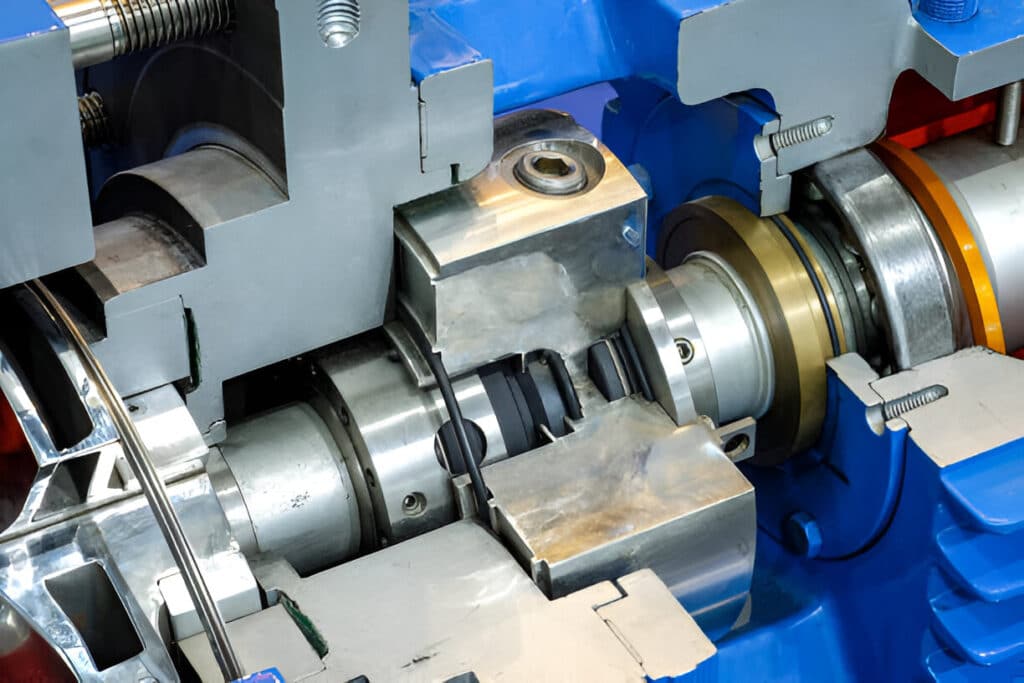
Contacting Seals
Contacting seals are a popular choice for many rotary applications, providing effective sealing through direct contact between the sealing surface and the rotating shaft. These seals are designed to accommodate shaft deflection, runout, and thermal expansion while maintaining a constant sealing interface. The most common types of contacting seals include radial lip seals, mechanical seals, and compression packings.
Radial Lip Seals
Radial lip seals, also known as rotary shaft seals or oil seals, are the most widely used type of shaft seal. They feature a flexible sealing lip that maintains contact with the shaft surface, preventing fluid leakage. The sealing lip is typically made from elastomeric materials such as NBR, FKM, or PTFE, and may incorporate a garter spring to ensure consistent sealing pressure.
Radial lip seals are available in various designs, including single-lip, double-lip, and multi-lip configurations, catering to different application requirements. They are commonly used in automotive, industrial, and marine applications, such as engine crankshafts, transmission shafts, and pump shafts.
Mechanical Seals
Mechanical seals are highly engineered sealing solutions that consist of two flat sealing surfaces—a stationary surface and a rotating surface—that are held in contact by spring pressure and fluid pressure. The sealing surfaces are typically made from hard, wear-resistant materials such as silicon carbide, tungsten carbide, or ceramic.
Mechanical seals offer superior sealing performance compared to lip seals, making them suitable for demanding applications involving high pressures, temperatures, and rotational speeds. They are commonly used in pumps, compressors, mixers, and other rotating equipment in industries such as oil and gas, chemical processing, and power generation.
Compression Packings
Compression packings are traditional sealing solutions that consist of braided or twisted strands of packing material, such as PTFE, graphite, or aramid fibers. The packing material is compressed into the stuffing box, creating a seal between the rotating shaft and the housing.
While compression packings have been largely replaced by more advanced sealing technologies, they still find use in certain applications, particularly in older equipment or in situations where ease of maintenance and low cost are prioritized. However, compression packings require frequent adjustment and replacement to maintain effective sealing.
