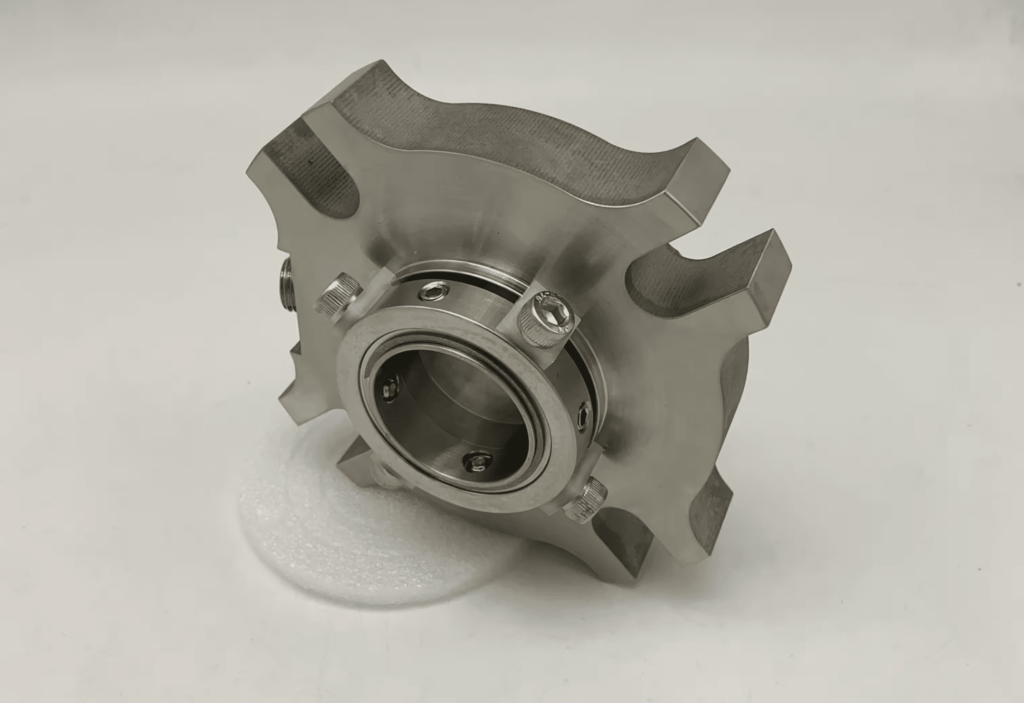
What Are Cartridge Seals
Cartridge seals, also known as cartridge mechanical seals, are a type of mechanical seal designed as a pre-assembled unit. This complete seal assembly consists of a stationary seat, a rotating seal ring, secondary seals, and a gland plate, all combined into a single cartridge unit. The arrangement of seal components within the cartridge simplifies installation and reduces assembly time compared to component seals.
Cartridge seals are commonly used in pumps and other rotating equipment to prevent fluid leakage along the rotating shaft. They provide a reliable sealing solution for a wide range of applications, including water, oil, and chemical processing industries. The design of cartridge seals allows for easier maintenance and replacement, as the entire unit can be swapped out without disassembling the equipment.
One advantage of cartridge seals is their versatility. They can be configured as single seals, double seals, or tandem seals, depending on the application requirements. Single cartridge seals consist of one set of sealing faces, while double seals have two sets of sealing faces with a buffer fluid between them for added safety and reliability. Tandem seals, on the other hand, have two seals mounted back-to-back, providing redundancy in case of primary seal failure.
What Are Lip Seals
Lip seals, also known as oil seals or rotary shaft seals, are a type of seal commonly used to prevent leakage of fluids or gases in rotating equipment. They consist of a flexible lip or multiple lips made from elastomeric materials, such as nitrile rubber or fluoroelastomers, that press against the rotating shaft to create a sealing effect.
The primary function of lip seals is to retain lubricants, such as oil or grease, within a bearing chamber while preventing the ingress of contaminants from the external environment. Lip seals are often used in applications with relatively low pressure and speed, such as gearboxes, pumps, and motors.
The sealing action of lip seals relies on the elastomeric lip maintaining contact with the rotating shaft. The lip is typically molded with a garter spring or other type of spring to maintain a constant sealing force against the shaft. As the shaft rotates, the lip flexes and accommodates any shaft misalignment or eccentricity, ensuring a continuous sealing interface.
Lip seals are available in various designs and configurations to suit different application requirements. Some common types of lip seals include:
- Single-lip seals: These have one sealing lip that contacts the shaft and are suitable for most general-purpose applications.
- Double-lip seals: These have two sealing lips, providing an additional barrier against leakage and improved sealing performance in more demanding conditions.
