Gland plates are integral components in mechanical seals, serving to secure and align the seal assembly within the equipment. Their design and material selection directly impact the performance and reliability of the sealing system.
By providing a stable foundation for the mechanical seal, gland plates contribute to the prevention of leaks and the optimal functioning of rotating equipment in various industrial applications.
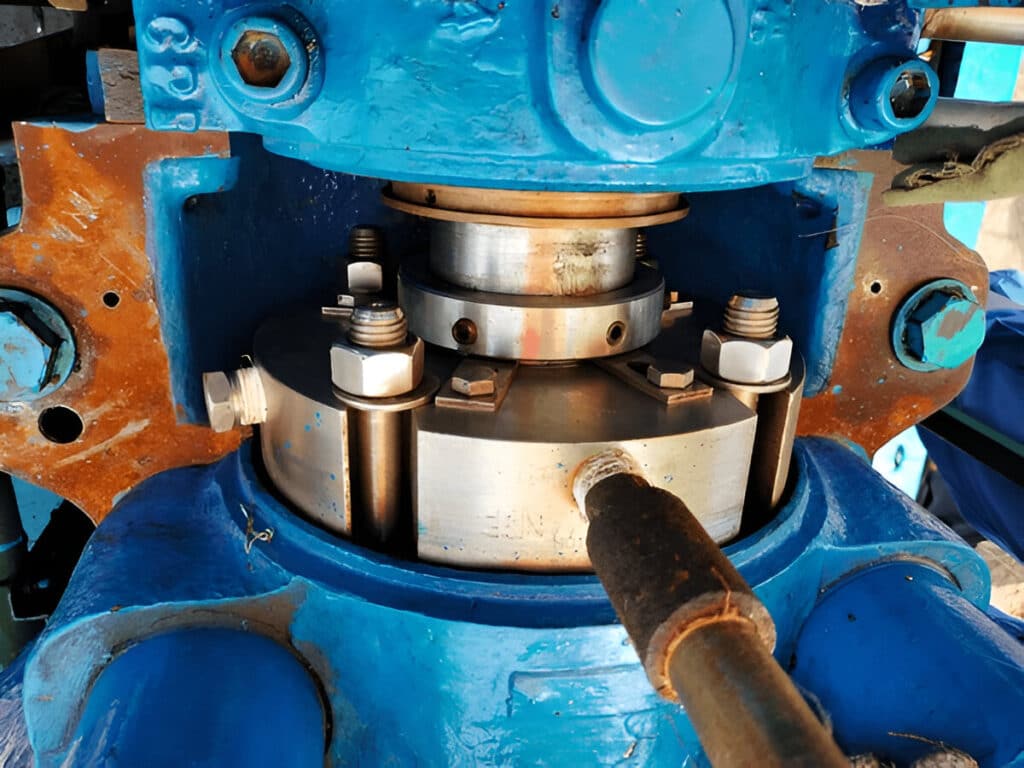
What Is a Gland Plate
A gland plate, also known as a seal gland, is a critical component in mechanical seals used to prevent leakage in rotary shaft equipment. It is a stationary part that houses the stationary seal ring and provides a connection point for the seal assembly to the equipment. The gland plate is typically mounted on the equipment seal chamber bore and is designed to accommodate shaft movement, such as misalignment, deflections, and expansion.
The primary function of the gland plate is to maintain the position of the stationary seal ring relative to the rotating shaft. It also serves as a heat sink, dissipating heat generated by the seal faces during operation. By maintaining proper alignment and heat dissipation, the gland plate helps to ensure optimal seal performance and longevity.
How Does a Gland Plate Work
The gland plate works in conjunction with other seal components to create a pressure-tight barrier between the process fluid and the atmosphere. It holds the stationary seal ring in place, which contacts the rotating seal ring mounted on the shaft sleeve. The seal faces between the stationary and rotating rings create a dynamic seal that prevents leakage along the shaft.
During operation, the gland plate maintains the position of the stationary seal ring, ensuring consistent contact with the rotating seal ring. As the shaft rotates, the seal faces generate heat due to friction. The gland plate acts as a heat sink, conducting heat away from the seal faces and into the surrounding environment or flush water, if present.
Types of Gland Plates
Flat Plate Gland Plates
Flat plate gland plates are the most basic and common type used in mechanical seals. These gland plates consist of a simple flat surface with holes for the seal gland bolts and the shaft bore. Flat plates provide a cost-effective solution for many standard sealing applications.
Step Plate Gland Plates
Step plate gland plates feature a raised “step” or shoulder machined into the plate surface. This step helps to properly align and locate the seal gland unit concentric to the shaft. Step plates are preferred for larger shaft sizes or in applications with higher pressures, as they provide improved seal chamber geometry and stability compared to flat plates. The step also allows for better distribution of the compression forces on the gasket, ensuring a more reliable static seal.
Piloted Gland Plates
Piloted gland plates, also known as centering ring gland plates, incorporate a pilot or centering ring that fits snugly into the seal chamber bore. This design automatically centers the gland plate and seal gland unit, ensuring optimal alignment with the shaft. Piloted plates are ideal for applications with high shaft speeds, large shaft diameters, or where precise alignment is critical. They help to minimize shaft deflections and vibrations, reducing wear on the seal faces and extending seal life.
Cartridge Gland Plates
Cartridge gland plates are designed to accommodate pre-assembled cartridge seals. These plates have a larger bore to fit the cartridge unit and often include tapped holes for the cartridge locking screws. Cartridge gland plates simplify seal installation and removal, as the entire cartridge can be handled as a single unit. This reduces maintenance times and minimizes the risk of incorrect assembly.
Dual Gland Plates
Dual gland plates, used with double mechanical seals, have provisions for both the inboard and outboard seal glands. These plates are typically thicker to accommodate the additional gland and may include separate ports for barrier fluid or flush water. Dual gland plates are used in applications requiring enhanced safety or leak protection, such as hazardous or environmentally sensitive processes. The redundancy provided by the double seal arrangement ensures continued sealing performance even if the primary seal fails.
Materials Used in Gland Plates
Material | Key Properties | Typical Applications |
---|---|---|
Cast Iron (ASTM A48) | – Good machinability – Moderate strength and durability – Economical | – General-purpose applications – Low-pressure systems – Non-corrosive fluids |
Ductile Iron (ASTM A536) | – Higher strength and toughness than cast iron – Good machinability – Moderate corrosion resistance | – Medium-pressure applications – Mildly corrosive fluids – Improved durability requirements |
Carbon Steel (ASTM A216) | – High strength and toughness – Good machinability – Suitable for high-pressure applications | – High-pressure systems – Non-corrosive fluids – Demanding mechanical environments |
Stainless Steel (ASTM A351) | – Excellent corrosion resistance – High strength and durability – Wide range of grades available | – Corrosive fluid applications – Food and pharmaceutical processing – Marine and offshore environments |
Alloy 20 (ASTM A351 CN7M) | – Superior corrosion resistance – High nickel and chromium content – Excellent for acidic and chloride-containing fluids | – Highly corrosive chemical processing – Seawater and brine services – Sulfuric and hydrochloric acid applications |
Hastelloy C-276 (ASTM A494 CW-12MW) | – Outstanding corrosion resistance – High molybdenum content for pitting and crevice corrosion resistance – Suitable for extreme chemical environments | – Severely corrosive chemical processing – Hydrochloric, sulfuric, and phosphoric acid applications – Seawater and chloride-containing fluids |