High-pressure pumps are essential components in many industrial applications, from oil and gas production to chemical processing. Maintaining optimal sealing performance in these demanding environments is critical for ensuring equipment reliability, safety, and efficiency.
This article explores the key considerations and techniques for effectively sealing high-pressure pump systems. We will delve into the specific needs of high-pressure applications, examine various types of seals and their configurations, discuss material selection, and highlight the importance of seal support systems.
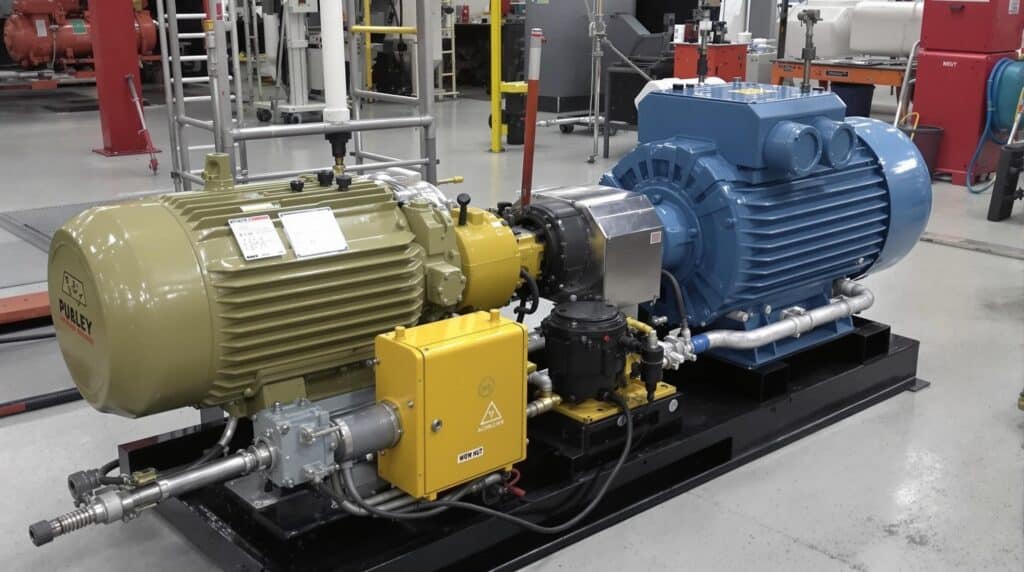
High-Pressure Sealing Needs
Challenges of High-Pressure Environments
High-pressure pump systems operate under extreme conditions that push the limits of traditional sealing methods. As pressures increase, the forces acting on the seals intensify exponentially. This creates a challenging environment where seals must withstand not only immense pressure but also high temperatures, corrosive media, and potential contaminants.
Maintaining Barrier Fluid Integrity
Another critical aspect of high-pressure sealing is maintaining the integrity of the barrier fluid. This fluid, often pressurized to a level greater than the process media, serves as the front-line defense in seal performance and longevity. It lubricates the seal faces, carries away heat, and prevents contamination from entering the sealing interface.
However, as the pressure differential between the barrier fluid and process media increases, maintaining a stable fluid film between the seal faces becomes increasingly difficult. If the barrier fluid pressure falls below the process pressure, even momentarily, the process media can infiltrate the sealing interface leading to accelerated wear and seal failure.
Optimizing Seal Life and Reliability
The extreme pressures found in high-pressure pump applications not only make seal failure more consequential but also accelerate wear and tear on sealing components. Maximizing the operational life and reliability of high-pressure seals requires carefully balancing multiple design considerations.
Seal faces must be manufactured from durable materials with excellent wear and heat-resistant properties. The geometric design of seal faces should promote optimal lubrication and heat dissipation. Adaptive mechanisms are often incorporated to allow the seal to self-adjust as conditions change. Redundancy, such as dual seal arrangements, provide an extra layer of assurance against leakage and failure.
Types of Seals for High-Pressure Applications
Dual Mechanical Seals
Dual mechanical seals provide an extra layer of protection against leakage. In this design, two independent seals are arranged in series, with a buffer fluid circulating between them. The buffer fluid acts as a barrier, preventing process fluid from escaping to the atmosphere if the primary seal fails.
