Labyrinth seals and mechanical seals are two types of sealing solutions. They are used to prevent leakage in rotating equipment. This post will compare labyrinth seals and mechanical seals.
This post will explain their differences, advantages, and typical applications.
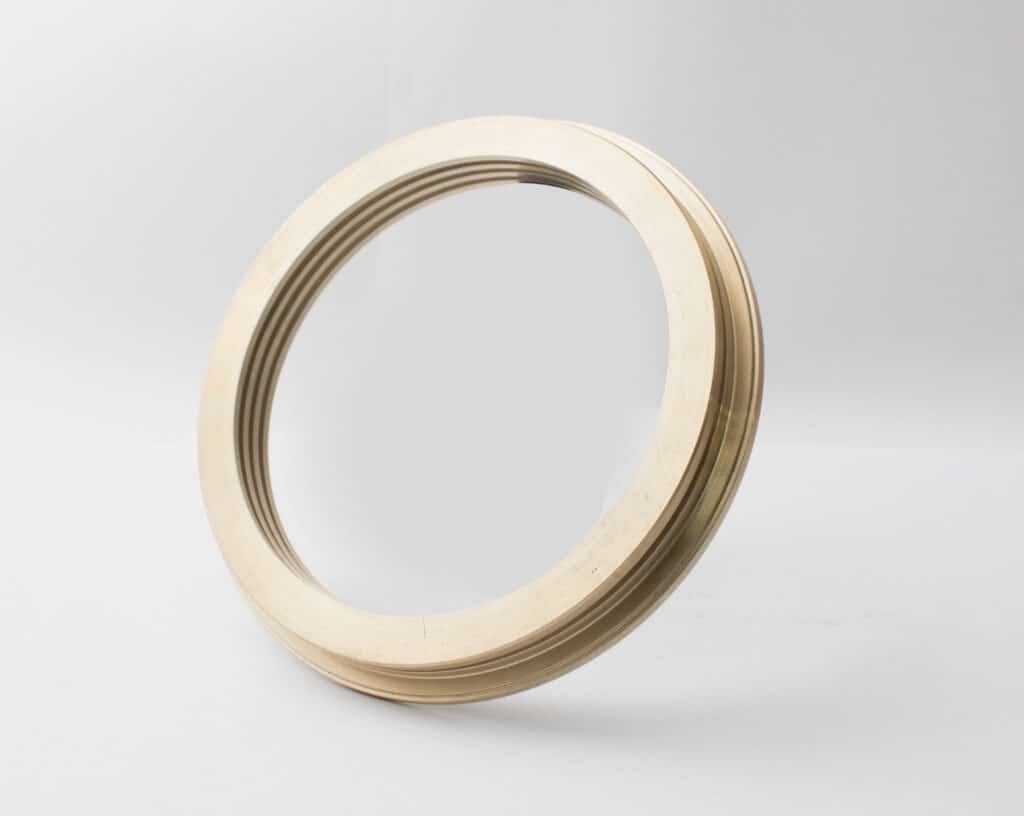
What Is the Difference between Labyrinth Seal and Mechanical Seal
Labyrinth seals are non-contacting and rely on the maze-like passages to reduce leakage, while mechanical seals are contacting seals that rely on the pressure between the two surfaces to prevent leakage.
Operating Principle
Labyrinth Seal: Relies on a tortuous path to restrict fluid flow through a series of grooves or chambers.
Mechanical Seal: Relies on physical contact between two flat seal faces, one rotating and one stationary, to prevent leakage.
Contact between Components
Labyrinth Seal: Non-contacting, with a clearance between the rotating and stationary parts.
Mechanical Seal: Contacting, with the seal faces in direct contact and pressed together with a controlled force.
Sealing Effectiveness
Labyrinth Seal: Generally less effective at preventing leakage, especially at higher pressures.
Mechanical Seal: More effective at preventing leakage, even at high pressures and temperatures.
Design Complexity
Labyrinth Seal: Relatively simple design with a series of grooves or chambers.
Mechanical Seal: More complex design, involving precise alignment and controlled force between the seal faces.
Cost
Labyrinth Seal: Lower cost due to simpler design and fewer components.
Mechanical Seal: Higher cost due to more complex design and additional components (e.g., secondary seals, springs).
