Are you struggling with leaking or malfunctioning mechanical seals in your centrifugal pumps? Improper seal installation can lead to costly downtime, reduced efficiency, and even complete pump failure.
Our step-by-step guide will walk you through the process of correctly installing a mechanical seal in your centrifugal pump. From preparation to startup, we’ll cover every critical step to ensure a leak-free, efficient operation. With our expert tips and detailed instructions, you’ll have your pump back up and running in no time.
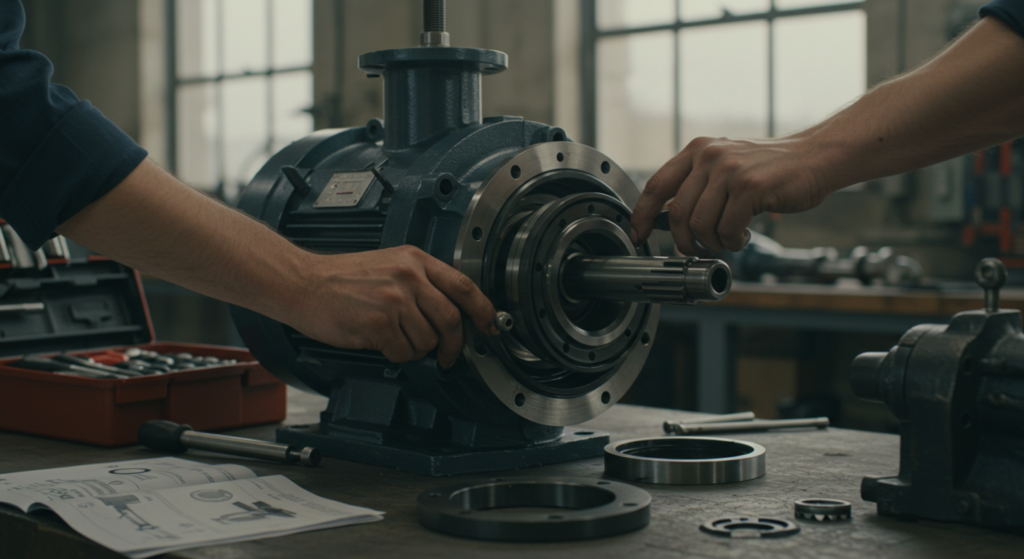
Step 1: Preparation
- Cut the power: The first step is to turn off the pump and completely disconnect it from its power source. This is a critical safety measure to prevent any accidental startup during the installation process.
- Isolate the fluid: Close both the inlet and outlet isolation valves to prevent fluid from entering or exiting the pump during the seal replacement. In cases where the pump does not have isolation valves, it may be necessary to drain the entire system to ensure a safe working environment.
- Drain the pump: Locate and remove the casing drain plug to allow any fluid remaining in the pump casing to drain out. Position a catch basin beneath the pump to collect this residual fluid, preventing any spills or messes in the work area.
Step 2: Disassembly
- Disconnect the pump from the motor and any outlet piping:
- For ‘back pull-out’ designs: Remove the spacer element in the pump coupling. This spacer connects the pump and motor shafts. Loosen the bolts that secure the casing to the pump frame. Carefully slide the back pull-out assembly (including the impeller, seal, and bearings) away from the casing.
- For non-back pull-out designs: Disconnect the coupling between the pump and motor shaft. Unbolt and disconnect the complete pump assembly from the piping and baseplate.
- For close-coupled designs: Remove the entire combined pump/motor unit from the piping and baseplate as a single assembly.
- Remove the casing: Completely remove the casing bolts that hold the casing to the pump frame. Carefully separate the casing from the rest of the pump assembly and set it aside.
- Remove the impeller: Depending on the specific pump design, the impeller may be threaded onto the shaft, keyed, or secured with a locking assembly. Remove any impeller locking hardware, such as locking screws, washers, or snap rings. Carefully pull the impeller off the shaft. In some cases, you may need to use an impeller puller tool for removal.
- Detach the old seal: The old seal will typically be composed of two primary components – a stationary seat that fits into the seal chamber bore, and a rotating portion that fits around the shaft. Carefully remove the rotating portion of the seal from the shaft. This may require gentle prying or twisting to break the seal. Remove the stationary seat from the seal chamber bore. This often involves carefully prying it out with a flat head screwdriver or similar tool.