The dual seal arrangement also allows for monitoring of seal condition. If the primary seal begins to leak, the buffer fluid pressure will change, alerting operators to the issue before a complete failure occurs. This early warning system enables proactive maintenance and helps avoid costly unplanned shutdowns.
Balanced Mechanical Seals
Balanced mechanical seals are designed to equalize the hydraulic forces acting on the seal faces. In an unbalanced seal, high fluid pressure can generate excessive force on the seal faces, leading to increased wear and premature failure. Balanced seals incorporate features such as stepped shafts, hydraulic recirculation passages, or pressure-responsive elements to counteract these forces.
By balancing the pressure, these seals reduce friction and heat generation at the seal faces. This prolongs seal life and allows for operation at higher pressures and speeds. Balanced seals are particularly well-suited for applications with high fluid pressures, large shaft diameters, or frequent starts and stops.
Seal Configurations
Face-to-Face
In a face-to-face configuration, two mechanical seals are mounted with their seal faces pointing towards each other. This arrangement allows for a compact design and simplifies installation and maintenance. Face-to-face seals are often used in applications with limited space or where easy access to the seals is required.
However, face-to-face seals may be more susceptible to heat buildup, as the heat generated by one seal can transfer to the other.
Back-to-Back
Back-to-back seal configurations have the seal faces pointing away from each other. This arrangement provides excellent resistance to pressure fluctuations and thermal expansion. The opposing orientation of the seals helps to balance axial forces, reducing wear on the seal faces.
Back-to-back seals are commonly used in high-pressure, high-temperature applications. They are also well-suited for systems with frequent pressure cycling or where thermal shock is a concern.
Tandem Configurations
Tandem seal configurations consist of two seals mounted in the same direction, with a buffer fluid between them. This arrangement combines the benefits of dual seals and balanced seals. The primary seal handles the high-pressure process fluid, while the secondary seal contains the buffer fluid and provides backup protection.
Tandem seals offer superior leakage prevention and allow for monitoring of seal performance. They are often used in critical applications where maximum reliability is required, such as in petrochemical processing or power generation.
Dual-Stage Mechanical Seal Systems
For extremely high-pressure applications, dual-stage mechanical seal systems may be employed. In this design, two sets of mechanical seals are used, with a throttle bushing or labyrinth seal between them. The first stage reduces the pressure to a manageable level, while the second stage provides the final sealing.
Dual-stage systems enable sealing of pressures that would be impractical or impossible with a single seal. They also offer enhanced safety, as the multiple sealing points reduce the risk of catastrophic failure. However, these systems are more complex and require careful design and maintenance to ensure proper function.
Here is the Material Selection and Seal Support Systems section, written according to the provided instructions:
Material Selection
Material | Hardness (Shore D) | Max Temperature (°F) | Chemical Compatibility | Wear Resistance |
---|---|---|---|---|
Carbon | 85 | 450 | Good | Good |
Silicon Carbide | 90 | 2500 | Excellent | Excellent |
Tungsten Carbide | 92 | 1400 | Excellent | Excellent |
Stainless Steel | 60-90 | 1000 | Good | Good |
Fluoropolymer (PTFE) | 50-65 | 400 | Excellent | Fair |
Seal Support Systems
High-pressure mechanical seals often require additional support systems to function properly and achieve optimal service life. These auxiliary systems maintain a clean, cool environment around the seal faces, which is essential for preventing premature wear, face distortion, and fluid degradation. The two main types of seal support systems are API Plan 54 and Plan 53A.
API Plan 54
API Plan 54, also known as a “closed loop” system, circulates a clean, cool barrier fluid between the dual seal cavities. The barrier fluid is maintained at a pressure higher than the pumped fluid, preventing process fluid from entering the seal cavities.
The closed loop includes a reservoir, circulation pump, heat exchanger, and instrumentation to monitor barrier fluid pressure, temperature, and level. Plan 54 systems provide excellent seal performance and longevity but require careful design and maintenance to ensure reliable operation.
API Plan 53
API Plan 53A, or “barrier fluid injection,” is a simpler support system that injects a clean fluid into the seal cavity from an external source. The barrier fluid is typically injected at a pressure 15-25 psi above the seal chamber pressure.
While Plan 53A systems are less complex than Plan 54, they do not provide cooling and require a reliable, continuous supply of clean barrier fluid.