In the machinery industry, mechanical seals are critical components that prevent leaks and ensure the efficient operation of rotating equipment. One key aspect of maintaining the integrity and performance of these seals is the flush rate, which refers to the flow of fluid used to cool, lubricate, and clean the sealing faces.
Determining the optimal flush rate is a delicate balancing act that requires careful consideration of various factors and potential consequences. This blog post will delve into the intricacies of flush rates, exploring the risks associated with insufficient or excessive flow, general guidelines, and factors influencing the ideal rate, as well as methods for determining the appropriate flush rate and the role of API seal flush plans.
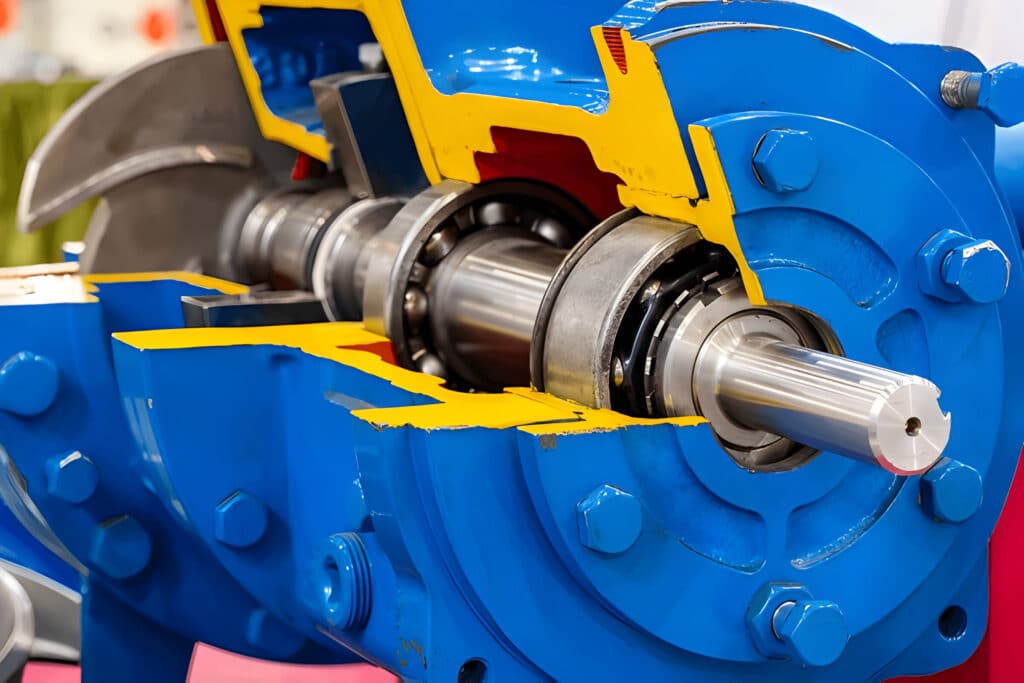
What Is a Flush Rate
In the context of mechanical seals, the flush rate refers to the volume of fluid introduced into the seal chamber per unit of time. This fluid, known as flush fluid or barrier fluid, serves to lubricate, cool, and clean the seal faces. Maintaining an optimal flush rate is critical for the proper functioning and longevity of mechanical seals.
The flush fluid is typically introduced through a port in the gland plate or seal chamber. The fluid then flows across the seal faces before exiting through another port or drain. The flow rate of the flush fluid is carefully regulated to ensure that it effectively performs its intended functions without causing any adverse effects on the seal performance.
Consequences of Insufficient Flush Rates
Overheating
One of the primary consequences of insufficient flush rates is overheating of the mechanical seal. The flush fluid acts as a coolant, absorbing heat generated by the friction between the rotating and stationary seal faces. If the flush rate is too low, the fluid may not effectively dissipate the heat, leading to elevated temperatures at the seal faces.
Increased Wear and Tear
Insufficient flush rates can also lead to increased wear and tear on the mechanical seal components. The flush fluid serves as a lubricant, reducing friction between the seal faces and minimizing wear. When the flush rate is too low, the seal faces may experience increased contact pressure and abrasion, accelerating the wear process.
Contamination Buildup
Another consequence of insufficient flush rates is the buildup of contaminants within the seal chamber. The flush fluid helps to flush away any debris, particles, or process fluid that may enter the seal chamber. If the flush rate is inadequate, these contaminants can accumulate on the seal faces or within the chamber.