Temperature and Pressure Handling
Labyrinth Seal: Can handle high temperatures and pressures, but with limitations.
Mechanical Seal: Can handle a wider range of temperatures and pressures, depending on the materials used.
Maintenance Requirements
Labyrinth Seal: Generally requires less maintenance due to the absence of contacting parts.
Mechanical Seal: Requires more frequent maintenance and potential replacement of seal faces due to wear from contact.
Applications
Labyrinth Seal: Commonly used in turbines, compressors, and pumps where leakage is acceptable within certain limits.
Mechanical Seal: Used in applications where leakage must be minimized or prevented, such as pumps, mixers, and agitators.
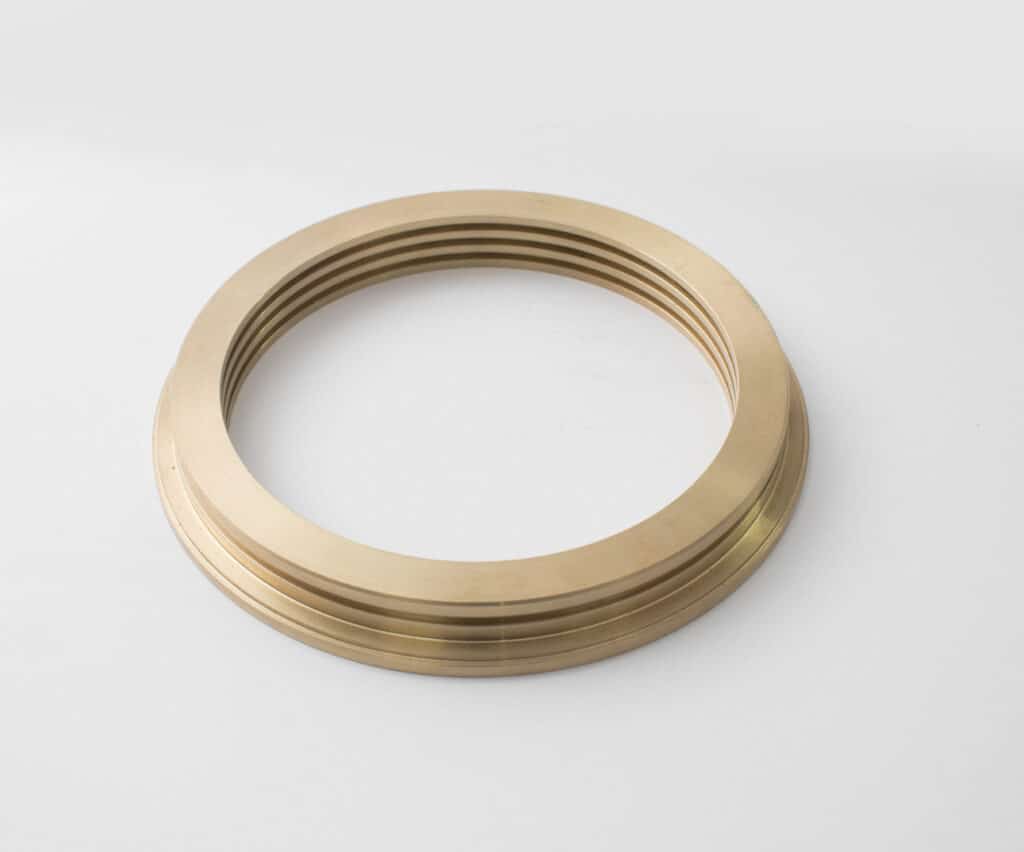
When would you use labyrinth seals
High-speed applications
Labyrinth seals are suitable for high-speed rotating equipment. They can handle high shaft velocities without excessive wear or heat generation. Turbomachinery, such as steam turbines and gas compressors, often utilize labyrinth seals.
Low-pressure applications
Labyrinth seals are effective in low-pressure environments. They can provide sufficient sealing performance when the pressure differential across the seal is relatively low. Applications with moderate to low-pressure requirements can benefit from labyrinth seals.
Non-critical sealing applications
Labyrinth seals are suitable for non-critical sealing applications. They can be used in systems where some leakage is acceptable and does not significantly impact the overall process. Auxiliary equipment and non-critical machinery can employ labyrinth seals.