Step 3: Cleaning and Inspection
- Clean all sealing areas: Use a non-toxic cleaner to clean the pump shaft, pump housing, O-ring groove, seal seat area, and shaft. Ensure no dirt, debris, or contaminated fluid remains.
- Inspect the pump’s operating condition and tolerances: Before installing a new seal, ensure the pump is in good working order and within the manufacturer’s acceptable tolerances. Refer to the pump’s manual for specific guidelines.
- Inspect the shaft or sleeve: The shaft finish should be smooth, with no roughness. Remove any burrs or sharp corners.
- Inspect the stuffing box face: Ensure the surface is smooth and free from pits or scratches.
- Inspect for a slinger: Many pumps have a slinger attached to the shaft. This component prevents water leakage from the pump housing from entering the bearing housing. Ensure the slinger is in good condition and properly positioned.
Step 4: Installing the New Seal
- Prepare the new seal: Carefully unpack the new seal and ensure all components are present and undamaged. Follow the manufacturer’s instructions for any required pre-installation steps, such as lubricating O-rings or applying anti-seize compound to the set screws.
- Install the seal: Begin by installing the stationary part of the seal into the pump housing or gland plate. Ensure it is seated properly and oriented correctly. Next, install the rotating part of the seal onto the shaft, following the manufacturer’s instructions for proper placement and tightening of any set screws. Be careful not to damage the seal faces during installation.
Step 5: Reassembly
- Install the impeller: Carefully slide the impeller onto the shaft, ensuring it is oriented correctly. Secure it in place according to the manufacturer’s specifications, which may involve a lock nut, lock washers, or a set screw.
- Reconnect the casing:
- For back pull-out designs, slide the back pull-out assembly against the installed casing and bolt it in place. Ensure the gasket or O-ring between the two sections is properly seated to prevent leaks.
- For close-coupled or non-back pull-out designs, reinstall the casing using the casing bolts. Make sure the casing is properly aligned and the gasket is in good condition and correctly positioned.
- Tighten the casing bolts: Using a torque wrench, tighten the casing bolts in a star pattern to the torque specifications provided in the pump’s Installation, Operation, and Maintenance (IOM) manual. This ensures even pressure distribution and prevents warping or damage to the casing.
- Reconnect the pump:
- For back pull-out designs, reattach the spacer to the coupling hubs, making sure it is properly aligned. Then, secure the mounting feet to the pump baseplate.
- For close-coupled pumps, reconnect the inlet and outlet piping, ensuring proper alignment and no undue stress on the connections.
- For non-back pull-out designs, replace the pump on the baseplate, reconnect the piping, and re-bolt the pump to the baseplate. Check alignment and make adjustments as necessary.
Step 6: Alignment
Use a laser alignment tool or dial indicators to check both angular and parallel alignment. Follow the pump manufacturer’s guidelines for acceptable alignment tolerances and adjustment methods. Adjustments may involve adding or removing shims under the motor or adjusting the position of the pump on the baseplate.
Step 7: Startup and Testing
- Refill the pump: Open the inlet and outlet isolation valves to allow fluid to enter the pump. Make sure the fluid is compatible with the pump materials and the mechanical seal.
- Vent the pump: Some pump designs may require venting to remove any trapped air. Consult your pump IOM for specific venting procedures.
- Verify motor rotation: Before starting the pump, confirm that the motor rotation matches the pump’s required rotation direction, which is typically indicated by an arrow on the pump casing.
- Prime the pump: Ensure the pump is properly primed before starting. Priming involves filling the pump casing with fluid and removing any air pockets.
- Start the pump: Turn on the pump and observe it for any unusual noises, excessive vibration, or leaks. If any issues are noticed, shut down the pump immediately and investigate the cause.
- Monitor performance: During the initial operating period, closely monitor the pump’s performance to verify that the mechanical seal is functioning correctly and the pump is operating within its designed parameters. Check for signs of leakage, overheating, or abnormal vibration.
Learn more about Common Mechanical Seal Installation Mistakes