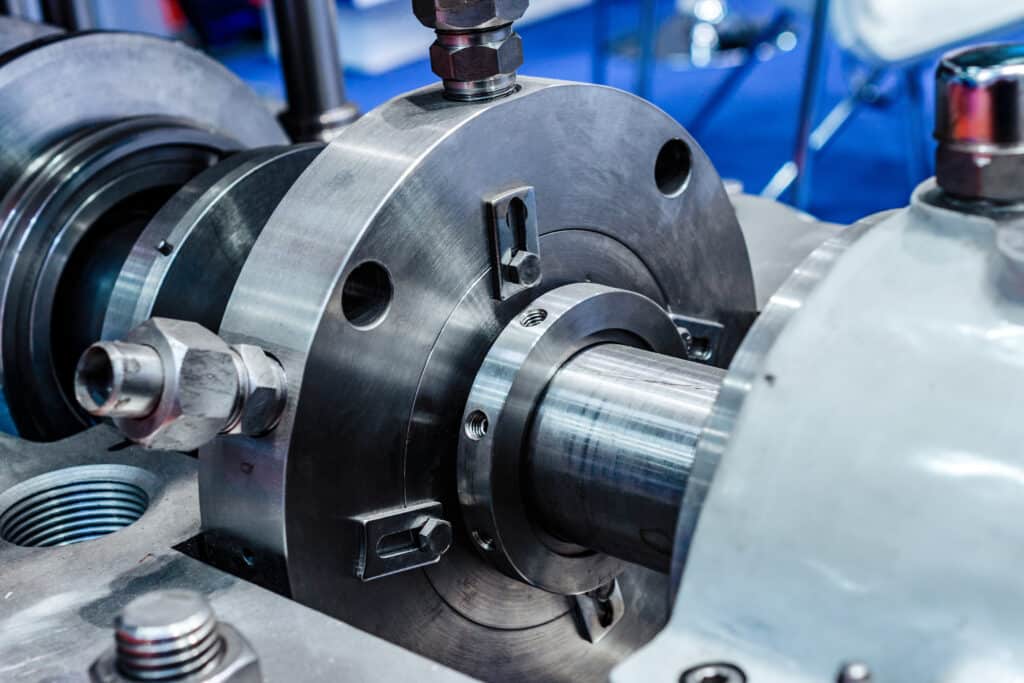
What Is a High-Pressure Mechanical Seal
A high-pressure mechanical seal is a critical component in machinery that operates under extreme pressure conditions, typically above 50 bar (725 psi). These seals are designed to prevent leakage of fluids or gases from the equipment while withstanding the immense forces generated by high-pressure environments.
The primary function of a high-pressure mechanical seal is to maintain a secure barrier between the process fluid and the atmosphere, even under the most demanding conditions. These seals consist of two main components: a stationary part (stator) and a rotating part (rotor), which are pressed together by a combination of hydraulic and spring forces. The sealing faces are typically made of hard, wear-resistant materials like silicon carbide, tungsten carbide, or ceramics, which can withstand the high pressures and temperatures encountered in these applications.
How High-Pressure Mechanical Seals Work
The working principle of high-pressure mechanical seals relies on the creation of a thin fluid film between the stationary and rotating seal faces. As the shaft rotates, the seal rings are pressed together by a combination of spring force and hydraulic pressure from the process fluid. This pressure causes a small amount of the process fluid to leak between the seal faces, creating a thin, stable fluid film that lubricates and cools the faces while preventing further leakage.
The fluid film between the seal faces is maintained by a delicate balance between the hydraulic pressure, spring force, and the precise geometry of the seal faces. The seal faces are lapped to a very high flatness, typically within 2-3 helium light bands (0.22-0.33 µm), to ensure uniform contact and minimize leakage. The rotating seal ring is usually mounted on the shaft with a flexible bellows or other secondary sealing element, which accommodates minor shaft misalignment and axial movement while maintaining the seal.
Which Type of Mechanical Seal Is Used for High Pressure Applications
Face-to-Face
In a face-to-face arrangement, two mechanical seals are installed with their seal faces oriented towards each other. This arrangement is commonly used in high-pressure applications because it balances the hydraulic forces acting on the seal faces, reducing the net closing force and heat generation. Face-to-face seals also provide a degree of redundancy, as the second seal can act as a backup if the primary seal fails.
Back-To-Back
Back-to-back seals are arranged with their seal faces oriented away from each other, with the space between the seals typically filled with a buffer fluid at a higher pressure than the process fluid. This arrangement is used when the process fluid is hazardous, toxic, or environmentally sensitive, as any leakage from the primary seal is contained by the buffer fluid and secondary seal. Back-to-back seals require a separate buffer fluid system and additional piping and instrumentation.