Dirty or abrasive environments
Labyrinth seals are less sensitive to dirty or abrasive particles compared to mechanical seals. The tortuous path of the labyrinth seal can help prevent the ingress of contaminants into the sealed area. Applications involving dirty fluids or abrasive media can consider labyrinth seals.
High-temperature applications
Labyrinth seals can operate in high-temperature environments. They do not rely on elastomeric or polymeric components that may degrade at elevated temperatures. High-temperature processes, such as gas turbines and steam systems, can utilize labyrinth seals.
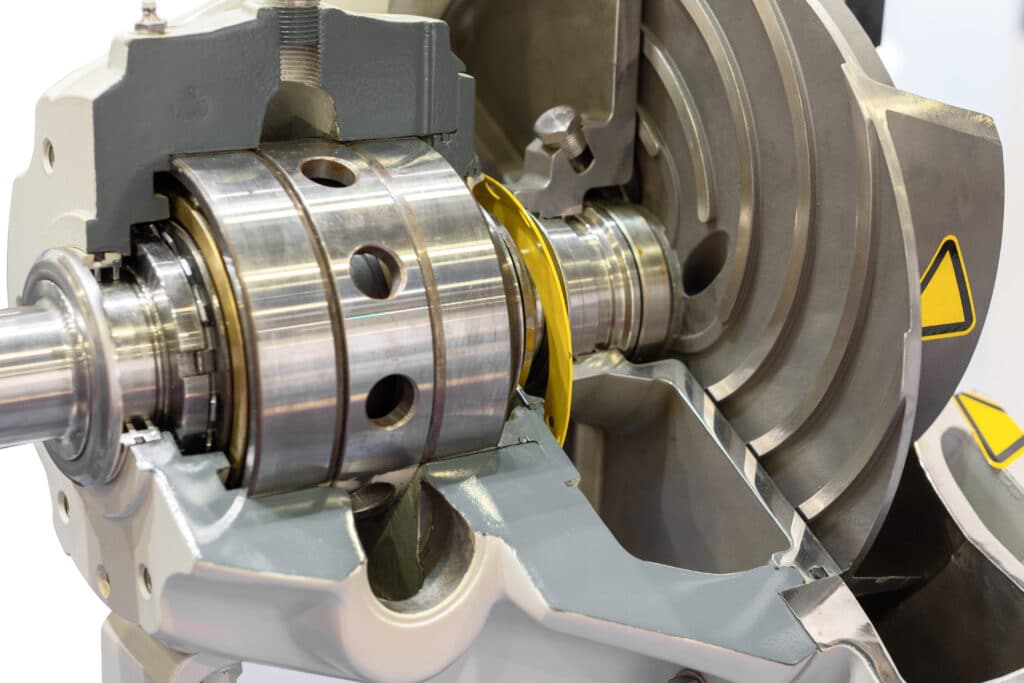
When would you use Mechanical seals
Critical sealing applications
Mechanical seals are preferred for critical sealing applications. They provide reliable and efficient sealing performance where leakage prevention is of utmost importance. Applications involving hazardous, toxic, or expensive fluids require the use of mechanical seals.
High-pressure applications
Mechanical seals are designed to handle high-pressure conditions. They can withstand significant pressure differentials across the seal faces without compromising sealing integrity. High-pressure pumps, compressors, and process equipment often employ mechanicalals.
Clean fluid environments
Mechanical seals perform best in clean fluid environments. They require a clean and lubricating fluid to maintain proper lubrication and cooling of the seal faces. Applications involving clean liquids or gases are suitable for mechanical seals.
Precise control of leakage
Mechanical seals offer precise control over leakage rates. They can be designed and selected to meet specific leakage requirements. Applications that demand strict leakage control, such as in the pharmaceutical or food processing industries, on mechanical seals.
Frequent starts and stops
Mechanical seals can handle frequent starts and stops of the equipment. They are designed to maintain sealing performance during transient conditions. Applications with intermittent operation or frequent cycling can benefit from mechanical seals.
In conclusion
Labyrinth seals and mechanical seals serve different purposes in sealing applications. Consider factors such as the type of fluid, operating conditions, and maintenance requirements when selecting the appropriate seal for your specific needs. Contact our experts today to discuss the best sealing solution for your application.