Double mechanical seals are widely used in rotating equipment like pumps and compressors to prevent fluid leakage. While simple in concept, they are comprised of several critical elements that work together as a system.
This article will explore the key components of a typical double mechanical seal, including the seal arrangements, faces, gland, sleeve, flush system, barrier fluid, elastomers, and hardware. By understanding the role and design considerations for each part, readers will gain a deeper appreciation for these intricate sealing solutions.
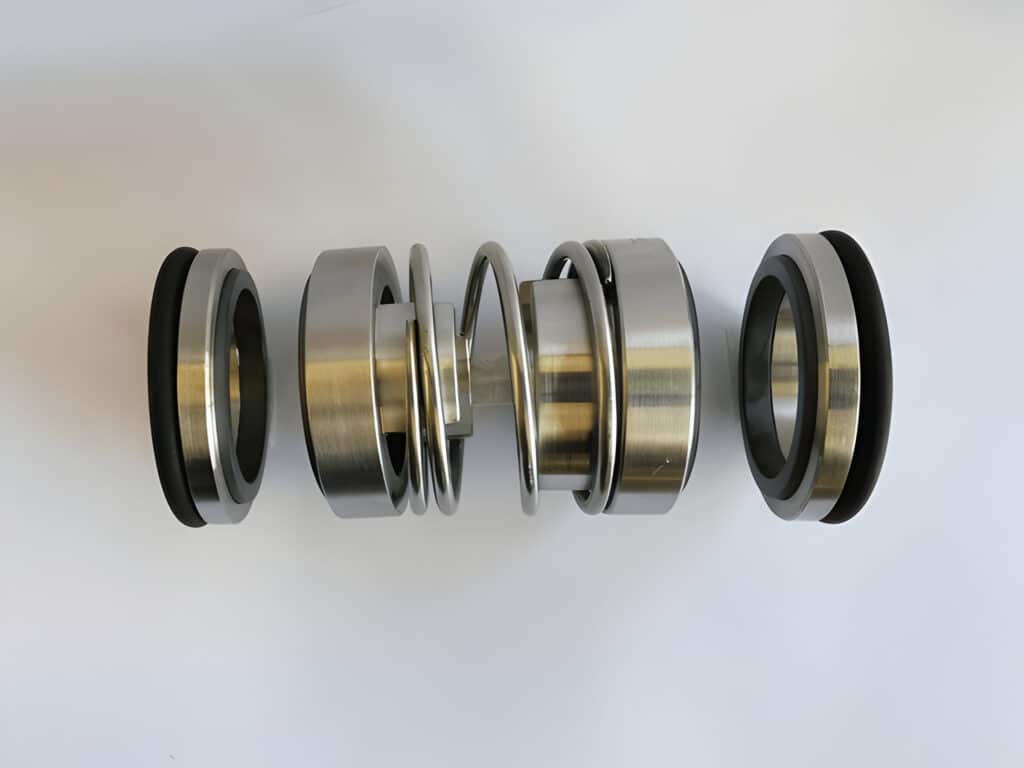
Seal Arrangements
Double mechanical seals can be configured in three primary arrangements: back-to-back, face-to-face, and tandem.
Back-to-Back
In a back-to-back arrangement, the two seals are mounted with their rotating faces oriented away from each other. The barrier or buffer fluid is introduced between the seals, with the pressure maintained higher than the process fluid pressure. This arrangement is ideal for high-pressure applications and prevents process fluid from entering the barrier/buffer fluid system.
Face-to-Face
Face-to-face arrangements have the rotating faces of the two seals oriented towards each other. The barrier or buffer fluid is maintained at a lower pressure than the process fluid. This configuration is suitable for low-pressure applications and allows for easy monitoring of the barrier/buffer fluid system for leakage.
Tandem
Tandem seal arrangements feature two seals mounted with their rotating faces in the same direction. The barrier or buffer fluid is introduced between the seals, with the pressure typically maintained at a lower level than the process fluid pressure. Tandem seals provide an additional layer of protection against leakage and are often used in environmentally sensitive or hazardous applications.
Components of a Double Mechanical Seal
Seal Faces
The seal faces are the primary sealing elements in a double mechanical seal. They consist of two parts: the primary seal and the secondary seal.