- Cassette seals: These are pre-assembled units that combine a lip seal with a bearing or other components, simplifying installation and maintenance.
- V-ring seals: These have a V-shaped cross-section and are designed to seal against the shaft and the housing bore, providing both radial and axial sealing.
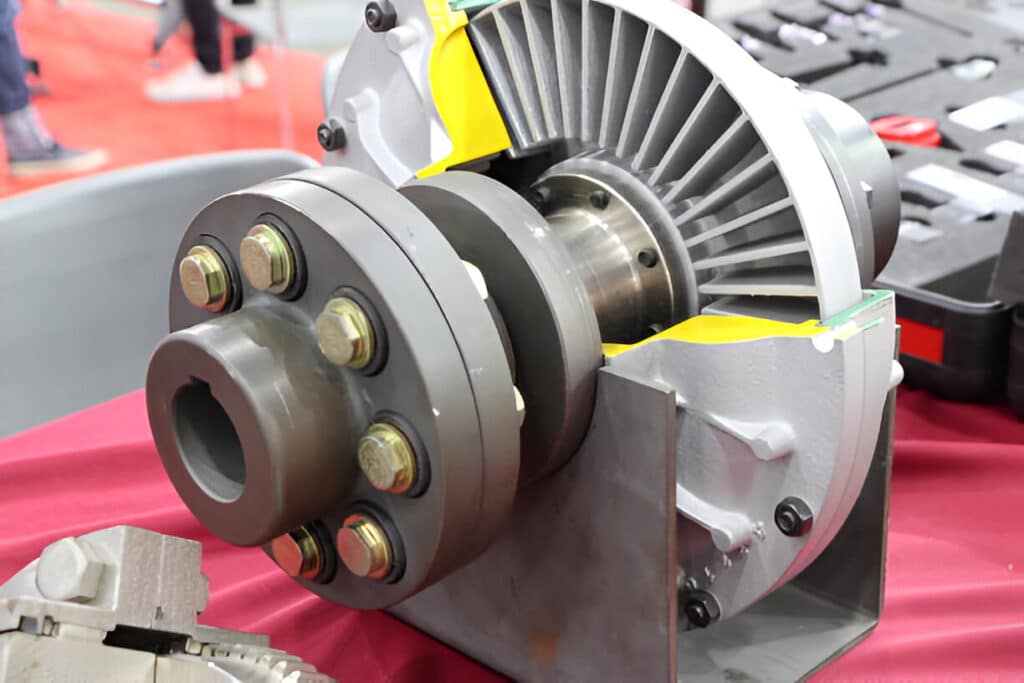
Key Differences Between Cartridge Seals and Lip Seals
Design and Structure
Cartridge seals are pre-assembled mechanical face seal units that consist of a stationary seat, rotating seal ring, secondary seals, and a gland plate. The arrangement of seal components is housed within a cartridge unit, making it a complete seal assembly.
In contrast, lip seals are a type of rotary shaft seal that feature a flexible sealing element, typically an elastomer or PTFE, with one or more sealing lips that contact the shaft surface.
Installation and Maintenance
The installation process for cartridge seals is generally more straightforward compared to non-cartridge mechanical seals. Cartridge seal units are pre-assembled and factory-tested, reducing assembly time and minimizing the possibility of incorrect installation. This ease of installation translates to reduced maintenance downtime.
Lip seals, on the other hand, require careful installation to ensure proper alignment and seal tension. They may need more frequent replacement due to wear on the sealing lips over time.
Applications
Cartridge seals find widespread use in a range of pumps, mixers, and other rotating equipment, handling various fluids, including thin, non-lubricating liquids. They are suitable for applications requiring reliable operation and minimal leakage.
Lip seals are commonly employed in equipment such as gearboxes, bearing chambers, and other machinery where effective sealing of lubricants or exclusion of contaminants is necessary. They are often used in automotive water-pump seal cartridges and earth-moving equipment.
Cost Considerations
The initial cost of cartridge seals is typically higher compared to lip seals due to their more complex design and pre-assembled nature. However, the enhanced performance and reliability of cartridge seals can result in long-term cost savings through reduced maintenance, fewer seal replacements, and minimized downtime.
Lip seals offer a more economical sealing solution upfront but may incur higher replacement and maintenance costs over time.
Performance and Reliability
Cartridge seals provide superior performance and reliability in demanding applications. The pre-assembled design ensures proper alignment and seal face materials selection, reducing the risk of premature failure. Cartridge seals can effectively handle higher pressures, temperatures, and a wider range of fluids compared to lip seals. They also offer better leakage control and extended seal life.
Lip seals, while reliable for certain applications, may be more prone to leakage and wear, especially in challenging conditions or when exposed to aggressive media.