Non-contacting Seals
Non-contacting seals, as the name suggests, do not rely on direct contact between the sealing components and the rotating shaft. Instead, they utilize labyrinth paths, fluid dynamics, or magnetic fields to create a sealing effect. Non-contacting seals are preferred in applications where low friction, high rotational speeds, or minimal wear are required. The most common types of non-contacting seals include labyrinth seals, floating ring seals, and magnetic fluid seals.
Labyrinth Seals
Labyrinth seals consist of a series of tight clearances and intricate passages that create a tortuous path for the fluid, making it difficult for leakage to occur. The sealing effect is achieved through a combination of centrifugal force, fluid dynamics, and the pressure drop across the seal.
Labyrinth seals are suitable for high-speed applications and can handle a wide range of temperatures and pressures. They are commonly used in gas turbines, compressors, and steam turbines, where their non-contacting design minimizes friction and wear.
Floating Ring Seals
Floating ring seals, also known as bushing seals or annular seals, consist of a floating ring that is located between the rotating shaft and the stationary housing. The ring is typically made from a wear-resistant material, such as carbon graphite or PTFE, and is designed to float freely in the radial direction.
The sealing effect is achieved through a combination of centrifugal force and fluid dynamics, with the floating ring acting as a barrier to fluid leakage. Floating ring seals are suitable for high-speed applications and can accommodate shaft deflection and misalignment.
Magnetic Fluid Seals
Magnetic fluid seals utilize a ferrofluid, which is a suspension of magnetic particles in a carrier liquid, to create a liquid O-ring around the shaft. The ferrofluid is held in place by a permanent magnet, forming a tight seal that prevents leakage.
Magnetic fluid seals offer several advantages, including low friction, high sealing efficiency, and the ability to tolerate shaft misalignment and runout. They are commonly used in high-vacuum applications, such as semiconductor manufacturing equipment and space technology.
Seal Selection Considerations
Operating Conditions
- Pressure: The seal must be capable of handling the maximum pressure encountered in the system, both static and dynamic.
- Temperature: The seal material must be compatible with the operating temperature range, ensuring that it retains its properties and performance.
- Speed: The seal design must be suitable for the rotational speed of the shaft, considering factors such as centrifugal force and heat generation.
- Runout: The seal must accommodate any shaft runout or misalignment without compromising its sealing effectiveness.
Fluid Properties
- Viscosity: The seal must be able to handle the viscosity of the fluid, ensuring proper lubrication and sealing performance.
- Cleanliness: The seal design must account for the cleanliness of the fluid, considering factors such as particle contamination and filtration requirements.
- Abrasiveness: If the fluid contains abrasive particles, the seal material must be wear-resistant to prevent excessive wear and leakage.
- Chemical Reactivity: The seal material must be chemically compatible with the fluid to prevent degradation and ensure long-term performance.
Environmental Factors
- Dust: In dusty environments, seals with additional dust lips or labyrinth designs may be necessary to prevent particle ingress and premature wear.
- Moisture: Seals exposed to moisture or water must be designed to prevent corrosion and maintain sealing effectiveness in wet conditions.
- Vibration: In applications with high vibration levels, the seal design must be robust enough to maintain contact and prevent leakage.
Shaft and Housing Interface
- Surface Finish: The shaft surface finish must be suitable for the seal type, ensuring proper contact and minimizing wear.
- Concentricity: The seal housing and shaft must be concentric to prevent uneven wear and leakage.
- Thermal Expansion: The seal design must accommodate any differences in thermal expansion between the shaft and housing materials to maintain sealing effectiveness.
Leakage Rate and Life Expectations
- Leakage Rate: The seal type and material must be selected to achieve the desired leakage rate, considering factors such as fluid properties and operating conditions.
- Life Expectations: The seal design and material must be chosen to provide the expected service life, taking into account factors such as wear, degradation, and maintenance intervals.
Ease of Installation and Maintenance
- Installation: The seal design should allow for easy and accurate installation, with minimal specialized tools or training required.
- Maintenance: The seal should be designed to facilitate easy inspection, cleaning, and replacement, minimizing downtime and maintenance costs.
Seal Material Options
Elastomers
Elastomers are widely used in shaft seals due to their flexibility, resilience, and sealing properties. The most common elastomers used in sealing applications include:
- Nitrile Butadiene Rubber (NBR): NBR is a versatile elastomer with good resistance to oils, fuels, and hydraulic fluids, making it suitable for general-purpose sealing applications.
- Fluoroelastomer (FKM): FKM offers excellent resistance to high temperatures, chemicals, and aggressive fluids, making it ideal for demanding applications in the chemical and petroleum industries.