Primary Seal
The primary seal, also known as the inboard seal, is the first line of defense against leakage. It is typically made of a hard, wear-resistant material such as silicon carbide, tungsten carbide, or ceramic. The primary seal faces are precisely lapped to create a smooth, flat surface that allows them to mate together with minimal leakage.
The primary seal faces are held in place by a combination of spring pressure and hydraulic force from the sealed fluid. As the sealed fluid pressure increases, the hydraulic force on the seal faces increases, causing them to close more tightly and prevent leakage.
Secondary Seal
The secondary seal, also known as the outboard seal, is the backup sealing element in a double mechanical seal. It is typically made of the same materials as the primary seal and serves as a redundant sealing point in case the primary seal fails.
The secondary seal faces are not in direct contact with the sealed fluid and are therefore not subject to the same wear and tear as the primary seal faces. However, they are still exposed to the environment and must be resistant to corrosion, temperature fluctuations, and other environmental factors.
Seal Gland
The seal gland is the housing that contains the mechanical seal components. It is typically made of a corrosion-resistant material such as stainless steel or Hastelloy and is designed to withstand the pressure and temperature of the sealed fluid.
The seal gland provides a mounting surface for the seal faces, as well as ports for the introduction of flush fluids and barrier/buffer fluids. It also includes a drain port to allow any leakage that may occur to be safely removed from the system.
Shaft Sleeve
The shaft sleeve is a cylindrical component that fits over the shaft of the rotating equipment and provides a mounting surface for the seal gland. It is typically made of a hard, wear-resistant material such as stainless steel or tungsten carbide and is designed to protect the shaft from damage caused by the mechanical seal.
The shaft sleeve also plays a critical role in maintaining the proper alignment of the seal faces. Any misalignment or runout in the shaft can cause the seal faces to become misaligned, leading to increased leakage and premature failure of the seal.
Flush System
The flush system is a critical component of a double mechanical seal that helps to cool and lubricate the seal faces, as well as prevent the buildup of contaminants that can cause the seal to fail. The flush system consists of two parts: the primary seal flush and the secondary seal flush.
Primary Seal (Inboard)
The primary seal flush is used to cool and lubricate the primary seal faces. It is typically a clean, compatible fluid that is introduced into the seal gland through a port in the seal gland. The flush fluid flows across the primary seal faces, removing heat and contaminants before exiting through the drain port.
Secondary Seal (Outboard)
The secondary seal flush is used to cool and lubricate the secondary seal faces. It is typically the same fluid as the primary seal flush and is introduced into the seal gland through a separate port. The secondary seal flush flows across the secondary seal faces before exiting through the drain port.
Barrier/Buffer Fluid System
The barrier/buffer fluid system is an additional component that may be used in double mechanical seals to provide an extra layer of protection against leakage. The barrier/buffer fluid is a clean, compatible fluid that is maintained at a higher pressure than the sealed fluid, creating a positive pressure differential across the seal faces.
The barrier/buffer fluid system consists of a reservoir, a pressure control valve, and a circulation pump. The reservoir holds a supply of the barrier/buffer fluid, while the pressure control valve maintains the fluid at a constant pressure. The circulation pump circulates the fluid through the seal gland, providing a continuous flow of clean, cool fluid across the seal faces.
Seal Elastomers
Seal elastomers are an essential component of double mechanical seals that provide static sealing between the various seal components. They are typically made of a flexible, resilient material such as fluoroelastomer (FKM), perfluoroelastomer (FFKM), or ethylene propylene diene monomer (EPDM) and are designed to withstand the pressure, temperature, and chemical compatibility requirements of the application.
Seal elastomers are used in a variety of locations within the mechanical seal, including:
- O-rings between the seal faces and the seal gland
- Gaskets between the seal gland and the equipment housing
- Bellows or diaphragms that provide axial movement of the seal faces
Seal Hardware
Seal hardware refers to the various mechanical components that hold the seal faces and other components in place within the seal gland. These components are typically made of a corrosion-resistant material such as stainless steel or Hastelloy and are designed to withstand the pressure and temperature of the sealed fluid.
Some common examples of seal hardware include:
- Springs that provide the necessary closing force on the seal faces
- Drive collars that transmit torque from the shaft to the seal faces
- Retaining rings that hold the seal components in place within the seal gland