Risks of Excessive Flush Rates
Erosion
While insufficient flush rates can lead to various problems, excessive flush rates can also have detrimental effects on mechanical seals. One of the primary risks associated with high flush rates is erosion of the seal faces and other components.
When the flush fluid flows across the seal faces at excessively high velocities, it can cause erosion, gradually wearing away the material of the seal faces. This erosion can create uneven surfaces, compromising the flatness and alignment of the faces. As a result, the sealing ability of the mechanical seal may be reduced, leading to increased leakage.
Increased Operational Costs Without Significant Benefits
Another risk associated with excessive flush rates is the potential for increased operational costs without yielding significant benefits. Higher flush rates require more flush fluid to be pumped through the system, which can lead to increased energy consumption and pump wear.
Moreover, excessive flush rates may necessitate larger pumps, piping, and storage tanks to accommodate the increased fluid volume. This can result in higher initial investment costs and ongoing maintenance expenses.
Factors Influencing Flush Rate
Several factors influence the determination of an appropriate flush rate for mechanical seals. Understanding these factors is necessary to optimize seal performance and longevity while minimizing operational costs. The following are the key factors that impact flush rates:
Seal Size and Type
The size and type of mechanical seal significantly influence the required flush rate. Larger seals generally require higher flush rates to maintain proper lubrication and cooling. The seal type, such as single or double, also affects the flush rate requirements. Double seals often require higher flush rates compared to single seals due to the additional fluid barrier between the process and the atmosphere.
Viscosity
The viscosity of the process fluid and the flush fluid impacts the required flush rate. Higher viscosity fluids require higher flush rates to maintain adequate flow and heat transfer. The flush fluid’s viscosity should be considered when selecting a compatible flush medium and determining the appropriate flush rate.
Temperature
The operating temperature of the process fluid and the seal environment influence the flush rate requirements. Higher temperatures necessitate increased flush rates to dissipate heat effectively and prevent overheating. The flush fluid’s temperature should also be considered, as it affects its cooling capacity and the overall heat transfer efficiency.
Volatility
The volatility of the process fluid affects the flush rate requirements. Highly volatile fluids tend to vaporize more readily, leading to the formation of vapor pockets within the seal chamber. Increased flush rates are necessary to maintain a stable liquid barrier and prevent vapor formation, which can compromise seal performance and lead to premature failure.
Speed
The rotational speed of the shaft and seal components impacts the flush rate requirements. Higher speeds generate more heat due to increased friction and require higher flush rates to dissipate the heat effectively. The flush rate should be adjusted accordingly to maintain proper lubrication and cooling at various operating speeds.
Pressure
The pressure of the process fluid and the seal chamber influence the required flush rate. Higher pressures necessitate increased flush rates to maintain a positive pressure differential between the flush fluid and the process fluid. This positive pressure differential prevents process fluid from entering the seal chamber and contaminating the sealing surfaces. The flush system’s pressure capabilities should be considered when determining the appropriate flush rate.
Methods to Determine Flush Rate
Determining the appropriate flush rate for a mechanical seal requires careful consideration of various factors. One common method is to consult the manufacturer’s specifications and recommendations for the specific seal model and application. These guidelines often provide a range of acceptable flush rates based on the seal size, operating conditions, and fluid properties.
Another approach is to calculate the flush rate using established formulas and guidelines. The American Petroleum Institute (API) provides a widely-used formula for determining the minimum flush rate based on the seal chamber pressure and the fluid’s vapor pressure. This formula ensures that the flush rate is sufficient to maintain a liquid state at the seal faces, preventing vaporization and excessive wear.
API Seal Flush Plans and Their Role
API seal flush plans are standardized configurations that define the arrangement of piping, instrumentation, and control systems for providing flush fluid to mechanical seals. These plans are designed to ensure proper seal lubrication, cooling, and debris removal, ultimately enhancing seal performance and longevity.
Each API flush plan is designated by a number, such as Plan 11, Plan 13, or Plan 54, and specifies the source of the flush fluid, the direction of flow, and the required instrumentation. For example, API Plan 11 involves a flush fluid recirculated from the pump discharge to the seal chamber, while Plan 13 uses an external fluid source for the flush.
The selection of the appropriate API flush plan depends on factors such as the type of fluid being sealed, the operating conditions, and the specific requirements of the application. By adhering to these standardized plans, facilities can ensure consistent and reliable seal performance, facilitate maintenance and troubleshooting, and comply with industry best practices.