- Ethylene Propylene Diene Monomer (EPDM): EPDM is known for its resistance to ozone, weathering, and high temperatures, making it suitable for outdoor and high-temperature applications.
- Polytetrafluoroethylene (PTFE): PTFE is a highly chemical-resistant and low-friction material, often used in combination with elastomers to enhance sealing performance and reduce wear.
Thermoset Polymers
Thermoset polymers are another class of materials used in shaft seals, offering high strength, wear resistance, and thermal stability. Common thermoset polymers include:
- Polyurethane: Polyurethane seals offer excellent abrasion resistance, tear strength, and resistance to oils and solvents, making them suitable for demanding industrial applications.
- Polyacrylate: Polyacrylate seals provide good resistance to heat, oils, and chemicals, and are often used in high-temperature and aggressive fluid environments.
Thermoplastics
Thermoplastic materials are increasingly used in shaft seals due to their excellent chemical resistance, low friction, and high-temperature stability. The most common thermoplastics used in sealing applications include:
- Polytetrafluoroethylene (PTFE): PTFE is a highly chemical-resistant and low-friction material, often used in combination with elastomers or as a solid seal material in demanding applications.
- Polyetheretherketone (PEEK): PEEK offers excellent mechanical strength, wear resistance, and chemical resistance, making it suitable for high-temperature and aggressive fluid environments.
- Polyphenylene Sulfide (PPS): PPS is known for its high strength, stiffness, and chemical resistance, making it suitable for demanding applications in the chemical and automotive industries.
Face Materials
In mechanical seals, the face materials are critical for ensuring effective sealing and long-term performance. The most common face materials used in mechanical seals include:
- Carbon: Carbon graphite is a widely used face material due to its excellent lubricity, chemical resistance, and compatibility with a wide range of fluids.
- Silicon Carbide: Silicon carbide offers high hardness, wear resistance, and chemical resistance, making it suitable for demanding applications with abrasive fluids or high pressures.
- Tungsten Carbide: Tungsten carbide is known for its high hardness, wear resistance, and compatibility with a wide range of fluids, making it suitable for high-pressure and high-speed applications.
- Diamond Coating: Diamond-coated faces provide exceptional hardness, wear resistance, and low friction, making them suitable for the most demanding applications with abrasive fluids or high pressures.
FAQs
What are the different types of marine shaft seals?
Marine shaft seals are designed to prevent water from entering the vessel through the propeller shaft. The most common types of marine shaft seals include:
- Lip seals: Radial lip seals with a flexible lip that maintains contact with the shaft surface, preventing water entry.
- Mechanical seals: Face seals that consist of a stationary and a rotating face, held in contact by spring pressure and fluid pressure.
- Labyrinth seals: Non-contact seals that utilize a series of tight clearances and intricate passages to create a tortuous path for the fluid, making it difficult for water to enter.
- Bellows seals: Mechanical seals with a flexible bellows element that accommodates shaft movement and misalignment while maintaining sealing effectiveness.
What are the types of oil seals?
Oil seals, also known as radial lip seals, are designed to prevent fluid leakage and protect against contaminants in various applications. The most common types of oil seals include:
- Single-lip seals: Seals with a single sealing lip that maintains contact with the shaft surface, preventing fluid leakage.
- Double-lip seals: Seals with two sealing lips, providing enhanced sealing performance and protection against contaminants.
- Cassette seals: Pre-assembled seals that consist of a metal casing, sealing lip, and garter spring, facilitating easy installation and replacement.
- Axial seals: Seals that are designed to seal against axial motion, typically used in applications with reciprocating shafts or rods.
What are the different types of rotary seals?
Rotary seals are designed to prevent fluid leakage and maintain system pressure in rotating equipment. The most common types of rotary seals include:
- Radial lip seals: Seals with a flexible sealing lip that maintains contact with the rotating shaft surface, preventing fluid leakage.
- Mechanical seals: Face seals that consist of a stationary and a rotating face, held in contact by spring pressure and fluid pressure, providing effective sealing in demanding applications.
- Labyrinth seals: Non-contact seals that utilize a series of tight clearances and intricate passages to create a tortuous path for the fluid, minimizing leakage in high-speed applications.
- Floating ring seals: Non-contact seals that consist of a floating ring located between the rotating shaft and the stationary housing, providing sealing through centrifugal force and fluid dynamics.