Tandem (Or Face-to-Back)
Tandem, or face-to-back, seals combine elements of face-to-face and back-to-back arrangements. In this configuration, two seals are installed with their faces oriented in opposite directions, with the primary seal facing the process fluid and the secondary seal facing away. The space between the seals is usually vented to a safe location or connected to a buffer fluid system at a lower pressure than the process fluid. Tandem seals provide both the pressure-balancing benefits of face-to-face seals and the safety and containment features of back-to-back seals.
Factors Affecting High-Pressure Mechanical Seal Performance
Pressure of Process Fluid on Seal Faces
As the fluid pressure increases, the closing force on the seal faces also increases, leading to higher face loads, increased heat generation, and potentially faster wear. To counteract these effects, high-pressure seals often incorporate features such as balance holes, grooves, or orifices in the seal faces to reduce the effective closing force and maintain a stable fluid film.
Temperature Control in the Seal Chamber
High temperatures can cause thermal expansion of seal components, leading to increased face loads and wear. Excessive heat can also degrade lubricating properties of the fluid film, increasing friction and the risk of seal failure. To mitigate these issues, high-pressure seals often incorporate cooling jackets, heat exchangers, or thermosyphon systems to remove heat from the seal chamber and maintain stable operating temperatures.
Proper Lubrication and Cooling of Seal Faces
The fluid film between the seal faces acts as both a lubricant and a coolant, carrying away frictional heat and preventing direct contact between the faces. To ensure adequate lubrication and cooling, high-pressure seals may incorporate features such as spiral grooves, radial slots, or microstructures on the seal faces to promote fluid circulation and heat dissipation. The selection of seal face materials with good thermal conductivity and self-lubricating properties, such as silicon carbide or graphite-loaded materials, can also enhance lubrication and cooling performance.
Support Systems for Mechanical Seal High-Pressure Applications
High-pressure mechanical seals require specialized support systems to ensure optimal performance and longevity. These systems help maintain stable operating conditions, prevent seal failure, and extend the life of the seals. One crucial component is the API Plan 52, which utilizes a buffer fluid reservoir to provide a clean, cool, and pressurized environment for the seals.
The API Plan 52 system circulates a compatible buffer fluid, such as glycol or oil, through a seal chamber at a pressure higher than the process fluid. This positive pressure differential prevents process fluid from entering the seal chamber, minimizing contamination and extending seal life. The system also helps to dissipate heat generated by the seals, maintaining a stable operating temperature.
Other essential support systems for high-pressure mechanical seals include:
- Proper seal face lubrication: Adequate lubrication is critical for reducing friction and wear on the seal faces. This can be achieved through the use of barrier fluids, such as oil or grease, or by incorporating lubricating features into the seal design.
- Temperature control: Maintaining a consistent temperature in the seal chamber is crucial for preventing thermal distortion and ensuring proper seal face alignment. This can be accomplished through the use of cooling jackets, heat exchangers, or temperature control units.
- Pressure monitoring: Continuously monitoring the pressure in the seal chamber helps detect any anomalies or leaks, allowing for timely maintenance and preventing catastrophic failures.
Applications of High-Pressure Mechanical Seal
- Centrifugal pumps: High-pressure mechanical seals are used in centrifugal pumps handling high-pressure fluids, such as boiler feed water pumps, pipeline pumps, and injection pumps in oil and gas wells.
- Compressors: Mechanical seals are used in high-pressure compressors for gases like hydrogen, natural gas, and carbon dioxide, as well as in refrigeration compressors using high-pressure refrigerants.
- Turbines: High-pressure seals are used in steam and gas turbines to prevent leakage of high-pressure steam or combustion gases from the turbine casing.
- Reactors and pressure vessels: Mechanical seals are used in agitators, mixers, and other rotating equipment in high-pressure reactors and pressure vessels in chemical processing and petrochemical industries.
- Subsea equipment: High-pressure seals are critical components in subsea oil and gas production equipment, such as subsea pumps, compressors, and valves, where they must withstand extreme pressures and harsh environmental conditions.
- High-pressure water systems: Mechanical seals are used in high-pressure water pumps and valves in applications such as reverse osmosis desalination, high-pressure cleaning, and waterjet cutting.
FAQs
What Is the Pressure Limit for Mechanical Seals?
In general, standard mechanical seals can handle pressures up to about 20 bar (290 psi), while high-pressure seals are designed for pressures ranging from 20 to 200 bar (290 to 2,900 psi) or higher.